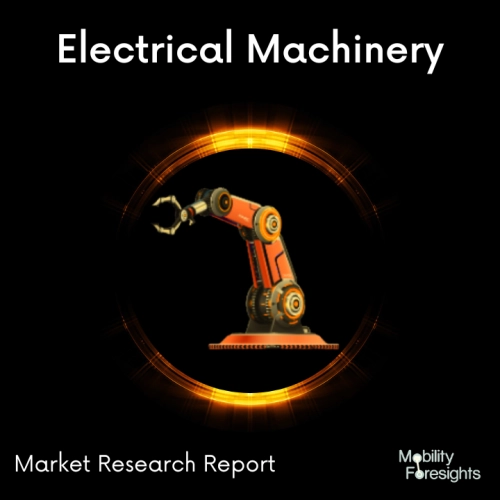
- Get in Touch with Us
Last Updated: Apr 25, 2025 | Study Period: 2024-2030
A machining centre with its spindle oriented horizontally is referred to as a horizontal machining centre (HMC). This machining center's layout encourages continuous production.
One explanation for this is that the horizontal arrangement makes it easier for chips to drop off the table since they are more likely to do so.
Slots and grooves are frequently milled using horizontal machining centres. Flat surfaces can also be shaped with it. The spindle axis of vertical machining centres is vertically orientated.It revolves on its axis while having its milling cutters held in the spindle.
An CNC machine known as a "machining centre" is able to mill, drill, bore, tap, and carry out a variety of other tasks without modifying the attachment of the work piece. It is capable of automatically bringing a wide range of different tools to the worksite.
Depending on the machine, horizontal milling machines can make several cuts at once and cut more quickly. When facing and pocketing, chips can also be taken off more quickly. For lengthy or significant production runs, horizontal milling machines are useful due to the enhanced speed and precision.
Business expands by acquiring a rival firm in a related industry at the same point in the supply chain, this process is known as horizontal integration.
Vertical integration is the process through which a company grows by purchasing a firm that comes before or after it in the supply chain.
The process of machining involves cutting away material, usually metal, to produce components for tools, machinery, transportation, and other things. Machine shops and machinists transform raw materials into useful tools by making accurate cuts using tools like lathes, mills, and drill presses.
The Global Horizontal Machining center market accounted for $XX Billion in 2023 and is anticipated to reach $XX Billion by 2030, registering a CAGR of XX% from 2024 to 2030.
The fourth generation of Heller's four-axis horizontal machining centres is now available. According to claims, this generation provides less idle time, better milling performance, quicker service, and more adaptable adaptation to user needs.
It is claimed to deliver great basic accuracy and surface finishes, and it has a modular architecture. The update series has ergonomic characteristics such low loading sills, minimal overhangs, and the ability of overhead loading.
It also incorporates a touch-sensitive operation panel with critical functions. At the setup stations and inside the work area, integrated LED illumination is the norm.
Power and Speed are the two equipment packages for drive technology that are offered. The Power package is intended for cutting steel and other challenging-to-machine materials in medium batch sizes.For high-volume machining of cast iron, aluminium, and other light metals, the Speed package is appropriate.
The AutoSet technology cycle for weight-dependent dynamic Z-axis and B-axis adjustment is part of the Speed package and is intended to optimise axis dynamics in relation to the load capacity. Additionally, depending on spindle size, it has shorter spindle run-up times, which range from 1.4 to 2.6 seconds.
Sl no | Topic |
1 | Market Segmentation |
2 | Scope of the report |
3 | Abbreviations |
4 | Research Methodology |
5 | Executive Summary |
6 | Introduction |
7 | Insights from Industry stakeholders |
8 | Cost breakdown of Product by sub-components and average profit margin |
9 | Disruptive innovation in the Industry |
10 | Technology trends in the Industry |
11 | Consumer trends in the industry |
12 | Recent Production Milestones |
13 | Component Manufacturing in US, EU and China |
14 | COVID-19 impact on overall market |
15 | COVID-19 impact on Production of components |
16 | COVID-19 impact on Point of sale |
17 | Market Segmentation, Dynamics and Forecast by Geography, 2024-2030 |
18 | Market Segmentation, Dynamics and Forecast by Product Type, 2024-2030 |
19 | Market Segmentation, Dynamics and Forecast by Application, 2024-2030 |
20 | Market Segmentation, Dynamics and Forecast by End use, 2024-2030 |
21 | Product installation rate by OEM, 2023 |
22 | Incline/Decline in Average B-2-B selling price in past 5 years |
23 | Competition from substitute products |
24 | Gross margin and average profitability of suppliers |
25 | New product development in past 12 months |
26 | M&A in past 12 months |
27 | Growth strategy of leading players |
28 | Market share of vendors, 2023 |
29 | Company Profiles |
30 | Unmet needs and opportunity for new suppliers |
31 | Conclusion |
32 | Appendix |