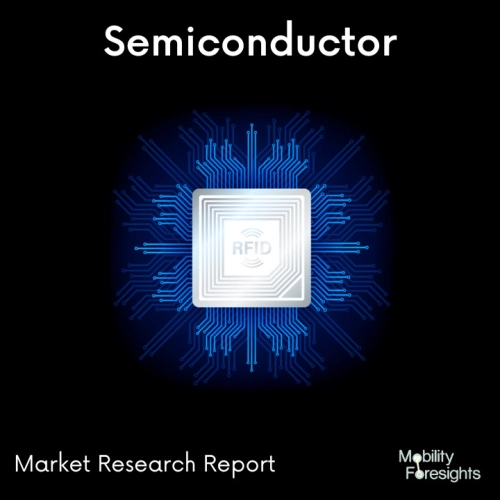
- Get in Touch with Us
Last Updated: Apr 25, 2025 | Study Period:
The IC (Integrated Circuit) test interface is a crucial element in the semiconductor manufacturing process, responsible for ensuring the functionality and quality of integrated circuits before they are deployed in electronic devices.
With the increasing complexity and miniaturization of ICs, testing becomes even more critical to identify defects and guarantee the reliability of the final products.
This comprehensive process involves various techniques and technologies, encompassing both design-for-testability considerations and the physical connections between the test equipment and the ICs.
At the heart of the IC test interface lies the Design-for-Testability (DFT) approach, which involves incorporating specific design features in the IC layout to facilitate easier and more efficient testing.
DFT encompasses several methodologies, including built-in self-test (BIST), scan chains, and boundary scan. BIST allows the IC to generate test patterns and evaluate its own functionality, reducing the need for external test equipment during production testing.
Scan chains, on the other hand, are shift registers integrated into the IC design, enabling the serial loading of test patterns and the observation of output responses, streamlining the testing process.
Boundary scan, defined by the IEEE 1149.1 standard (also known as JTAG), provides a standardized method to test and configure ICs, particularly those with a high pin count, by accessing internal circuitry through dedicated boundary scan cells.
Once the IC design incorporates DFT features, the physical IC test interface comes into play during the testing phase. This interface acts as a bridge between the external test equipment and the IC's internal circuitry.
It is typically realized through test pads or test pins located on the IC's package, allowing the test equipment to connect to various internal nodes and perform functional and parametric tests.
The test interface serves as the conduit for test data, control signals, and power supply, enabling communication with the IC during testing.The test pads or pins are strategically placed on the IC layout based on the DFT considerations to ensure comprehensive test coverage.
The number of test pads and their arrangement depends on the complexity of the IC and the testing requirements. For modern ICs, with hundreds or even thousands of pins, the physical arrangement of test pads becomes a significant challenge.
Designers must carefully plan the placement of test pads to maximize test coverage while considering the limited space available on the IC package.In addition to test pads, there are different test interface standards used in the industry, such as the Joint Test Action Group (JTAG) standard (IEEE 1149.1), the IEEE 1500 standard for embedded core test, and various proprietary interfaces developed by semiconductor companies.
These standards define the protocols and methodologies for accessing and testing ICs, ensuring compatibility between different test equipment and ICs from various manufacturers.
As the complexity of ICs continues to increase, especially with the advent of System-on-Chip (SoC) designs, the IC test interface faces additional challenges. SoCs often integrate multiple functional blocks, including processors, memory, and various peripherals, onto a single chip.
Testing such complex designs requires efficient access to each functional block and thorough verification of their interactions. Advanced test interfaces and methodologies, such as hierarchical testing and hierarchical DFT, have emerged to address these challenges.
Hierarchical testing allows testing individual blocks separately before testing the complete SoC, while hierarchical DFT extends DFT techniques to hierarchical designs.
Moreover, testing ICs for manufacturing defects is not the only purpose of the IC test interface. It is also instrumental in various stages of product development, including design validation and characterization.
During the design validation phase, engineers use the test interface to verify the correctness of the IC's functionality before committing to mass production. Characterization involves analyzing the IC's performance under various conditions to establish its operating limits and ensure it meets the required specifications.
In summary, the IC test interface plays a vital role in semiconductor manufacturing by enabling efficient and comprehensive testing of integrated circuits. It incorporates DFT features in the IC design and facilitates physical connections between external test equipment and the IC's internal circuitry.
Through strategic placement of test pads and adherence to test interface standards, it ensures thorough testing and reliable functionality of ICs. As semiconductor technology advances, the IC test interface will continue to evolve, adapting to the increasing complexity of IC designs and the demands for higher performance and reliability in electronic devices.
The Global IC Test Interface Market accounted for $XX Billion in 2022 and is anticipated to reach $XX Billion by 2030, registering a CAGR of XX% from 2023 to 2030.
Advantest's V93000 platform is a modular, scalable, and high-performance IC test platform that can be used to test a wide range of devices, including memory, logic, and mixed-signal chips.
The platform features a number of innovative technologies, including a new vector-based architecture that provides high throughput and low latency, and a new digital interface that supports a wide range of protocols.
The V93000 platform is also designed to be highly scalable, so it can be easily expanded to meet the needs of future test applications. The platform is available in a variety of configurations, from small, single-station systems to large, multi-station systems.
Keysight Technologies' XiPalladium platform is a high-performance IC test platform that is designed for the testing of complex and demanding devices. The platform features a number of innovative technologies, including a new vector-based architecture that provides high throughput and low latency, and a new digital interface that supports a wide range of protocols.
The XiPalladium platform is also designed to be highly scalable, so it can be easily expanded to meet the needs of future test applications. The platform is available in a variety of configurations, from small, single-station systems to large, multi-station systems
.
Microsemi's Fusion Test Platform is a modular, scalable, and high-performance IC test platform that can be used to test a wide range of devices, including memory, logic, and mixed-signal chips.
The platform features a number of innovative technologies, including a new vector-based architecture that provides high throughput and low latency, and a new digital interface that supports a wide range of protocols.
The Fusion Test Platform is also designed to be highly scalable, so it can be easily expanded to meet the needs of future test applications. The platform is available in a variety of configurations, from small, single-station systems to large, multi-station systems.
Sl no | Topic |
1 | Market Segmentation |
2 | Scope of the report |
3 | Abbreviations |
4 | Research Methodology |
5 | Executive Summary |
6 | Introduction |
7 | Insights from Industry stakeholders |
8 | Cost breakdown of Product by sub-components and average profit margin |
9 | Disruptive innovation in the Industry |
10 | Technology trends in the Industry |
11 | Consumer trends in the industry |
12 | Recent Production Milestones |
13 | Component Manufacturing in US, EU and China |
14 | COVID-19 impact on overall market |
15 | COVID-19 impact on Production of components |
16 | COVID-19 impact on Point of sale |
17 | Market Segmentation, Dynamics and Forecast by Geography, 2023-2030 |
18 | Market Segmentation, Dynamics and Forecast by Product Type, 2023-2030 |
19 | Market Segmentation, Dynamics and Forecast by Application, 2023-2030 |
20 | Market Segmentation, Dynamics and Forecast by End use, 2023-2030 |
21 | Product installation rate by OEM, 2023 |
22 | Incline/Decline in Average B-2-B selling price in past 5 years |
23 | Competition from substitute products |
24 | Gross margin and average profitability of suppliers |
25 | New product development in past 12 months |
26 | M&A in past 12 months |
27 | Growth strategy of leading players |
28 | Market share of vendors, 2023 |
29 | Company Profiles |
30 | Unmet needs and opportunity for new suppliers |
31 | Conclusion |
32 | Appendix |