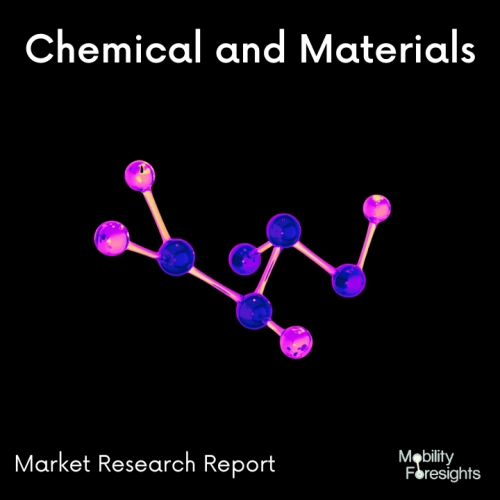
- Get in Touch with Us
Last Updated: Apr 25, 2025 | Study Period: 2024-2030
A particularly pure variety of hydrogen chloride is called hyperpure hydrogen chloride (HCl). It is frequently applied as a silicon wafer and other semiconductor materials' cleaning agent in the semiconductor sector.
High purity chemicals are necessary in the semiconductor sector to reduce contamination and guarantee maximum device performance. When cleaning semiconductor wafer surfaces of organic and inorganic impurities, hyperpure HCl is frequently utilised.
Technical grade HCl is frequently used to make hyperpure HCl, which is distinguished by its high degree of purity, usually greater than 99.999%.
It is also utilised in several industrial and chemical processes, including those that create organic molecules, catalysts, and other materials.
A hydrogen halide is the substance hydrogen chloride, which has the chemical formula HCl. It is a colourless gas at room temperature that reacts with water vapour in the air to produce white fumes of hydrochloric acid. At normal temperature and pressure, hydrogen chloride (HCl), a gas composed of the elements hydrogen and chlorine, is a gas.
Hydrochloric acid is the name given to a gaseous solution in water. Numerous processes and products are refined and made using hydrogen chloride, including cleaning, pickling, electroplating metals, tanning leather, and cleaning. Burning many plastics can result in the formation of hydrogen chloride.
The global Hyperpure Hydrogen Chloride market accounted for $XX Billion in 2022 and is anticipated to reach $XX Billion by 2030, registering a CAGR of XX% from 2024 to 2030.
One of WACKER's primary competitive advantages is the highly integrated material loops at its major locations in Burghausen, Nünchritz, and Zhangjiagang. Essentially, integrated production entails utilising waste resources from one step as raw materials for another.
Energy-intensive processes are needed to produce hydrogen chloride. The conversion of the chlorine-containing intermediates to the chlorine-free end products in WACKER's integrated material loop results in the recovery of both hydrogen chloride and a portion of the energy in the form of heated steam (such as silicones, hyperpure silicon or pyrogenic silica).
The recovered hydrogen chloride is then used again in the manufacturing loop. Due to lessening raw material consumption, this closed material loop also cuts down on shipment trips and emissions.
Sl no | Topic |
1 | Market Segmentation |
2 | Scope of the report |
3 | Abbreviations |
4 | Research Methodology |
5 | Executive Summary |
6 | Introduction |
7 | Insights from Industry stakeholders |
8 | Cost breakdown of Product by sub-components and average profit margin |
9 | Disruptive innovation in the Industry |
10 | Technology trends in the Industry |
11 | Consumer trends in the industry |
12 | Recent Production Milestones |
13 | Component Manufacturing in US, EU and China |
14 | COVID-19 impact on overall market |
15 | COVID-19 impact on Production of components |
16 | COVID-19 impact on Point of sale |
17 | Market Segmentation, Dynamics and Forecast by Geography, 2024-2030 |
18 | Market Segmentation, Dynamics and Forecast by Product Type, 2024-2030 |
19 | Market Segmentation, Dynamics and Forecast by Application, 2024-2030 |
20 | Market Segmentation, Dynamics and Forecast by End use, 2024-2030 |
21 | Product installation rate by OEM, 2023 |
22 | Incline/Decline in Average B-2-B selling price in past 5 years |
23 | Competition from substitute products |
24 | Gross margin and average profitability of suppliers |
25 | New product development in past 12 months |
26 | M&A in past 12 months |
27 | Growth strategy of leading players |
28 | Market share of vendors, 2023 |
29 | Company Profiles |
30 | Unmet needs and opportunity for new suppliers |
31 | Conclusion |
32 | Appendix |