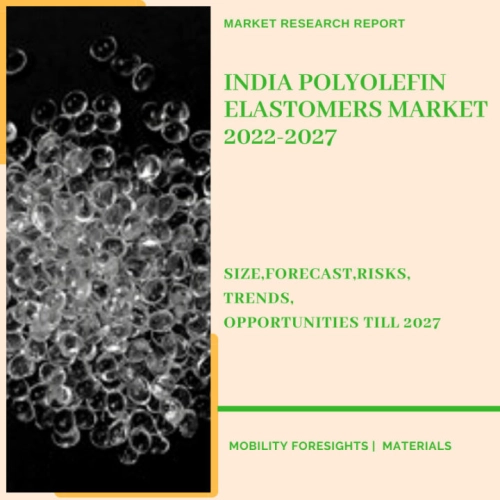
- Get in Touch with Us
Last Updated: Apr 25, 2025 | Study Period: 2022-2027
Polyolefin elastomers are straightforward polymer compounds that were first introduced to the market with the automotive sector in mind. Elastomers, fillers, and other compounds are mixed together, then specific TPO components made for specific uses are added.
TPOs' complex value and supply chain before they reach the ultimate consumer raises the entire price of the product and reduces end consumers' trust. It's utilised in everything from car weather-stripping to gaskets, hoses, seals, and electrical insulation.
Automobile manufacturers prefer thermoplastic polyolefin elastomers for a variety of internal and external uses. Demand has been spurred by substantial integration of TPOs and beneficial network externalities by automakers all over the world.
On the strength of increased demand for healthcare equipment around the world, syringe tips and peristatic tubes have achieved adequate traction in the industry. Over the last decade, manufacturers have realised the benefits of low costs and easy access, and increased market reach has bolstered the country's agglomeration economies.
The rise in electric vehicle production has a knock-on effect on the market for lightweight materials including TPOs, POEs, and TPVs, among others. POE is used in bumpers, instrument panels, and other areas.
Medical device manufacturers are increasingly using polyolefin elastomers to make catheters, tubes, masks, and bags. Polyolefin elastomers' properties, such as high sterilisation resistance, ease of mixing with other polymers, high torque transmission, superior impact resistance, and resistance to harsh chemicals, are likely to drive demand.
Aside from the complicated elements of supply sequence, the existence of a multitude of substitute products with similar properties, such as exacerbated TPOs, POEs, and polycarbonate vulcanizates (TPVs), among other potential materials, could be used by automakers and industrial equipment end users at a lower price tag at the compounding pharmacist and end-user nodes of the distribution chain.
As a result, several risk factors in the TPO elastomers industry will function as roadblocks to the market's significant expansion in the future years.
Exxon Mobil is a leading mobiliser of the polymers in the market. The latest integration has been the Polyethylene alpha olefin composites called exact elastomers straddle the gap amongst rubber compounds and polymers.
They're used as polymer enhancers in packaging applications, moulded and extruded goods, cable insulation, and foamy compounds because of their rubber-like characteristics and plastic ease of processing.
Exact elastomers balance high flow, flexibility, and shock resistance. They contribute to the auto industry's increased desire for smaller, lighter-weight parts that preserve strength and endurance.
MitsuiChemicals is part of the component manufacture trending companies in the current industry. TheLow-crystallinity copolymers soften, enhance impact resistance, and lower the melting point of polyethylene (PE) and polypropylene (PP). Polyethylene, polypropylene, EPDM, and polyamide compounds can be tailored to have certain qualities.
TAFMER is preferred by compounders who need to manufacture the cheapest solution for their customers because to its low density. TAFMER is utilised in a variety of applications including automotive thermoplastic polyolefin (TPO) compounds, wire and cable materials, and packaging.
Sl no | Topic |
1 | Market Segmentation |
2 | Scope of the report |
3 | Abbreviations |
4 | Research Methodology |
5 | Executive Summary |
6 | Introduction |
7 | Insights from Industry stakeholders |
8 | Cost breakdown of Product by sub-components and average profit margin |
9 | Disruptive innovation in theIndustry |
10 | Technology trends in the Industry |
11 | Consumer trends in the industry |
12 | Recent Production Milestones |
13 | Component Manufacturing in US, EU and China |
14 | COVID-19 impact on overall market |
15 | COVID-19 impact on Production of components |
16 | COVID-19 impact on Point of sale |
17 | Market Segmentation, Dynamics and Forecast by Geography, 2022-2027 |
18 | Market Segmentation, Dynamics and Forecast by Product Type, 2022-2027 |
19 | Market Segmentation, Dynamics and Forecast by Application, 2022-2027 |
20 | Market Segmentation, Dynamics and Forecast by End use, 2022-2027 |
21 | Product installation rate by OEM, 2022 |
22 | Incline/Decline in Average B-2-B selling price in past 5 years |
23 | Competition from substitute products |
24 | Gross margin and average profitability of suppliers |
25 | New product development in past 12 months |
26 | M&A in past 12 months |
27 | Growth strategy of leading players |
28 | Market share of vendors, 2022 |
29 | Company Profiles |
30 | Unmet needs and opportunity for new suppliers |
31 | Conclusion |
32 | Appendix |