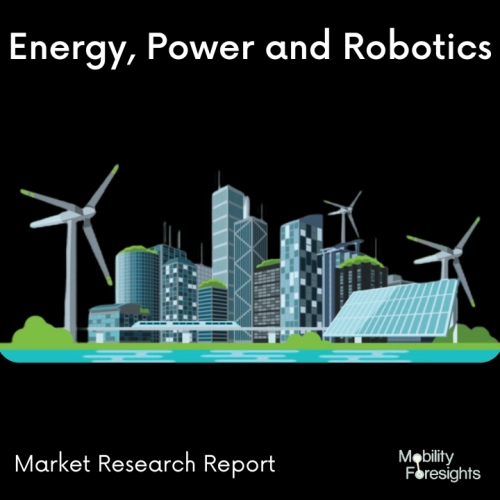
- Get in Touch with Us
Last Updated: Apr 25, 2025 | Study Period:
Hydrogen electrolyzers are advanced devices that divide water into valuable Hydrogen and Oxygen. Like fuel cells, electrolyzers consist of an anode and a cathode separated by an electrolyte. Different electrolyzers function in different ways, mainly due to the different type of electrolyte material involved and the ionic species it conducts
Electrolyzers can range in size from small, appliance-size equipment that is well-suited for small-scale distributed hydrogen production to large-scale, central production facilities that could be tied directly to renewable or other non-greenhouse-gas-emitting forms of electricity production.
There are three main types of hydrogen electrolyzersâalkaline, polymer electrolyte membrane (PEM), and solid oxide. PEM electrolyzers are valued because of their greater energy efficiency, wider operating temperature, and easier maintenance relative to other kinds of hydrogen electrolyzer. The alkaline electrolyzer uses a liquid alkaline electrolyte. The water in this electrolyte is split into hydrogen and hydroxide ions at the cathode pole. These ions are then brought into contact with a membrane, after which they are oxidized to water and oxygen at the anode pole
A Solid Oxide Electrolysis Cell (SOEC ) is basically the corresponding fuel cell (Solid Oxide Fuel Cell â SOFC) run in âreverseâ. Such a cell operates at relatively high temperatures (700-1000 °C), which makes the efficiency very high. Therefore, High-temperature solid oxide electrolyzer cell (SOEC) has great potential for efficient and economical production of hydrogen fuel.
The largest Hydrogen electrolyzers market is China, which has installed more renewable power than any other country. With lower capital expenditure costs, China produces 40% of the world's electrolyzers. Additionally, state-owned firms have pledged to build an extensive 6,000-kilometer network of pipelines for green hydrogen transportation by 2050
Europeâs cumulative deployments are accelerating, and deployment plans are growing year after year. The EU is strong on regulatory framework with funding and financing support schemes and European companies have a strong presence as international patent holders. When it comes to high value inventions, EU is still leading with (31% of total share) alongside Japan. Europe is active in R&D actions spanning the whole continent and has a leading global scientific publication record together with China and the US.Several companies have announced new hydrogen deals in Europe, as Germany moves forward on hydrogen collaboration with Australia and the United Arab Emirates
In the United States, in October 2023, the Biden administration announced $7 billion for the countryâs first clean hydrogen hubs, and the U.S. Department of Energy further allocated $750 million for 52 projects across 24 states to dramatically reduce the cost of clean hydrogen and establish American leadership in the industry. U.S. also has the H2NEW which is a consortium of nine U.S. Department of Energy (DOE) national laboratories focused on making large-scale electrolyzers, which produce hydrogen from electricity and water, more durable, efficient, and affordable
Electrolysis is a leading hydrogen production pathway to achieve the Hydrogen Energy Earthshot goal of reducing the cost of clean hydrogen by 80% to $1 per 1 kilogram in 1 decade. Meeting the Hydrogen Shot clean hydrogen cost target of $1/kg H2by 2030 (and interim target of $2/kg H2by 2025) through improved understanding of performance, cost, and durability trade-offs of electrolyzer systems under predicted future dynamic operating modes using CO2-free electricity.
In 2023, the hydrogen industry announced over 1,000 large-scale projects requiring electrolyzer capacities of more than 1 MW. Among these projects, 795 aim to be fully or partially commissioned by 2030. Alkaline and PEM (proton exchange membrane) electrolyzers are already commercially available. Alkaline electrolyzers are a more mature technology with a long history of deployment in the chlor-alkali industry.
