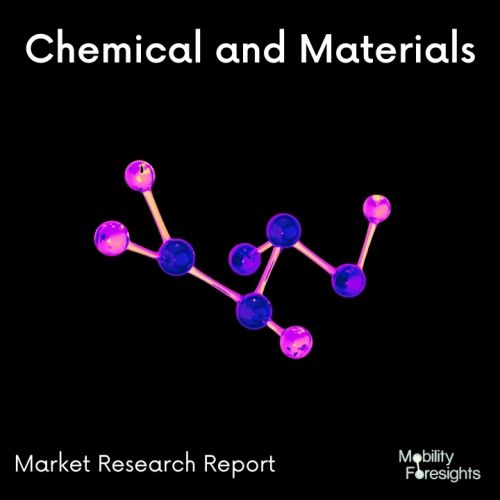
- Get in Touch with Us
Last Updated: Apr 25, 2025 | Study Period: 2024-2030
The portfolio of polyphenylene sulfide (PPS) products has outstanding heat and chemical resistance and is designed specifically for electronic applications.
In addition, the PPS portfolio includes a wide range of engineering compounds that have been formulated with either mineral filler or glass fiber to meet a variety of desired characteristics for home electronics, general electronic components, and principal electronic components.
PPS delivers elevated temperature performance, precision moldability, and dimensional stability to withstand the SMT process, along with the required UL V-0 flame resistance without incorporating flame retardant additives. Additionally, available elastomer modified grades offer outstanding heat shock resistance and enhanced impact properties.
These characteristics make PPS an ideal injection molding product for use in producing electrical and electronic parts such as connectors, electronic control modules and sensors.It is mainly used in LCD projection TV lamp housings ; Microwave parts ; Electromagnetic cooker coil bases ; Lamp sockets ; Hair dryer nozzles ; Steam iron parts.
The Global Home electronics PPS resin market accounted for $XX Billion in 2023 and is anticipated to reach $XX Billion by 2030, registering a CAGR of XX% from 2024 to 2030.
Toray Develops New Home electronics PPS Resin with Worldâs Highest Flexibility Level
By optimizing the polymer structure with its innovative material design based on a technology database accumulated over many years and the alloy precise control technology based on its proprietary nanoalloy technology, Toray was successful in developing the novel PPS resin with the highest flexibility level in the worldâ1,200 MPa or less in elastic modulus.
The new PPS resin's mechanical strength remains unaltered even after 1,000 hours of treatment at 170°C. Additionally, it has been demonstrated to be highly resistant to acids and vehicle coolants, which is necessary in the actual operating environment. In addition, the business has been working to improve resin property optimization and verify processability for use in automobile piping.
It is anticipated that the newly developed PPS resin will make it possible to use resin for automobile piping, which has not been possible up until this point, reduce the number of components used, and simplify the process.
Toray has already started recommending the material for use in automobile piping and is working on setting up a production system for the resin so that the material can be widely promoted.
Sl no | Topic |
1 | Market Segmentation |
2 | Scope of the report |
3 | Abbreviations |
4 | Research Methodology |
5 | Executive Summary |
6 | Introduction |
7 | Insights from Industry stakeholders |
8 | Cost breakdown of Product by sub-components and average profit margin |
9 | Disruptive innovation in the Industry |
10 | Technology trends in the Industry |
11 | Consumer trends in the industry |
12 | Recent Production Milestones |
13 | Component Manufacturing in US, EU and China |
14 | COVID-19 impact on overall market |
15 | COVID-19 impact on Production of components |
16 | COVID-19 impact on Point of sale |
17 | Market Segmentation, Dynamics and Forecast by Geography, 2024-2030 |
18 | Market Segmentation, Dynamics and Forecast by Product Type, 2024-2030 |
19 | Market Segmentation, Dynamics and Forecast by Application, 2024-2030 |
20 | Market Segmentation, Dynamics and Forecast by End use, 2024-2030 |
21 | Product installation rate by OEM, 2023 |
22 | Incline/Decline in Average B-2-B selling price in past 5 years |
23 | Competition from substitute products |
24 | Gross margin and average profitability of suppliers |
25 | New product development in past 12 months |
26 | M&A in past 12 months |
27 | Growth strategy of leading players |
28 | Market share of vendors, 2023 |
29 | Company Profiles |
30 | Unmet needs and opportunity for new suppliers |
31 | Conclusion |
32 | Appendix |