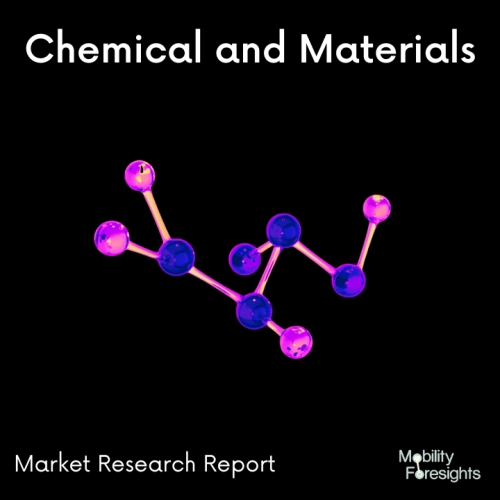
- Get in Touch with Us
Last Updated: Apr 25, 2025 | Study Period: 2024-2030
The process of designing, implementing, and maintaining automated systems in an industrial plant is known as industrial automation engineering. Reduce operating expenses: Healthcare costs, paid leave, and holidays associated with a human operator are eliminated by industrial automation.
Additionally, industrial automation does not necessitate the provision of additional employee benefits like pension coverage or bonuses. Most importantly, despite the high initial cost, it saves the workers' monthly wages, resulting in significant cost savings for the business.
Maintenance automation reduces the risk of human error. Additionally, robots do not experience fatigue, which results in products of uniform quality produced at various times.
Because industrial automation machinery rarely fails, its maintenance costs are lower. It can only be fixed by computer and maintenance engineers if it breaks. It involves designing the architectures of machines and procedures and controlling them with software.
Programmable logic controllers (PLCs), human-machine interfaces (HMIs), distributed control systems (DCSs), programmable logic controllers (PLCs), and other industrial automation software and products are just a few examples.
The goal of industrial automation is to automate production through the use of control systems like machines, actuators, sensors, processors, and networks.
Simple conveyor belts that moved parts through an assembly line were the beginning of industrial automation. Automated systems can be broken down into four categories: programmable automation, flexible automation, integrated automation, and fixed automation.
The Global Industrial automation engineering polymers market accounted for $XX Billion in 2023 and is anticipated to reach $XX Billion by 2030, registering a CAGR of XX% from 2024 to 2030.
Industrial automation engineering polymers manufacturer Form labs unveiled a high-productivity additive manufacturing platform. Its "Automation Ecosystem," which consists of three new products, including Fleet Control software and Form labs' Form Auto and High Volume Resin hardware packages, is said to assist users in driving greater 3D printing utilization.
The company hopes that by doing so, it will be able to assist dental labs, service bureaus, and job shops in increasing production without significantly increasing their labor requirements.
The Form labs Automation Ecosystem is a seamless solution for ramping up production with 3D printer fleets, staying true to the ease of use of all Form labs products. With more than 100 million parts printed on our 3D printers, Form labs users recently reached a significant milestone.
By adding this ecosystem, Form labs is increasing the capacity so that users can deliver additional 3D printing innovation. Form labs initially concentrated on stereolithography (SLA) 3D printing, but it has gradually broadened its product offering to meet the demands of new markets and customers.
The high-speed Form 3+ and Form 3B+ 3D printers, which were introduced at the CES convention last year, are among the most recent additions to the company's SLA offering.
Its "Automation Ecosystem," which consists of three new products, including Fleet Control software and Form labs' Form Auto and High Volume Resin hardware packages, is said to assist users in driving greater 3D printing utilization.
The company hopes that by doing so, it will be able to assist dental labs, service bureaus, and job shops in increasing production without significantly increasing their labor requirements.
Form labs initially concentrated on stereolithography (SLA) 3D printing, but it has gradually broadened its product offering to meet the demands of new markets and customers. The high-speed Form 3+ and Form 3B+ 3D printers, which were introduced at the CES convention last year, are among the most recent additions to the company's SLA offering.
Sl no | Topic |
1 | Market Segmentation |
2 | Scope of the report |
3 | Abbreviations |
4 | Research Methodology |
5 | Executive Summary |
6 | Introduction |
7 | Insights from Industry stakeholders |
8 | Cost breakdown of Product by sub-components and average profit margin |
9 | Disruptive innovation in the Industry |
10 | Technology trends in the Industry |
11 | Consumer trends in the industry |
12 | Recent Production Milestones |
13 | Component Manufacturing in US, EU and China |
14 | COVID-19 impact on overall market |
15 | COVID-19 impact on Production of components |
16 | COVID-19 impact on Point of sale |
17 | Market Segmentation, Dynamics and Forecast by Geography, 2024-2030 |
18 | Market Segmentation, Dynamics and Forecast by Product Type, 2024-2030 |
19 | Market Segmentation, Dynamics and Forecast by Application, 2024-2030 |
20 | Market Segmentation, Dynamics and Forecast by End use, 2024-2030 |
21 | Product installation rate by OEM, 2023 |
22 | Incline/Decline in Average B-2-B selling price in past 5 years |
23 | Competition from substitute products |
24 | Gross margin and average profitability of suppliers |
25 | New product development in past 12 months |
26 | M&A in past 12 months |
27 | Growth strategy of leading players |
28 | Market share of vendors, 2023 |
29 | Company Profiles |
30 | Unmet needs and opportunity for new suppliers |
31 | Conclusion |
32 | Appendix |