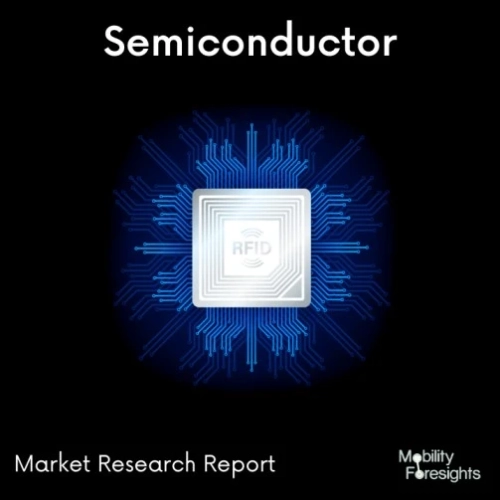
- Get in Touch with Us
Last Updated: Apr 25, 2025 | Study Period:
The Global Industrial Encoder Market is expected to experience significant growth from 2024 to 2030, driven by rising automation and the increasing demand for precision in industrial processes. This growth is estimated to be at a Compound Annual Growth Rate (CAGR) of around 10%. Two main types of industrial encoders exist: rotary encoders, which measure rotational motion, and linear encoders, which measure linear displacement. Both play a crucial role in various industrial applications, including robotics, machine tools, and factory automation.
The increasing adoption of Industry 4.0 principles, which emphasize automation and data exchange in manufacturing, is a major factor propelling the industrial encoder market. These encoders provide the precise positioning and speed feedback necessary for automated systems to function efficiently. Another key driver is the growth of emerging economies like China and India, where investments in industrial infrastructure and manufacturing are rapidly increasing. This demand for industrial automation creates a ripple effect, leading to a greater need for encoders.
However, the market also faces challenges. The high initial investment cost of high-end encoders can be a deterrent for some manufacturers. Additionally, installation, maintenance, and calibration of encoders require specific expertise, which can be a barrier for smaller companies. Despite these challenges, advancements in technology are creating exciting opportunities. The integration of encoders with the Internet of Things (IoT) allows for real-time monitoring and remote diagnostics, improving overall system efficiency.
Furthermore, the development of new encoder technologies, such as magnetic and multi-turn encoders, is offering greater accuracy, durability, and versatility in harsh industrial environments. Looking ahead, the growing demand for renewable energy systems, autonomous vehicles, and smart factories is expected to further propel the industrial encoder market. These sectors rely heavily on precise motion control, making encoders an essential component.
In conclusion, the global industrial encoder market is poised for robust growth in the coming years, driven by automation trends, technological advancements, and the rise of new industries. As the demand for precision and efficiency in industrial processes continues to climb, encoders will play a critical role in enabling smarter and more automated manufacturing operations.
Industrial encoders are devices used in various industries to convert mechanical motion into electrical signals, providing precise feedback on position, speed, and direction of movement. They are essential components in motion control systems, enabling automation and accuracy in industrial processes. There are two main types of industrial encoders: incremental and absolute. Incremental encoders generate pulses as the shaft rotates, providing relative position information, while absolute encoders provide absolute position information, usually in the form of binary or gray code, ensuring accurate positioning even after power loss.
The benefits of industrial encoders include improved accuracy, efficiency, and reliability in industrial operations. They enable precise control of machinery, enhancing productivity and quality of output. Industrial encoders also facilitate automation, reducing the need for manual intervention and minimizing human error. Moreover, they contribute to predictive maintenance strategies by providing real-time feedback on equipment performance, helping to prevent costly downtime and prolonging the lifespan of machinery.
However, industrial encoders also pose certain risks and challenges. They can be susceptible to environmental factors such as dust, moisture, and temperature variations, which may affect their performance and accuracy. Moreover, compatibility issues and integration complexities can arise when implementing encoder systems into existing machinery or control systems.
Additionally, the reliance on electrical signals makes industrial encoders vulnerable to electromagnetic interference (EMI) and electrical noise, which can disrupt signal transmission and accuracy. Despite these challenges, advancements in technology and ongoing innovations aim to address these issues, ensuring the continued relevance and effectiveness of industrial encoders in diverse industrial applications.
The Global Industrial Encoder Market accounted for $XX Billion in 2023 and is anticipated to reach $XX Billion by 2030, registering a CAGR of XX% from 2024 to 2030.
Rockwell Automation Inc. introduced the"PrecisionPlus" encoder series, which sets new standards in accuracy and reliability. These encoders boast an impressive resolution of up to 10,000 pulses per revolution, enabling precise control in demanding industrial applications. With advanced signal processing algorithms, the PrecisionPlus series ensures smooth operation even in harsh environments, providing dependable feedback for motion control systems.
Omron Corporationintroduced the"OmniSense" encoder series. This groundbreaking series offers unparalleled accuracy and durability, making it ideal for high-speed and high-precision industrial applications. With a resolution exceeding 20,000 pulses per revolution, OmniSense encoders deliver precise positioning and motion control, ensuring optimal performance in diverse manufacturing environments.
Renishaw plcintroduced the "UltraTrack" series, a cutting-edge lineup of industrial encoders designed to revolutionize precision measurement in the Global Industrial Encoder Market from 2024 to 2030. The UltraTrack series combines Renishaw's expertise in metrology with advanced encoder technology, offering unmatched accuracy and reliability. With resolutions up to 100,000 pulses per revolution, UltraTrack encoders provide precise feedback for high-precision motion control and positioning applications across various industries.
Sl no | Topic |
1 | Market Segmentation |
2 | Scope of the Report |
3 | Research Methodology |
4 | Executive Summary |
5 | Introduction |
6 | Average B-2-B Selling Price in Past 5 Years |
7 | Insights from Industry Stakeholders |
8 | Cost Breakdown of Product Components and Average Profit Margin |
9 | Disruptive Innovation in the Industry |
10 | Technological Innovations in Global Industrial Encoder Market 2024-2030 |
11 | Integration of IoT and AI in Industrial Encoders |
12 | Advances in Wireless Communication Technologies |
13 | Miniaturization Trends in Industrial Encoder Design |
14 | Eco-Friendly and Energy-Efficient Encoder Solutions |
15 | Cybersecurity Measures in Industrial Encoder Systems |
16 | Data Analytics and Predictive Maintenance Capabilities |
17 | Evolution of Materials Science in Encoder Manufacturing |
18 | Smart Manufacturing and Industry 4.0 Integration |
19 | Enhanced Accuracy and Resolution in Encoder Technology |
20 | Real-Time Monitoring and Remote Access Features |
21 | New Product Development in the Past 12 Months |
22 | Market Size, Dynamics, and Forecast by Geography (2024-2030) |
23 | Market Size, Dynamics, and Forecast by Type (2024-2030) |
24 | Market Size, Dynamics, and Forecast by Industry (2024-2030) |
25 | Market Size, Dynamics, and Forecast by Technology (2024-2030) |
26 | Competitive Landscape and Market Share Analysis |
27 | Growth Strategy of Leading Players |
28 | Market Share of Vendors (2023) |
29 | Company Profiles |
30 | Unmet Needs and Opportunities for New Suppliers |
31 | Conclusion |