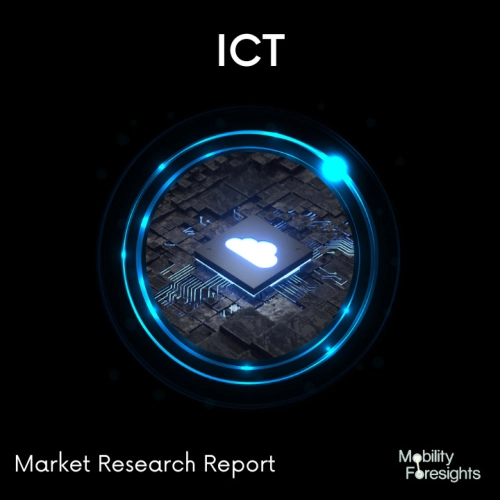
- Get in Touch with Us
Last Updated: Apr 25, 2025 | Study Period: 2024-2030
Industrial laser systems are employed for a variety of tasks, including cutting metals and fabrics, marking tracking codes for industrial traceability, precisely welding metals, cleaning metal surfaces, modifying surface roughness, and measuring part dimensions.
They are extensively utilized in a variety of sectors, including the EV and primary metals industries.
The same principles underlie all lasers, which come in a variety of power levels, colors, and beam widths. What is an industrial laser and how does it operate? Laser light is monochromatic, which means that its color is limited to a single distinct hue.
The wavelength of the electromagnetic waves that make up light determines its color. It is possible for the beam to be visible, infrared, or ultraviolet.
A typical incandescent lamp, for instance, emits a mixture of green, yellow, red, blue, and even infrared light, despite appearing to be yellowish. Its wavelength lies in the 400â800 nanometer region.
The wavelength of a typical industrial red laser, such as a helium-neon laser, spans from 632.800 to 632.802 nanometers.
A helium-neon laser is monochromatic, whereas regular incandescent light is polychromatic. Laser light is distinct due to its monochromaticity, which also enables some of its specialized applications.
The direction of the laser beam is only one. Its beam diameter is tiny and nearly constant over a wide range of distances, and its orientation is fixed.
The lasers' extremely high power output is made possible by this light concentration. Metal can be sliced with high-energy pulsed lasers with power in the megawatt range.
The word "coherent" refers to the synchronization of all the light rays within the beam. They share the same polarity and phase. The beam's tremendous strengths are also made possible by this coherence.
The Global Industrial laser system market accounted for $XX Billion in 2022 and is anticipated to reach $XX Billion by 2030, registering a CAGR of XX% from 2024 to 2030.
Fiber technology has been developed by Furukawa Electric. The business is currently improving itself based on its traditional technology by utilizing cutting-edge technology in the areas of energy, information, heat conduction, convection, and storage.
Furukawa makes contributions to the construction, automotive, and electronics sectors. The world industry benefited from its contribution.
Furukawa created and introduced the industrial laser system. Numerous positive characteristics of the Furukawa fiber laser include high beam quality, time stability, high dependability, and high effect.
For cutting half- and shingled-cells in the manufacture of photovoltaics, 3D-Micromac introduces a new laser system. With the microCELL MCS cell cutting system, you have a wide range of cutting arrangement options, from half-cells to shingled cells, without sacrificing throughput or yield.
The microCELL MCS is a sophisticated laser cutting system for half- and shingled solar cells, developed by 3D-Micromac AG, the global leader in roll-to-roll laser systems and laser micromachining for the semiconductor, photovoltaic (PV), medical device, and electronics markets.
By reducing power losses and offering extraordinarily high mechanical strength of cut cells, the new microCELL MCS advanced laser technology has been created to answer the PV market's demands for increasing module power output and service life.
It permits cutting cell sizes up to M12/G12 into half-cells or shingled cells at the highest throughputs. Two microCELL MCS systems have been purchased by Heckert Solar GmbH for its facilities in Thuringia (LWD Solar GmbH) and Chemnitz.
Heckert Solar GmbH is one of the biggest and most renowned German producers of high-performance PV modules.Recent improvements in PV production are driven by cell cutting. Due to the significant increases in power output and mechanical strength at the module level made possible by cutting solar cells into half-cells, this technique has recently become an important strategy for PV production.
This pattern has been accompanied by a shift to bigger full-cell forms and a corresponding rise in module power ratings.
Cell cutting will continue to be a key component of PV manufacturing for the foreseeable future because it compensates for the greater power loss caused by the higher cell currents from larger wafer surfaces.
Cell cutting can be used to divide cells into half- and third-cells or even shingles.The thermal laser separation (TLS) method for cell separation, which is a trademark of 3D-Micromac, is utilized by the microCELL MCS system.
A superb edge quality is ensured by the ablation-free method. As a result, compared to ablative laser procedures, the separated cells have a mechanical strength that is up to 30% higher, which allows for less power degradation over the course of the solar module's life.
It has been demonstrated that TLS can produce a module power gain of at least 2W by drastically lowering edge recombination losses and preparing the way for cutting edge passivation. Compared to solar cells that have undergone traditional processing, one-pass contactless dicing offers much improved mechanical stability.
Unrivaled versatility in terms of the number of cell cuts; in the default setup, the laser system only splits cells in half. The device can cut up to sixth-cut cells without reducing throughput, depending on how many laser sources are used.
More than 6,000 wafers produced per hour with superior productivity Outstanding upgradeability - simple integration of extra laser modules to enhance the number of cell cuts
In the upcoming years, the industry growth will be significantly impacted by the use of half- and shingled cells in PV modules.
They offer future-proof production options to module makers with their new microCELL MCS laser technology, which seamlessly integrates into an intelligent and scalable cell production line. To increase the number of cuts per wafer without reducing throughput, the system can be extended with more lasers with no difficulty.
Sl no | Topic |
1 | Market Segmentation |
2 | Scope of the report |
3 | Abbreviations |
4 | Research Methodology |
5 | Executive Summary |
6 | Introduction |
7 | Insights from Industry stakeholders |
8 | Cost breakdown of Product by sub-components and average profit margin |
9 | Disruptive innovation in the Industry |
10 | Technology trends in the Industry |
11 | Consumer trends in the industry |
12 | Recent Production Milestones |
13 | Component Manufacturing in US, EU and China |
14 | COVID-19 impact on overall market |
15 | COVID-19 impact on Production of components |
16 | COVID-19 impact on Point of sale |
17 | Market Segmentation, Dynamics and Forecast by Geography, 2024-2030 |
18 | Market Segmentation, Dynamics and Forecast by Product Type, 2024-2030 |
19 | Market Segmentation, Dynamics and Forecast by Application, 2024-2030 |
20 | Market Segmentation, Dynamics and Forecast by End use, 2024-2030 |
21 | Product installation rate by OEM, 2023 |
22 | Incline/Decline in Average B-2-B selling price in past 5 years |
23 | Competition from substitute products |
24 | Gross margin and average profitability of suppliers |
25 | New product development in past 12 months |
26 | M&A in past 12 months |
27 | Growth strategy of leading players |
28 | Market share of vendors, 2023 |
29 | Company Profiles |
30 | Unmet needs and opportunity for new suppliers |
31 | Conclusion |
32 | Appendix |