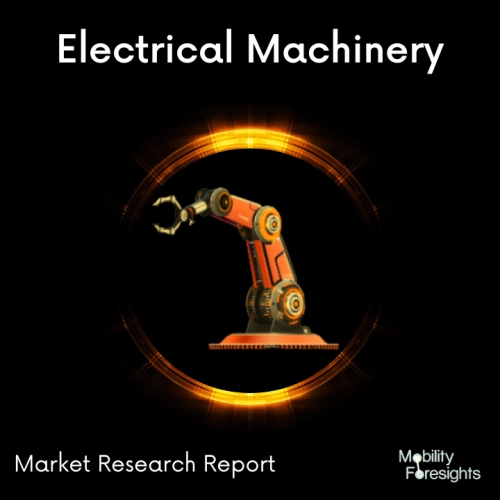
- Get in Touch with Us
Last Updated: Apr 25, 2025 | Study Period: 2023-2030
In order to determine position or motion, an incremental encoder translates the angular motion or position of a shaft into an analog or digital code. One of the most widely used types of rotary encoders is the incremental encoder.
Applications for positioning and motor speed feedback that use incremental encoders include servo/light, industrial, and heavy-duty ones. Since there aren't many sensors used, incremental encoders offer great speed and distance feedback, and the systems are easy to use and reasonably priced. Because an incremental encoder can only provide change information, it is unable to calculate motion.
A spindle assembly, PCB, and cover make up the standard assembly in an incremental optical encoder. A sensor array on the PCB produces only two primary signals one each for location and speed. In an incremental optical encoder, light passing through a designated disc is detected by an optical sensor.
The spindle assembly rotates while the disc advances, and the PCB converts the information into pulses. In an incremental magnetic encoder, a magnetic sensor takes the place of the optical sensor, and a revolving disc is filled with magnetic poles.
Resolvers and absolute encoders offer alternatives depending on the application needs and environment, even though incremental encoders are frequently used in many feedback applications.
A linear or rotary electromechanical device called an incremental encoder contains two output signals, A and B, which produce pulses whenever the device is moved. The A and B signals together signal both the presence of movement and its direction.
Numerous incremental encoders contain an additional output signal, usually called index or Z, that serves as a marker for the encoder's location relative to a specific reference position. Additionally, some encoders include a status output that describes internal fault circumstances such a bearing failure or a sensor issue.
An incremental encoder, as contrast to an absolute encoder, simply reports changes in position together with the detection of movement for each reported position change. Consequently, the encoder signals must be sent to an incremental encoder interface in order to determine absolute location at any given time.
The Global incremental encoder market accountedfor $XX Billion in 2022 and is anticipated to reach $XX Billion by 2030, registering a CAGR of XX% from 2023 to 2030.
The next generation of Programmable Incremental Rotary Encoders has been released by TR Electronic, a top supplier of encoders and sensors for the automation sector. TR Electronics latest line of programmable incremental rotary encoders builds on its technology leadership in the market.
The new product series can now tell you everything an absolute rotary encoder can, including absolute position, RPM over-speed/under-speed, and count direction, and can display and alter all of these things. It might possibly be referred to as the Intelligent Incremental Encoder.
Position, angle, and rotation counts are produced via incremental encoders. The number of lines or pulses per rotation that the encoder provides to the control unit for each rotation defines the resolution.
The control unit may calculate its current position by counting these pulses. When turning on the machine, it could be essential to perform a reference run.
As a new member of the VIONiC digital all-in-one encoder line, VIONiCplus is Renishaw's latest, highest performance optical incremental encoder system. The VIONiC architecture avoids the need for extra external interfaces by integrating all essential interpolation and signal processing inside the redhead.
To do this, Renishaw created a new Versatile Interpolation ASIC (VIA) chip to carry out all of the tasks that the interface's prior functionality handled.
The BIONiC plus incremental encoder, which achieves performance levels that are unmatched, is the result of research into the most recent fine compensation structures and improvements in contemporary optimisation techniques.
Sl no | Topic |
1 | Market Segmentation |
2 | Scope of the report |
3 | Abbreviations |
4 | Research Methodology |
5 | Executive Summary |
6 | Introduction |
7 | Insights from Industry stakeholders |
8 | Cost breakdown of Product by sub-components and average profit margin |
9 | Disruptive innovation in the Industry |
10 | Technology trends in the Industry |
11 | Consumer trends in the industry |
12 | Recent Production Milestones |
13 | Component Manufacturing in US, EU and China |
14 | COVID-19 impact on overall market |
15 | COVID-19 impact on Production of components |
16 | COVID-19 impact on Point of sale |
17 | Market Segmentation, Dynamics and Forecast by Geography, 2023-2030 |
18 | Market Segmentation, Dynamics and Forecast by Product Type, 2023-2030 |
19 | Market Segmentation, Dynamics and Forecast by Application, 2023-2030 |
20 | Market Segmentation, Dynamics and Forecast by End use, 2023-2030 |
21 | Product installation rate by OEM, 2023 |
22 | Incline/Decline in Average B-2-B selling price in past 5 years |
23 | Competition from substitute products |
24 | Gross margin and average profitability of suppliers |
25 | New product development in past 12 months |
26 | M&A in past 12 months |
27 | Growth strategy of leading players |
28 | Market share of vendors, 2023 |
29 | Company Profiles |
30 | Unmet needs and opportunity for new suppliers |
31 | Conclusion |
32 | Appendix |