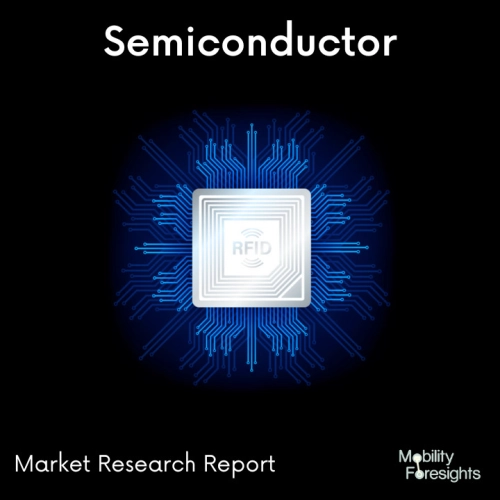
- Get in Touch with Us
Last Updated: Apr 25, 2025 | Study Period: 2024-2030
An alternating current (AC) electrical generator known as an induction generator, also known as an asynchronous generator, generates electricity using the same principles as induction motors. Mechanically rotating their rotors faster than synchronous speed is how induction generators work.
Typically, a standard AC induction motor can function as a generator without requiring any internal alterations. Induction generators are helpful in applications like micro hydro power plants, wind turbines, or decreasing high-pressure gas streams to lower pressure because they can recover energy with comparatively simple controls.
Reactive excitation current is drawn from an external source using an induction generator. Unlike synchronous machines, which can bootstrap utilising residual magnetism to black start a de-energized distribution system, induction generators have an AC rotor.
Externally installed power factor-correcting capacitors can be used to offset a fixed amount of the variable reactive excitation current.
A capacitor bank can be used by an induction generator to generate reactive excitation current after it has started, however the isolated power system's voltage and frequency are not self-regulating and are easily unstable.
The Global Induction generator market accounted for $XX Billion in 2023 and is anticipated to reach $XX Billion by 2030, registering a CAGR of XX% from 2024 to 2030.
Effectively Utilising Wind Energy with a Sun Integrated Doubly Fed Induction Generator. The Doubly-Fed Induction Generator (DFIG) is a standard, dual-input asynchronous device connected across both the stator and the rotor that also serves as an electrical transducer and can use up to 30% of the power produced during rotor injection. This is the main issue with the DFIG's ability to generate power effectively.
By linking the DFIG with a collection of solar Photovoltaic (PV) panels via a typical direct current bus and a boost converter, the proposed method addresses this unwelcome power loss.
In order to maintain the constant DC voltage under arbitrary circumstances, this study setup can function on the basis of indirect vector control algorithms performed at the rotor and grid converter level.
With this cutting-edge strategy, even voltage and frequency changes will be under control. Using the MATLAB/Simulink environment, a simulation model of a 2MW DFIG system and a 300KW solar PV array is created.
In order to reduce the power rating of the converters and power consumption from the grid, solar and wind energy sources incorporate Maximum Power Point Tracking (MPPT) through their control algorithms, resulting in the addition of 30-80 KW of solar power for rotor injection compared to the existing system.
Sl no | Topic |
1 | Market Segmentation |
2 | Scope of the report |
3 | Abbreviations |
4 | Research Methodology |
5 | Executive Summary |
6 | Introduction |
7 | Insights from Industry stakeholders |
8 | Cost breakdown of Product by sub-components and average profit margin |
9 | Disruptive innovation in the Industry |
10 | Technology trends in the Industry |
11 | Consumer trends in the industry |
12 | Recent Production Milestones |
13 | Component Manufacturing in US, EU and China |
14 | COVID-19 impact on overall market |
15 | COVID-19 impact on Production of components |
16 | COVID-19 impact on Point of sale |
17 | Market Segmentation, Dynamics and Forecast by Geography, 2024-2030 |
18 | Market Segmentation, Dynamics and Forecast by Product Type, 2024-2030 |
19 | Market Segmentation, Dynamics and Forecast by Application, 2024-2030 |
20 | Market Segmentation, Dynamics and Forecast by End use, 2024-2030 |
21 | Product installation rate by OEM, 2023 |
22 | Incline/Decline in Average B-2-B selling price in past 5 years |
23 | Competition from substitute products |
24 | Gross margin and average profitability of suppliers |
25 | New product development in past 12 months |
26 | M&A in past 12 months |
27 | Growth strategy of leading players |
28 | Market share of vendors, 2023 |
29 | Company Profiles |
30 | Unmet needs and opportunity for new suppliers |
31 | Conclusion |
32 | Appendix |