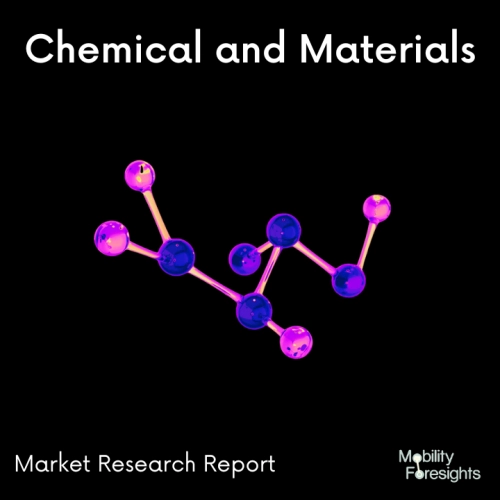
- Get in Touch with Us
Last Updated: Apr 25, 2025 | Study Period: 2024-2030
An Impingement Plate Scrubber is a type of air pollution control system that is used to reduce the amount of particulate matter from exhaust gas streams.
It works by using impingement plates, which are plates with specially-designed holes in them, to guide the flow of air from the exhaust gas stream so that it passes through a scrubbing liquid.
This scrubbing liquid is typically water-based, but can also be any other type of liquid depending on the application. The scrubbing liquid is sprayed onto the impingement plates, which then causes the particulate matter to be removed from the exhaust gas stream.
The particulate matter is then collected in a collection device and disposed of appropriately.
The Impingement Plate Scrubber is an effective and efficient method of removing particulate matter from exhaust gas streams.
It is capable of removing particles down to 0.3 microns in size, which is smaller than the particles that can be removed by other air pollution control systems. Additionally, the Impingement Plate Scrubber can handle exhaust gases that have high temperatures and pressures, which makes it suitable for a wide range of applications.
The Impingement Plate Scrubber is relatively easy to maintain and operate, making it an attractive option for many industries. It is also relatively compact, allowing for installation in limited spaces.
This makes it an ideal choice for areas with limited space and/or limited budgets. Additionally, the Impingement Plate Scrubber is able to achieve high removal efficiencies, making it an attractive option for industries that need to reduce air pollution.
Overall, the Impingement Plate Scrubber is an effective, efficient, and cost-effective method of reducing the levels of particulate matter in exhaust gas streams. It is capable of removing particles down to 0.3 microns in size and can handle exhaust gases that have high temperatures and pressures.
Additionally, the Impingement Plate Scrubber is relatively easy to maintain and operate and can be installed in limited spaces. Therefore, it is an attractive option for many industries and applications.
The Global Impingement Plate Scrubber Market accounted for $XX Billion in 2023 and is anticipated to reach $XX Billion by 2030, registering a CAGR of XX% from 2024 to 2030.
The Impingement Plate scrubber from APMG Plastics can be operated in a variety of flow rate scenarios with minimum impact on the system's dust collection and absorption efficiency.
When choosing a fume scrubber, pressure drop is a key consideration. In this regard, our Impingement Plate Fume Scrubber outperforms other gas cleaning techniques.
There will be a pressure drop of 500 to 750 Pa throughout each impingement plate stage, depending on the type of plate used. Multiplying this by the number of stages and adding to it for mist eliminator and inlet/outlet losses will yield the total pressure decrease. Depending on the circumstances, their specialists will specifically create the plate scrubber's number and kinds of stages.
The air stream can come into touch with the right chemicals on the plates to facilitate the chemical absorption of harmful contaminating gases, such as sulphur dioxide, hydrochloric acid, chlorine, hydrogen sulphide, etc.
Plate type scrubbers are thought of as constant volume units, but it is widely acknowledged that deviations from the design volume of 20% can be accepted with minimal impact on the efficiency of dust removal and gas absorption. Up to 50% of the intended capacity can often be achieved by using impingement plate scrubbers beyond these limitations.
The sieve plate, with its rounded holes, is the most basic type of impingement-plate scrubber. The gas rises through the holes in this kind of scrubber while the scouring liquid passes over the plates.
The liquid cannot pass through the holes due to the gas velocity. The froth created by the gas moving through the liquid layer is where gas-liquid-particle contact occurs. Complicated plates, such baffle or bubble cap plates, add another way to gather PM.
The gas is forced to rotate before it can escape the liquid layer by the bubble caps and baffles positioned above the plate holes. Most PM cannot be avoided by the gas turning to avoid the barriers, thus it collects on the caps or baffles.
Sl no | Topic |
1 | Market Segmentation |
2 | Scope of the report |
3 | Abbreviations |
4 | Research Methodology |
5 | Executive Summary |
6 | Introdauction |
7 | Insights from Industry stakeholders |
8 | Cost breakdown of Product by sub-components and average profit margin |
9 | Disruptive innovation in theIndustry |
10 | Technology trends in the Industry |
11 | Consumer trends in the industry |
12 | Recent Production Milestones |
13 | Component Manufacturing in US, EU and China |
14 | COVID-19 impact on overall market |
15 | COVID-19 impact on Production of components |
16 | COVID-19 impact on Point of sale |
17 | Market Segmentation, Dynamics and Forecast by Geography, 2024-2030 |
18 | Market Segmentation, Dynamics and Forecast by Product Type, 2024-2030 |
19 | Market Segmentation, Dynamics and Forecast by Application, 2024-2030 |
20 | Market Segmentation, Dynamics and Forecast by End use, 2024-2030 |
21 | Product installation rate by OEM, 2023 |
22 | Incline/Decline in Average B-2-B selling price in past 5 years |
23 | Competition from substitute products |
24 | Gross margin and average profitability of suppliers |
25 | New product development in past 12 months |
26 | M&A in past 12 months |
27 | Growth strategy of leading players |
28 | Market share of vendors, 2023 |
29 | Company Profiles |
30 | Unmet needs and opportunity for new suppliers |
31 | Conclusion |
32 | Appendix |