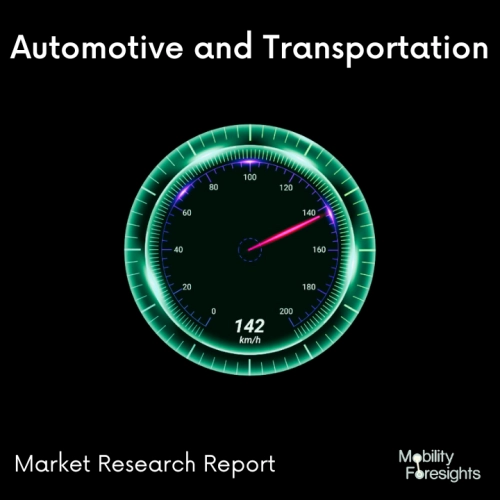
- Get in Touch with Us
Last Updated: Apr 25, 2025 | Study Period: 2023-2030
In order to reduce weight and improve vehicle packaging, there is an increasing demand for lightweight wiring harnesses.
Some automakers are considering aluminum for weight and cost reduction. Aluminum has its own challenges such as corrosion and termination issues. Hence, prominent wiring harness manufacturers use copper because of its high thermal capacity and conductivity.
The Indonesia Automotive Wiring Harness Market accounted for $XX Billion in 2023 and is anticipated to reach $XX Billion by 2030, registering a CAGR of XX% from 2023 to 2030
As Increasing adoption of EVâs and HEVâs require high-voltage electrical systems, manufacturers are developing high-voltage wiring harnesses to meet this need.
These harnesses are designed to handle the high voltage and current demands of EVs, while also providing protection against electrical interference and short circuits.
The automotive harness weight per vehicle is gradually increasing due to additional electronic controls and features
Since most of automatic features in the region is limited to luxury and high end SUVs, there is room for these features to be equipped in the mass segment
With the fitment of these features in mass segment the market volume for wiring harness will propel drastically
Aluminium wires could potentially reduce the weight by 10-20% if it is replaced for copper. Currently, only ~4% of the overall wiring is of aluminium material.
Pick up truck sales in the country reached its peak in 2022 with the sales of ~149K units. This will propel the volume for wiring harness in the country in commercial vehicle segment
The rise in Nickel prices had affected the availability of terminals, relays and other components
Valens Semiconductor and Sumitomo Electric Industries announced that they are collaborating in the field of A-PHY technology and deployments.
The companies will work together to ensure that Sumitomo Electric's wiring harness systems meet the channel requirements of the A-PHY specification, while Valens will add the Sumitomo Electric cable assembly and matching on-board connectors as an ordering option for its VA70X customer evaluation kits.
Wiring Harness manufacturers are exploring for additive element along with Iron to make an aluminium alloy which will be able to conduct at low diameters.
DRAXLMAIER developed high voltage control box which is designed for connecting the cell package to the high-voltage wiring harnesses.
It contains precise measurement and control electronics, which meet the requirements set out by ASIL risk level C, including an integrated thermal management function
Sumitomo Electric developed wiring harness which provides electric power and signals to electrical components within sliding doors, whether the door is open, closed, or in operation. This allows opening and closing of the door to be automated.
It is used for the slide door of minivans, conveying electricity (power supply, signal) to electrical components installed in the door either in closed or opened state.
Furukawa Electric developed corrosion-proof terminal that seal the connection part with a tube structure to prevent corrosion.
Individual corrosion-proofing processing is not required because a sealed structure is formed by crimping the tube shaped terminal to a wire.
This results reductions in manufacturing costs and is contributing to the expansion of adoption of aluminum wires.
COMPETITIVE LANDSCAPE
The connectors developed by Sumitomo Electric reduces the overall weight of connectors by 20-40%
Almost every connector manufacturer have opted for push to seat connector over pull to seat ones
Sumitomo Electric accounted for XX% of the market in Indonesia Automotive Wiring Harness
Although globally Yazaki is one of the biggest wiring harness manufacturer, their share in the Indonesian market is much lesser
As Yazaki moves more of its production overseas, it plans to make fewer wire harnesses in Japan, creating a challenge to protect employment for those employees who sustained production up to now.
Sl no | Topic |
1 | Market Segmentation |
2 | Scope of the report |
3 | Abbreviations |
4 | Research Methodology |
5 | Executive Summary |
6 | Introduction |
7 | Insights from Industry stakeholders |
8 | Cost breakdown of Product by sub-components and average profit margin |
9 | Disruptive innovation in the Industry |
10 | Technology trends in the Industry |
11 | Consumer trends in the industry |
12 | Recent Production Milestones |
13 | Component Manufacturing in US, EU and China |
14 | COVID-19 impact on overall market |
15 | COVID-19 impact on Production of components |
16 | COVID-19 impact on Point of sale |
17 | Market Segmentation, Dynamics and Forecast by Geography, 2023-2030 |
18 | Market Segmentation, Dynamics and Forecast by Product Type, 2023-2030 |
19 | Market Segmentation, Dynamics and Forecast by Application, 2023-2030 |
20 | Market Segmentation, Dynamics and Forecast by End use, 2023-2030 |
21 | Product installation rate by OEM, 2023 |
22 | Incline/Decline in Average B-2-B selling price in past 5 years |
23 | Competition from substitute products |
24 | Gross margin and average profitability of suppliers |
25 | New product development in past 12 months |
26 | M&A in past 12 months |
27 | Growth strategy of leading players |
28 | Market share of vendors, 2023 |
29 | Company Profiles |
30 | Unmet needs and opportunity for new suppliers |
31 | Conclusion |
32 | Appendix |