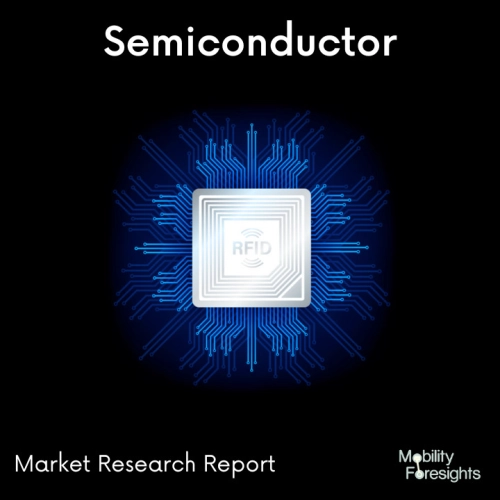
- Get in Touch with Us
Last Updated: Apr 25, 2025 | Study Period: 2024-2030
IC packaging materials are used to protect and support integrated circuits (ICs) during manufacturing, assembly, and use. They also provide electrical and thermal connections between the IC and the outside world.
The most common IC packaging materials are ceramic, plastic, and metal. Ceramic materials are strong and can withstand high temperatures, making them ideal for high-power and high-frequency ICs.
Plastic materials are lightweight and inexpensive, making them ideal for low-power and low-frequency ICs. Metal materials are good conductors of heat and electricity, making them ideal for ICs that require good thermal management.
The choice of IC packaging material depends on the specific requirements of the IC. For example, a high-power IC that will be used in a harsh environment will require a different packaging material than a low-power IC that will be used in a benign environment.
IC packaging materials are an important part of the IC manufacturing process. They protect the IC from damage and provide the necessary electrical and thermal connections. The choice of IC packaging material is based on the specific requirements of the IC.
In addition to the three most common materials, there are a number of other materials that can be used for IC packaging, such as glass, composites, and even paper. The choice of material will depend on the specific requirements of the IC and the application in which it will be used.
IC packaging materials are constantly being developed and improved. New materials are being developed to meet the ever-increasing demands of IC technology.IC packaging materials protect and support ICs during manufacturing, assembly, and use.
They provide electrical and thermal connections between the IC and the outside world. The choice of material depends on the IC's requirements.The material that houses a semiconductor device is referred to as IC packaging.
The package is a casing that protects the circuit material from corrosion or physical damage while also allowing attachment of the electrical connections that link it to the printed circuit board (PCB).
There are many various types of integrated circuits, and therefore multiple types of IC packaging system designs to consider, because different types of circuit designs will have varied demands for their outer shell.
The final stage in the fabrication of semiconductor devices is IC packaging. During this critical stage, the semiconductor block is wrapped in a container that protects the IC from potentially harmful exterior factors as well as the corrosive effects of age.
The package is simply an encasement meant to preserve the block while also promoting the electrical connections that send signals to an electronic device's circuit board.
Since the 1970s, when ball grid array (BGA) packages were initially used by electronics packaging makers, IC packaging technology has progressed. At the turn of the century, innovative packaging technologies, especially the plastic quad flat pack and the thin tiny outline package, surpassed pin grid array products.
As the decade proceeded, manufacturers such as Intel heralded the era of land grid array packages.Meanwhile, flip-chip ball grid arrays (FCBGAs), which have a higher pin count than other package designs, have surpassed BGAs. The FCBGA comprises input and output signals that span the whole die.
The Global IC Packaging Materials Market accounted for $XX Billion in 2023 and is anticipated to reach $XX Billion by 2030, registering a CAGR of XX% from 2024 to 2030.
Tera View is thrilled to announce the release of the EOTPR 4500, a purpose-built integrated circuit package inspection machine.The auto probe technology we developed to tackle the demands of the most sophisticated IC packaging technology, supporting substrate sizes up to 150mmx150mm while enhancing probe tip placement precision to +/- 0.5 m, is the core feature of the EOTPR 4500.
Our clients may now probe very large chip-let devices with landing contact sizes of less than 5 m, such as copper pillars and TSV tips, using the new auto prober. We worked closely with a big advanced packaging client to design this product, and it has completed a rigorous beta site testing phase at this customer site to confirm that the new product works properly.
The probe stations are insufficient to fulfill the need for IC package probing, which differs from wafer probing in that wafer surfaces are fully flat. This implies that wafer-based probe stations can crush or stress probing points like TSVs, or that the probe tip must fall excruciatingly slowly to prevent introducing artifacts into the target sample.
This solution enables our clients to isolate defects in their most modern IC packaging devices while benefiting from EOTPR's industry-leading distance-to-defect capabilities of less than 5 m.
It also provides a device under test (DUT) heater that can reach temperatures of up to 250 °C, which implies that customers working on sophisticated graphics engines or autonomous driving AI engines may now use it.
Sl no | Topic |
1 | Market Segmentation |
2 | Scope of the report |
3 | Abbreviations |
4 | Research Methodology |
5 | Executive Summary |
6 | Introduction |
7 | Insights from Industry stakeholders |
8 | Cost breakdown of Product by sub-components and average profit margin |
9 | Disruptive innovation in the Industry |
10 | Technology trends in the Industry |
11 | Consumer trends in the industry |
12 | Recent Production Milestones |
13 | Component Manufacturing in US, EU and China |
14 | COVID-19 impact on overall market |
15 | COVID-19 impact on Production of components |
16 | COVID-19 impact on Point of sale |
17 | Market Segmentation, Dynamics and Forecast by Geography, 2024-2030 |
18 | Market Segmentation, Dynamics and Forecast by Product Type, 2024-2030 |
19 | Market Segmentation, Dynamics and Forecast by Application, 2024-2030 |
20 | Market Segmentation, Dynamics and Forecast by End use, 2024-2030 |
21 | Product installation rate by OEM, 2023 |
22 | Incline/Decline in Average B-2-B selling price in past 5 years |
23 | Competition from substitute products |
24 | Gross margin and average profitability of suppliers |
25 | New product development in past 12 months |
26 | M&A in past 12 months |
27 | Growth strategy of leading players |
28 | Market share of vendors, 2023 |
29 | Company Profiles |
30 | Unmet needs and opportunity for new suppliers |
31 | Conclusion |
32 | Appendix |