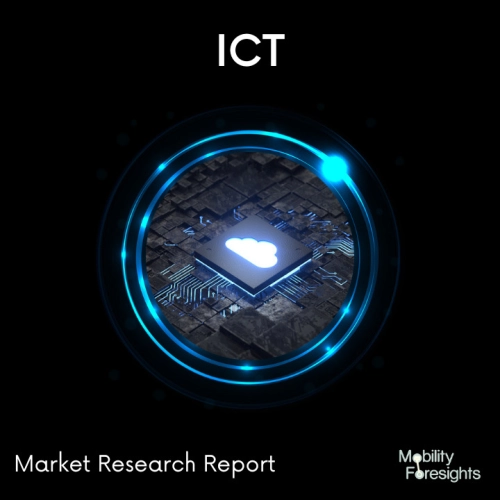
- Get in Touch with Us
Last Updated: Apr 25, 2025 | Study Period: 2024-2030
Many industrial applications, including quality control, inspection, and monitoring, call for the usage of industrial robotic cameras, which are video systems built to be installed on robotic arms or gantries.
These cameras can take photos and videos of objects and processes with a high degree of accuracy and detail since they are often fitted with features like high-resolution imaging, precise focusing, and zoom capabilities.
Manufacturing, automotive, aerospace, and other sectors where quality control and inspection are crucial frequently use industrial robotic cameras.
To capture images and videos of particular areas of interest, they can be programmed to move and change their focus and zoom levels. They can also be integrated with other systems to enable real-time monitoring and analysis of production processes.
The ability to function in challenging or dangerous conditions, their high level of precision and accuracy, and their capacity to record detailed photos and movies from a variety of angles are a few of the main benefits of industrial robotic cameras.
Also, they may be utilised to automate routine inspection operations, which will decrease the need for manual labour and boost production.
For manufacturers and other industrial businesses wishing to enhance their quality control and inspection procedures, lower costs, and boost productivity, industrial robotic cameras are a potent tool.
Global industrial robotic camera market accounted for $XX Billion in 2023 and is anticipated to reach $XX Billion by 2030, registering a CAGR of XX% from 2024 to 2030.
Robots operating in both indoor and outdoor situations can now use the ZED-X stereo camera range from Stereolabs.
The camera has a 3.0 m pixel size for both low-light and bright circumstances, a 1920 x 1200 global shutter RGB sensor, and rendering speeds up to 120 frames per second.
For precise object detection during core process automation, it additionally incorporates an IMU that combines a 16-bit digital triaxial accelerometer and a 16-bit digital triaxial gyroscope.
To aid automate visual inspections of cutting tool edges at high speed and with great accuracy, Nidec Machine Tool has introduced two new robot cameras for hobbing and broaching machines.
These robot cameras employ a digital camera to swiftly and accurately capture photos of cutting tool edges while preserving the graphic data of those images.
By entering a tool's specs into a robot camera, a user can instruct it to choose which photographs to take of tools of various forms, identify any missing pieces on the edge of a cutting edge, and any coatings that have come loose, all while determining whether any visual issues are present.
Sl no | Topic |
1 | Market Segmentation |
2 | Scope of the report |
3 | Abbreviations |
4 | Research Methodology |
5 | Executive Summary |
6 | Introduction |
7 | Insights from Industry stakeholders |
8 | Cost breakdown of Product by sub-components and average profit margin |
9 | Disruptive innovation in the Industry |
10 | Technology trends in the Industry |
11 | Consumer trends in the industry |
12 | Recent Production Milestones |
13 | Component Manufacturing in US, EU and China |
14 | COVID-19 impact on overall market |
15 | COVID-19 impact on Production of components |
16 | COVID-19 impact on Point of sale |
17 | Market Segmentation, Dynamics and Forecast by Geography, 2024-2030 |
18 | Market Segmentation, Dynamics and Forecast by Product Type, 2024-2030 |
19 | Market Segmentation, Dynamics and Forecast by Application, 2024-2030 |
20 | Market Segmentation, Dynamics and Forecast by End use, 2024-2030 |
21 | Product installation rate by OEM, 2023 |
22 | Incline/Decline in Average B-2-B selling price in past 5 years |
23 | Competition from substitute products |
24 | Gross margin and average profitability of suppliers |
25 | New product development in past 12 months |
26 | M&A in past 12 months |
27 | Growth strategy of leading players |
28 | Market share of vendors, 2023 |
29 | Company Profiles |
30 | Unmet needs and opportunity for new suppliers |
31 | Conclusion |
32 | Appendix |