Solid Oxide Electrolysis (SOEC) is quickly approaching commercialization. In April 2023, a 2.6 MW SOEC electrolyzer was installed in a Neste refinery in the Netherlands, becoming the biggest at that time. A few weeks later, the record was broken with a 4 MW SOEC system installed in a NASA research center in California. Bloom Energy increased its SOEC manufacturing capacity in 2022 with a new high-volume line in Newark, moving towards GW-scale operations in the United States. Topsoe is advancing the construction of an industrial-scale 500 MW/yr manufacturing facility in Denmark, expected to be online in 2025.
This commitment is also underscored by the significant funding and grants that many governments have announced, including the EU 1 billion funding by the European Commission under the Horizon Europe program for green hydrogen projects.
The next major hurdle in achieving low-cost green hydrogen is to reduce the investment cost of the electrolyzer. Researchers are aiming for a reduction of up to 80% in the investment cost of the electrolyzer. They could produce green hydrogen at less than USD 2.5/kgH2 in the coming five to ten years, and at less than USD 1/kgH2 before 2040 in a scenario with an ambitious electrolyzer deployment
The market is exposed to several risks that may impact its expansion. One of the major risks is the concern of Severe overcapacity, Electrolyser manufacturers have invested too quickly into new factories, with âsevere overcapacityâ compared to actual demand from green hydrogen project developers in the coming year
The high initial capital expenditure required for setting up Hydrogen electrolyzer systems is another concern. Even with the reductions in cost, dependence on rare materials for catalysts, such as Titanium And Nickel, is a risk because these materials are very easily subjected to price fluctuation and supply chain disruption. Moreover, the continuous technological improvements required by industry to ensure efficiency and lower costs underline the fact that further research development investment is required and integral to market viability in the long term.
A producer of hydrogen electrolyzers named EH2 has declared plans to construct a new production facility in Massachusetts that may nearly triple the existing global capacity for producing hydrogen electrolyzers.
Proton exchange membrane electrolyzers with a capacity of 100MW will be produced at the facility, which is significantly larger than the more prevalent 1MW and 5MW units currently on the market.EH2 thinks that by using greater machinery, it will be able to better serve the needs of sectors including chemical manufacture, steel manufacturing, and cement manufacturing.
A second plant is also being planned by the corporation, though no deadline has been set. The first plant is anticipated to start producing equipment for demonstration purposes, and the following year, full production will be achieved.Before the Biden administration unveiled the Inflation Reduction Act, EH2 was already developing a future for the production of hydrogen electrolyzers.
Now, it wants to exploit economies of scale to produce larger proton exchange membrane electrolyzers, which will lower the cost of H2 synthesis. Instead of the 1MW and 5MW units that are more prevalent on the market today, they want to develop 100 MW units.In addition, the company plans to create electrolyzers that will enable and accelerate the synthesis of H2 based on the accessibility of sporadic renewable electricity sources. In terms of what is required in the sector, in terms of what is necessary if one is genuinely going to address steel, cement, and chemical manufacture, electrolyzers are currently accessible on a scale that makes it very difficult to bring them to what is needed.
The electrolyzer needs to be substantially larger in size. Dean added that despite this, the company started receiving more orders from clients looking for the equipment they require for planned green H2 production facilities as a result of the new production tax credits for low-carbon H2 and the Inflation Reduction Act.
Due to this increase in demand, EH2 sped up the completion of its first factory and began organising the building of a second. In Germany, Shell introduced a hydrogen electrolyzer. According to Shell, the project, which is supported by a European consortium and is located at the company's energy and chemicals park in Rheinland, would "accelerate hydrogen production and contribute to Europe's goal to achieve climate neutrality."
According to a statement from Shell, the fully operating facility is the first to employ this technology on such a massive scale in a refinery. It is a member of the Refine European consortium and is funded by the European Commission under the fuel cells and hydrogen joint project. At the Rhineland location, where Shell also wants to eventually generate sustainable aviation fuel using renewable energy and biomass, plans are also underway to increase the polymer electrolyte membrane (PEM) electrolyzer's capacity from 10 megawatts to 100 megawatts.
