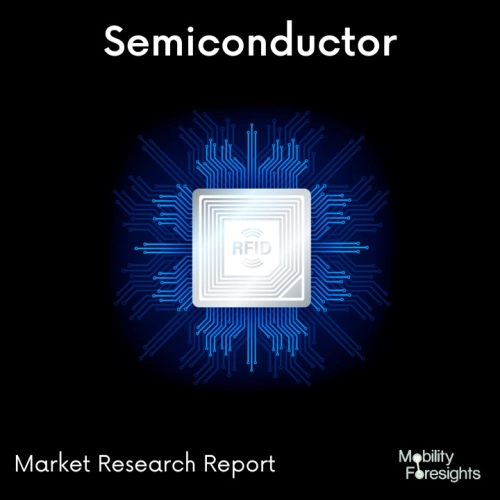
- Get in Touch with Us
Last Updated: Apr 25, 2025 | Study Period:
Industrial MCU are by definition useless without a connection to the outside world. They were created to manage sequential and parallel operations, execute conditional responses, and serve as a hub for inputs and outputs.
Control defines their function, and since they are programmable, control is managed by logic. Although they mainly rely on analog/digital conversion, they are fundamentally built as interfaces to the analog world.
The control process is frequently driven by the digital representation of an analog parameter, which is typically taken from a sensor of some kind. No application makes this clearer than automation.
MCUs have become more popular due to their capacity to manage intricate and huge mechanical systems with a small, reasonably priced piece of silicon.
The Global Industrial MCU market accounted for $XX Billion in 2023 and is anticipated to reach $XX Billion by 2030, registering a CAGR of XX% from 2024 to 2030.
Industrial MCU makers recognize the significance of sensors in automation and are starting to create optimized analog front ends that give inductive, capacitive, and resistive sensors a specialized interface. Some of these front ends, like the LESENSE (Low Energy Sensor) interface in Energy Micro's series of ultra-low power Industrial MCU, are even intended to function independently.
The Industrial MCU core can configure it, and it can be used even while the rest of the device is in deep sleep mode because it has analog comparators, a DAC (digital to analog converter), and a low power sequencer.
The comparator outputs can be set up as interrupts to wake the CPU, and the DAC can be chosen as a comparator reference and excitation source.
The sequencer works off a 32 kHz clock and regulates activity. A configurable decoder is another component of the LESENSE technology, and it can be set up to only emit an interrupt when many sensor conditions are met at once. Energy Micro's EFM32 Industrial MCU Tiny Gecko Starter Kit, which features an LESENSE demonstration, is available from Digi-Key.
Energy Micro's Tiny Gecko line of Industrial MCU is based on the ARM Cortex-M3 and targets the industrial automation application areas of temperature, vibration, pressure, and motion sensing. It operates at up to 32 MHz
In preparation for the next era of advanced industrial and IoT edge computing, NXP launched its new MCX portfolio of microcontrollers. The MCU Xpresso suite of development tools and software, which is extensively used, supports the portfolio, which consists of four series of devices developed on a similar platform. With this unified offering, developers may accelerate development by maximising software reuse throughout the portfolio.
Additionally, the portfolio includes the initial implementation of NXP's brand-new, specialised neural processing unit (NPU) for accelerating inference at the edge, which offers up to 30x faster machine learning throughput than a CPU core alone. The MCU has seen a significant evolution over the past few decades, driven by the growth of edge devices.
The next generation of intelligent applications will need a new class of MCUs, which will be at the centre of many of today's edge applications, but which will also enable developers to navigate a complex landscape of power, performance, and security requirements, as well as connectivity options, while balancing total system cost and energy efficiency.
The MCX portfolio will provide the flexibility required to handle this challenge since it is built on a shared foundation of key technologies and supported by a unified software suite for maximum software reuse.
Developers are free to invest in distinctive elements of their design thanks to the diversity of the MCX portfolio, which enables them to choose devices that best suit their application demands.
The four series in the MCX portfolio are made to be simple to use, easy to migrate to, and easy to scale up or down as needed while maximizing software reuse to reduce development costs. The portfolio is built on high-performance Arm Cortex-M CPUs and incorporates a vast array of peripherals for design flexibility.
To further improve the real-time performance of edge applications, MCX devices have up to 1MB of on-chip SRAM, low power cache, and advanced memory management controllers in addition to up to 4MB of on-chip flash memory. The software development environment for machine learning (eIQ® ML) from NXP will allow both machine learning and run-time inference.
Developers can train ML models for either the NPU or the CPU core and then deploy them on the MCU by using the user-friendly tools provided by eIQ. In addition to secure boot with an immutable root-of-trust, hardware accelerated cryptography, and, on some families, a built-in Edge Lock® secure subsystem, MCX families developed in accordance with NXP's security-by-design methodology will provide these features.
They are entering a new era of edge computing in order to get closer to the landmark of 75 billion connected devices, necessitating a fundamental rethinking of how to best architect a flexible MCU portfolio that is scalable, optimized, and can serve as the basis for energy-efficient industrial and IoT edge applications today and in the decades to come.
INDUSTRIAL MCU MARKET KEY PLAYERS
Sl no | Topic |
1 | Market Segmentation |
2 | Scope of the report |
3 | Abbreviations |
4 | Research Methodology |
5 | Executive Summary |
6 | Introduction |
7 | Insights from Industry stakeholders |
8 | Cost breakdown of Product by sub-components and average profit margin |
9 | Disruptive innovation in the Industry |
10 | Technology trends in the Industry |
11 | Consumer trends in the industry |
12 | Recent Production Milestones |
13 | Component Manufacturing in US, EU and China |
14 | COVID-19 impact on overall market |
15 | COVID-19 impact on Production of components |
16 | COVID-19 impact on Point of sale |
17 | Market Segmentation, Dynamics and Forecast by Geography, 2024-2030 |
18 | Market Segmentation, Dynamics and Forecast by Product Type, 2024-2030 |
19 | Market Segmentation, Dynamics and Forecast by Application, 2024-2030 |
20 | Market Segmentation, Dynamics and Forecast by End use, 2024-2030 |
21 | Product installation rate by OEM, 2023 |
22 | Incline/Decline in Average B-2-B selling price in past 5 years |
23 | Competition from substitute products |
24 | Gross margin and average profitability of suppliers |
25 | New product development in past 12 months |
26 | M&A in past 12 months |
27 | Growth strategy of leading players |
28 | Market share of vendors, 2023 |
29 | Company Profiles |
30 | Unmet needs and opportunity for new suppliers |
31 | Conclusion |
32 | Appendix |