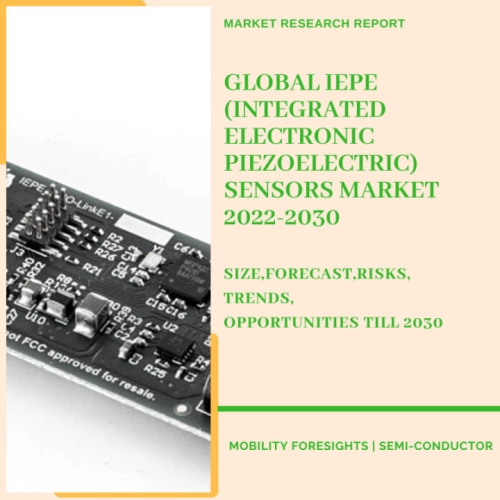
- Get in Touch with Us
Last Updated: Apr 25, 2025 | Study Period: 2022-2030
Integrated electronic piezoelectric is the sensitive piezoelectric sensor that must adhere to a technical standard that calls for them to have integrated active impedance conversion in order to increase the high-impedance signal via lengthy cables with the least amount of noise. The measurement of acceleration, force, pressure, or audio is done using IEPE sensors in a wide range of real-world applications and sectors, including automotive, medical, and aerospace.
The high impedance signal of the piezoelectric material is converted into a voltage signal with a low impedance, typically 100, by the electronics of the IEPE sensor (typically implemented as a FET circuit). Low impedance signals are advantageous because they can travel over long cable distances without deteriorating in signal quality.
Additionally, it is no longer necessary to use special low noise cables when using piezoelectric sensors.The majority of IEPE sensors operate at a constant current of 2 to 20 mA. The standard value is 4 mA. The maximum cable length increases with increasing constant current.
Signal quality can be used over cables that are several hundred metres long without any loss. A typical IEPE sensor supply uses 100 mW of power at 4 mA constant current and 25 V compliance voltage. This might be a problem for battery-operated systems.
The Global IEPE (integrated electronic piezoelectric) sensors market accounted for $XX Billion in 2021 and is anticipated to reach $XX Billion by 2030, registering a CAGR of XX% from 2022 to 2030.
The strategic acquisition of accelerometer expert Dytran Instruments by Spectris and integration into the HBK arm has expanded both businesses. North America is Dytran's biggest market, and the company is based there. By making this move, HBK will gain access to a significant new sales region, and Dytran will gain from HBK's widespread presence.
HBK will bring additional value from piezoelectric accelerometers, delivering higher customer intimacy and a broader product capability, thanks to its strong position in space, aerospace, and defence. In a more interconnected and sustainable world, the precision sensing industry is well positioned to expand, and the addition of Dytran will help HBK empower the innovators.
The technologies used by Dytran include digital smart sensors, MEMS accelerometers, and piezoelectric sensors, which measure force, vibration, and pressure.
The launching of the DNA-AI-211 analogue input board has been announced with pleasure by United Electronic Industries. The board delivers 24-bit resolution with a 109 dB signal to noise (S/N) ratio and 4 fully isolated IEPE/ICP accelerometer / vibration sensor channels.
The usage of IEPE sensors on any data acquisition devices with a 1 M BNC interface is now possible thanks to a novel solution from Pico Technology. Any PicoScope or oscilloscope can use the TA487 IEPE Signal Conditioner, a straightforward adaptor, to record and measure signals from a variety of piezo-electric IEPE sensors.
The new products from Advanced Sensors Calibration comprise the ASC P101A, ASC P203A, and ASC P401A series of IEPE acceleration sensors for use in the automotive, wind energy, and railway applications.
The new group of products consists of the triaxial P203A range for railway applications, the uniaxial P101A range for general vibration monitoring applications, the uniaxial P401 range for high temperature applications, and the uniaxial P401 range for high temperature applications.
To measure the IEPE sensors, the NI-9230 provides an IEPE excitation current for each channel. The case of a typical IEPE sensor is electrically isolated from the IEPE electronics. As a result, even though the sensor's case is grounded, connecting the sensor to the NI-9230 produces a floating connection.
The most popular Kistler sensor for these measurements is the IEPE (Integrated Electronics Piezoelectric) triaxial accelerometer 8763B, which enables vibration monitoring in three mutually perpendicular axes. The smallest level of vibrations that the sensor can reliably detect is determined by the measuring threshold.
The noise threshold of the 8763B has been significantly lowered across the board: it is now 51% lower for the sensor's lowest range of 100 g, 58% lower for the 250 g range, 52% lower for the 500 g range, 54% lower for the 1000 g range, and 58% lower for the 2000 g range.
These upgrades make the sensor 8763B even more appropriate for widely used tasks like modal analysis, frequency response analysis, and e-motor testing.
Sl no | Topic |
1 | Market Segmentation |
2 | Scope of the report |
3 | Abbreviations |
4 | Research Methodology |
5 | Executive Summary |
6 | Introduction |
7 | Insights from Industry stakeholders |
8 | Cost breakdown of Product by sub-components and average profit margin |
9 | Disruptive innovation in the Industry |
10 | Technology trends in the Industry |
11 | Consumer trends in the industry |
12 | Recent Production Milestones |
13 | Component Manufacturing in US, EU and China |
14 | COVID-19 impact on overall market |
15 | COVID-19 impact on Production of components |
16 | COVID-19 impact on Point of sale |
17 | Market Segmentation, Dynamics and Forecast by Geography, 2022-2030 |
18 | Market Segmentation, Dynamics and Forecast by Product Type, 2022-2030 |
19 | Market Segmentation, Dynamics and Forecast by Application, 2022-2030 |
20 | Market Segmentation, Dynamics and Forecast by End use, 2022-2030 |
21 | Product installation rate by OEM, 2022 |
22 | Incline/Decline in Average B-2-B selling price in past 5 years |
23 | Competition from substitute products |
24 | Gross margin and average profitability of suppliers |
25 | New product development in past 12 months |
26 | M&A in past 12 months |
27 | Growth strategy of leading players |
28 | Market share of vendors, 2022 |
29 | Company Profiles |
30 | Unmet needs and opportunity for new suppliers |
31 | Conclusion |
32 | Appendix |