Manufacturer | Model | Key Features | Launch Date | Region |
Siemens Energy | SilySix | - High-efficiency PEM electrolyzer with a modular design for scalability (up to 500 MW) - Targets large-scale green hydrogen production facilities - Emphasizes durability and long-term operational efficiency | 2023 | Europe |
Nel Hydrogen | A Series | - High-pressure alkaline electrolyzer designed for containerized deployment - Offers fast installation and easy transportation for on-site hydrogen generation - Targets industrial applications and fueling stations | -2023 | Global |
McPhy | McLyzer Mega | - Large-scale alkaline electrolyzer with a capacity of 20 MW - Suitable for industrial-scale hydrogen production facilities - Focuses on compactness and ease of maintenance | 2024 | North America |
IHI Corporation | Advanced High-Efficiency Electrolyzer (AHEE) | - Next-generation PEM electrolyzer boasting superior efficiency and lower operating costs - Targets large-scale green hydrogen production projects - Pioneering advancements in PEM technology | 2023 | Asia Pacific |
Green Hydrogen Systems | HRSING | - Solid oxide electrolyzer (SOE) designed for high-temperature operation and efficient hydrogen production - Offers potential for integration with renewable energy sources like concentrated solar power - Focuses on innovation and future potential of SOE technology | 2024 | Global |
Sl No | Company | Product Description | Analyst View |
1.1 | Enapter AG | Enapter AG expands its product portfolio with âAEM Flex 120â electrolyzer for a streamlined launch of industrial and refueling hydrogen projects. The AEM Flex 120 features up to 50 AEM Stack core modules, ensuring flexible operation and high reactivity to fluctuating renewable energy. | This launch not only showcases their technological expertise but also demonstrates theiractive role in shaping a greener future. |
2. | thyssenkrupp nucera | Introduced a new product name for its innovative solution for the production of green hydrogen. This 20 MW module will henceforth be called âscalumâ. The supplier of world-leading technologies for high-efficiency electrolysis plants announced this at the international industry trade fair âWorld Hydrogen Summit 2023â in Rotterdam. | This name change is likely a strategic marketing move to make their product more memorable and accessible to a wider audience. "Scalum" is easier to remember and pronounce than the technical term, potentially increasing brand recognition and marketability. |
3. | SANY Hydrogen | The hydrogen energy subsidiary of SANY, has announced the grand launch of t worldâs largest single hydrogen electrolyzer. The new S-series square electrolyzer can produce 3,000 standard cubic meters of hydrogen per hour using renewable electricity. This milestone accelerates the adoption of clean energy technologies by industries and marks progress in SANY's efforts to fuel the shift to greener solutions. | This launch not only showcases their technological expertise but also demonstrates theiractive role in shaping a greener future. |
The competitive landscape in the market has shaped up due to the activities of key players, together with their product launches, mergers and acquisitions, and pricing strategies. Companies like NEL, Plug Power, Linde Engineering, and Siemens Energy are increasingly focusing on innovation and differentiation, with strategic product launches aimed at meeting evolving consumer demands.
Mergers and acquisitions are being employed to enhance market share and expand capabilities, reflecting a trend toward consolidation in the industry. For instance, ITM is partnering with Mott Corporation to cement ITM's market leadership in electrolyzer stack technology.
Variations in Product Pricing often come from differences in technology, brand positioning, and production costs, which influence consumer choices and competitive dynamics. Thismixed approach highlights that the market is both dynamic and competitive, with companies continually adapting their strategies to maintain a competitive edge.
Sl no | Topic |
1 | Market Segmentation |
2 | Scope of the report |
3 | Research Methodology |
4 | Executive summary |
5 | Key Predictions of the Hydrogen Electrolyzer Market |
6 | Avg B2B price of Hydrogen Electrolyzer Market, By Region |
7 | Major Drivers For Hydrogen Electrolyzer Market |
8 | Global Hydrogen Electrolyzer Market Production Footprint - 2023 |
9 | Technology Developments In Hydrogen Electrolyzer Market |
10 | New Product Development In Hydrogen Electrolyzer Market |
11 | Research focus areas on new Hydrogen Electrolyzer |
12 | Key Trends in the Hydrogen Electrolyzer Market |
13 | Import And Export of Hydrogen As Fuel and Impact on Hydrogen electrolyzer market |
14 | Regulations, and Incentives for Hydrogen Electrolyzer Market, By Region |
15 | Major Projects Utilizing Hydrogen Electrolyzer |
16 | Market Size, Dynamics And Forecast, By Geography, 2024-2030 |
17 | Market Size, Dynamics And Forecast, By Type, 2024-2030 |
18 | Market Size, Dynamics And Forecast, By Output, 2024-2030 |
19 | Market Size, Dynamics And Forecast, By End User, 2024-2030 |
20 | Competitive Landscape Of Hydrogen Electrolyzer Market |
21 | Mergers and Acquisitions |
22 | Competitive Landscape |
23 | Growth strategy of leading players |
24 | Market share of vendors, 2023 |
25 | Company Profiles |
26 | Unmet needs and opportunity for new suppliers |
27 | Conclusion |