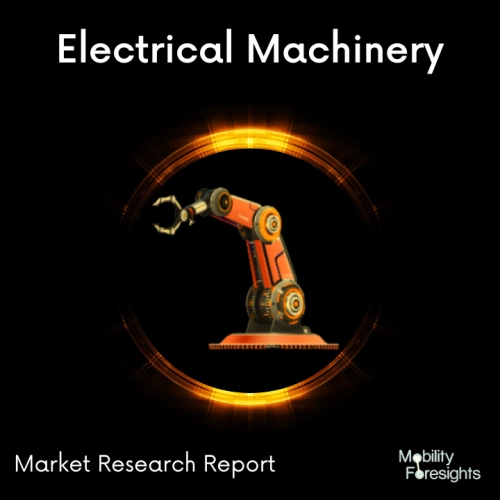
- Get in Touch with Us
Last Updated: Apr 25, 2025 | Study Period: 2024-2030
A physical object can be made using industrial 3D printers by starting with a computer-aided design (CAD) digital file. Up until the object is finished, thin layers of material are deposited gradually. The method is the reverse of subtractive manufacturing, which involves cutting a product out of raw materials.
In comparison to conventional processes, 3D printers generates less waste, needs no tools or molds, permits customization of each output, and speeds the time it takes for complex designs to reach the market.
Plastic, metals, and alloys, which are the most common materials for industrial and consumer printers, are used to quickly produce prototypes and finished parts.
The Global Industrial 3D printer market accounted for $XX Billion in 2022 and is anticipated to reach $XX Billion by 2030, registering a CAGR of XX% from 2024 to 2030.
The release of the NXE 200 industrial 3D printer, a low-cost entry point into Lubricant Sublayer Photo-curing (LSPc) technology, has been revealed by Nexa3D, a manufacturer of ultrafast 3D printers. In order to broaden the accessibility of LSPc technology, Nexa3D has added the NXE 200 to its inventory, which also includes the NXE 400 industrial 3D printer and the NXD 200 dental 3D printer.
For designers, engineers, and manufacturers who need efficient, precise, and scalable manufacturing and prototyping options, the NXE 200 is the best choice.
The system has a large build volume of 8.5L and a build area of 275 x 155 x 200mm in addition to printing objects at a speed that is 6.5 times faster than rival resin 3D printing technologies.
With this combination of speed and volume, users can create big parts and production runs of smaller parts in a fraction of the time needed by other 3D printers.
For the NXE 200 industrial 3D printer, Nexa3D offers a variety of materials in addition to its simple-to-use NexaX 2.0 software, which allows intelligent build optimization, process stability, and print consistency. The xWash and xCure post-processing technologies finish the validated workflow.
Each of these components is fast and easy to use, which cuts down on the time needed for print setup and post-processing.
Sl no | Topic |
1 | Market Segmentation |
2 | Scope of the report |
3 | Abbreviations |
4 | Research Methodology |
5 | Executive Summary |
6 | Introduction |
7 | Insights from Industry stakeholders |
8 | Cost breakdown of Product by sub-components and average profit margin |
9 | Disruptive innovation in the Industry |
10 | Technology trends in the Industry |
11 | Consumer trends in the industry |
12 | Recent Production Milestones |
13 | Component Manufacturing in US, EU and China |
14 | COVID-19 impact on overall market |
15 | COVID-19 impact on Production of components |
16 | COVID-19 impact on Point of sale |
17 | Market Segmentation, Dynamics and Forecast by Geography, 2024-2030 |
18 | Market Segmentation, Dynamics and Forecast by Product Type, 2024-2030 |
19 | Market Segmentation, Dynamics and Forecast by Application, 2024-2030 |
20 | Market Segmentation, Dynamics and Forecast by End use, 2024-2030 |
21 | Product installation rate by OEM, 2023 |
22 | Incline/Decline in Average B-2-B selling price in past 5 years |
23 | Competition from substitute products |
24 | Gross margin and average profitability of suppliers |
25 | New product development in past 12 months |
26 | M&A in past 12 months |
27 | Growth strategy of leading players |
28 | Market share of vendors, 2023 |
29 | Company Profiles |
30 | Unmet needs and opportunity for new suppliers |
31 | Conclusion |
32 | Appendix |