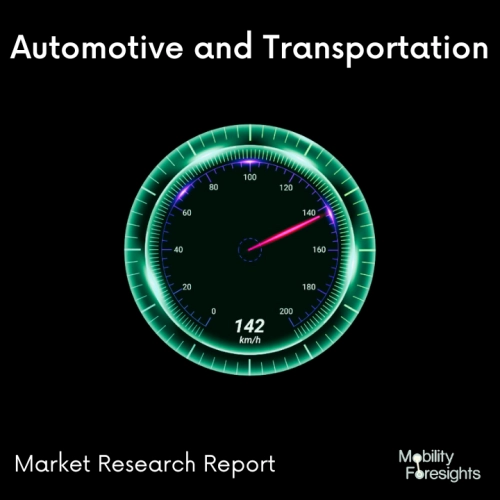
- Get in Touch with Us
Last Updated: Apr 25, 2025 | Study Period: 2024-2030
India's automotive industry is a growing giant, and the materials used to build its vehicles are undergoing a transformation. Aluminum, long overshadowed by steel, is emerging as a serious contender in the India Automotive Aluminum Market.India's tightening emission norms (BSVI) necessitate lighter vehicles for better fuel efficiency. Aluminium's lightweight properties make it an attractive option compared to traditional steel.
With rising fuel costs and stricter emission regulations (BSVI), carmakers are pressured to build lighter vehicles. Aluminum's strength-to-weight ratio makes it an ideal choice for components like hoods, fenders, and even structural parts. Environmental consciousness is gaining momentum in India. Aluminum's recyclability and lower lifecycle carbon footprint compared to steel resonate with eco-conscious consumers and manufacturers alike.
Upward Trajectory in Passenger Vehicles (PVs) as car buyers in India demand better fuel efficiency and premium features, the use of aluminum in PVs is expected to climb steadily. The booming electric two-wheeler (E2W) market and potential electrification of three-wheelers (3Ws) could see a significant rise in aluminum usage for weight reduction and improved range.
Currently, aluminum can be costlier than steel. The development of cost-effective aluminum alloys suited for the Indian market and robust recycling infrastructure for scrap metal are crucial for wider adoption. Integrating aluminum effectively into car manufacturing processes currently dominated by steel requires advancements in joining techniques like welding and riveting.The success of the "Make in India" initiative for domestic aluminum production can significantly reduce costs and make aluminum a more attractive option.
INDIA AUTOMOTIVE ALUMINIUM MARKET INTRODUCTION
Automobile design and production that uses aluminium alloys is referred to as automotive aluminium. Aluminium is a desirable material for many automotive applications because it is strong, lightweight, and corrosion-resistant. Aluminum is utilised in the automotive industry for many different things, including body panels, chassis, wheels, engine blocks, and transmission cases. Automakers can lighten the car by employing aluminium in these components, which can improve handling and fuel economy. Aluminium can also increase the crashworthiness of the car by absorbing and distributing impact energy.
Aluminium, copper, magnesium, and silicon are frequently combined to make the aluminium alloys utilised in automobile applications. The particular alloy used relies on the componentâs intended purpose and the application. For engine blocks, for instance, an alloy with a higher proportion of copper and magnesium might be utilized since it provides better strength and heat resistance. Generally, as manufacturers strive to fulfil higher fuel economy and emissions requirements while still offering a safe and dependable vehicle, aluminium utilization in the automobile industry has increased recently.
Cost-Effective Alloys: Development of new aluminum alloys with a good balance of strength and affordability is a key trend. These alloys cater to the price-sensitive Indian market and make aluminum a more viable alternative to steel. Recycling Initiatives: Companies are exploring ways to efficiently recycle aluminum scrap generated during car manufacturing in India. This reduces production costs and promotes a circular economy.
High-Strength Alloys: Indian companies are increasingly adopting high-strength aluminum alloys for structural components in vehicles. This allows for weight reduction without compromising safety, a crucial factor for passenger safety regulations. Joining Technology Advancements: There's a growing focus on developing robust and cost-effective joining techniques for aluminum, like friction stir welding and self-pierce riveting. This addresses challenges in integrating aluminum into existing steel-dominated manufacturing processes.
Tier-2 and Tier-3 Suppliers: The use of aluminum is gradually extending beyond major car manufacturers to Tier-2 and Tier-3 component suppliers. This widens the reach of aluminum in the Indian automotive industry. Focus on Two-Wheeler and Three-Wheeler Segments: As the E2W market thrives and electrification of 3Ws becomes a possibility, there's an emerging trend of using aluminum for lightweight frames and battery enclosures in these segments.
Life Cycle Assessment (LCA): Car manufacturers are increasingly conducting Life Cycle Assessments to understand the environmental impact of materials used. Aluminum's recyclability and lower carbon footprint compared to steel are becoming a selling point. Green Manufacturing Practices: Emphasis on sustainable manufacturing practices is pushing companies to explore greener alternatives like using recycled aluminum content in car parts.
India automotive aluminium market accounted for $XX Billion in 2023 and is anticipated to reach $XX Billion by 2030, registering a CAGR of XX% from 2024 to 2030.
In order to create a prototype of the electric Tata Tiago car, which makes use of Phinergyâs unique aluminum-air battery, the company collaborated with Tata Motors. The prototype was displayed during the January Auto Expo India event in New Delhi.The companyâs aluminum-air battery produces electricity using the energy produced when aluminium and oxygen react. By breathing oxygen, the aluminium anode, which serves as the fuel, converts water into hydroxide. Somewhat slowly, the outer layer dissolves back into alumina hydroxide.
The aluminium air battery must be completely replaced once the aluminium is used up. According to reports, this zero-emission technology offers a high energy density solution that can assist automakers in reducing the size of the battery in their cars. Additionally, the two businesses have MOUs with a number of the top automakers in the Indian market. With a Mahindra Electric three-wheeler, the business has most recently accomplished a 500 km continuous drive driven by aluminium energy.
Sl no | Topic |
1 | Market Segmentation |
2 | Scope of the report |
3 | Research Methodology |
4 | Executive Summary |
5 | Average B2B Price, By Region |
6 | 5 key Prediction for Hotel Industry in India Automotive Aluminium Market |
7 | Key Drivers and Challenges Shaping the India Automotive Aluminium Market |
8 | Impact of Emerging Brands and Disruptors |
9 | Growth potential and key markets for India Automotive Aluminium Market in different regions. |
10 | Analysis of the supply chain and manufacturing processes in the industry |
11 | Investment opportunities in India Automotive Aluminium Market |
12 | Technological advancements influencing product development |
13 | Consumer insights and preferences in India Automotive Aluminium Market |
14 | Factors propelling the growth of India Automotive Aluminium Market |
15 | Analysis of emerging market trends and innovations in India Automotive Aluminium Market |
16 | Consumer behavior shifts in response to cultural and societal changes |
17 | Investment opportunities in the India Automotive Aluminium Market |
18 | Market Size, Dynamics and Forecast by By End-User , 2024-2030 |
19 | Market Size, Dynamics and Forecast by, Aluminium alloy type 2024-2030 |
20 | Market Size, Dynamics and Forecast by Application, 2024-2030 |
21 | Market Size, Dynamics and Forecast by Vehicle segment, 2024-2030 |
22 | Competitive Landscape |
23 | M&A in past 12 months |
24 | Growth strategy of leading players |
25 | Market share of vendors, 2023 |
26 | Company Profiles |
27 | Unmet needs and opportunity for new suppliers |
28 | Conclusion |