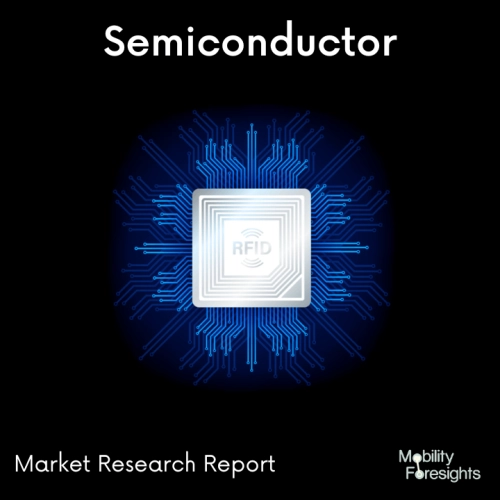
- Get in Touch with Us
Last Updated: Apr 25, 2025 | Study Period: 2024-2030
KEY FINDINGS
The global industrial vibration sensor market is poised for significant growth over the next six years, with estimates suggesting a market size of USD xx billion in 2023 and reaching USD xx billion by 2030. This translates to a Compound Annual Growth Rate (CAGR) of xx%.
Innovations in MEMS technology, wireless connectivity, AI integration, and energy harvesting are driving the evolution of vibration sensors, enabling more effective predictive maintenance and operational optimization across various industries. These advancements are helping companies improve equipment reliability, reduce downtime, and enhance overall productivity. Also, the technological advancements in vibration sensors have significantly expanded their capabilities, making them more accurate, reliable, and versatile.
Numerous sales opportunities and steadfast growth in Asia Pacific is driven due to multiple promising factors. Rapid urbanization and infrastructure development in the region create a high demand for vibration monitoring solutions to maintain the health and safety of structures such as bridges, buildings, and transportation systems.
Accelerometers have seen dominant sales compared to other industrial sensors due to a variety of factors related to their versatility, technological advancements, broad range of applications, and their critical role in modern industrial practices. Another prominent factor, Accelerometers are used in various industries, including automotive, aerospace, consumer electronics, healthcare, and industrial automation. Their ability to measure acceleration, vibration, and tilt makes them versatile tools for numerous applications.
Smart vibration sensors with embedded microprocessors and digital signal processing (DSP) capabilities can perform complex data analysis directly at the sensor level. This reduces the need for external processing and speeds up decision-making. Sensors with onboard diagnostics can self-monitor their performance and report issues, ensuring reliable operation and reducing maintenance requirements.
INTRODUCTION
Industrial vibration sensors, also known as vibration transducers or accelerometers, are devices used to measure and monitor mechanical vibrations in industrial machinery and equipment. These sensors detect changes in acceleration, velocity, or displacement caused by vibration, allowing for the assessment of equipment health, the identification of potential faults or defects, and the implementation of predictive maintenance strategies. Industrial vibration sensors play a crucial role in various industries, including manufacturing, automotive, aerospace, energy, and transportation, where the reliable operation of machinery is essential for productivity, safety, and efficiency. sensing element, signal conditioning circuitry, output interface, mounting hardware are considered as prominent components for vibration sensor.
The development of smart cities involves extensive use of sensors for monitoring infrastructure health, including bridges, buildings, and public transportation systems. Vibration sensors help in detecting structural issues early, ensuring public safety. In regions with aging infrastructure, there is a growing need for continuous monitoring and maintenance, which drives the demand for vibration sensors.
While industrial vibration sensors are invaluable tools for monitoring and maintenance, they come with limitations related to environmental sensitivity, installation and calibration, data management, power supply, cost, interference, frequency range, durability, system integration, and security. Addressing these challenges involves careful planning, selecting the right sensor for the application, ensuring proper installation and maintenance, and leveraging advanced data analytics and cybersecurity measures. By understanding and mitigating these limitations, companies can maximize the benefits of vibration sensors and improve their operational efficiency and reliability.
The Global Industrial Vibration Sensor Market accounted for $XX Billion in 2023 and is anticipated to reach $XX Billion by 2030, registering a CAGR of XX% from 2024 to 2030.
Smart Sensors and Integrated Electronics: Smart vibration sensors with embedded microprocessors and digital signal processing (DSP) capabilities can perform complex data analysis directly at the sensor level. This reduces the need for external processing and speeds up decision-making. Sensors with onboard diagnostics can self-monitor their performance and report issues, ensuring reliable operation and reducing maintenance requirements.
Multi-Axis Sensing: Modern vibration sensors can measure vibrations along multiple axes (x, y, z), providing a comprehensive understanding of the vibrational behavior of machinery and structures. This is crucial for detecting complex vibration patterns and anomalies. Multi-axis sensors enable more detailed and accurate analysis of vibrational data, improving fault detection and diagnosis.
Rugged and Robust Designs: Advances in sensor housing materials and designs have led to more rugged and durable vibration sensors that can withstand harsh environmental conditions, such as extreme temperatures, moisture, dust, and chemicals. Improved durability extends the operational lifespan of vibration sensors, reducing replacement costs and downtime.
Plug-and-Play Solutions: Plug-and-play vibration sensors simplify installation and setup, reducing the time and expertise required to deploy these systems. This ease of use encourages broader adoption across industries. Improved interfaces and software tools make it easier for users to configure, monitor, and analyze sensor data, enhancing user experience and accessibility.
POLYN Technology,a fabless semiconductor firm,has introduced its advanced NASP-based vibration monitoring.POLYN provides application-specific Neuromorphic Analogue Signal Processing (NASP) technology and products. Vibration monitoring is initially applied in an analogue neuromorphic design by POLYN. Typically, these AI-powered systems operate in the cloud and consume a lot of power, but POLYN provides it locally on a tiny VibroSense chip that uses very little power.
Fraunhofer researchershave created ahelmet with an integrated acceleration vibration sensor.The vibration sensors integrated helmet will mainly use by drivers of construction vehicles. The sensor on the helmet records detrimental vibrations that are felt by the body. Software examines the sensor data and displays the stress level of the impacted individual. This makes it possible to execute appropriate relief actions. The sensor is a flexible piezo-electret film. The combined Fraunhofer booth at the Hannover Messe will feature a demonstration model for the Flexeras project.
The Vibration Metreis the newest wireless sensor offered byWorldsensing. The gadget has a longer battery life, a greater communications range, and a more affordable pricing point than similar devices. It measures vibrations using a tri-axial accelerometer. Peak particle velocity (PPV) and vibration frequency are two examples of the metrics that the Vibration Metre utilises an advanced algorithm to detect threshold violations of. It continuously collects data at 1000MHz on the spot, which is sent to the management tools of engineering providers via a cellular gateway. To be compatible with other company devices, it uses Worldsensing's 15km Long Range (LoRa) antenna.
Advantechhas launched theWISE-2460, a cutting-edge vibration detection system. With a Z-axis sensitivity range of 5 to 10000Hz, this sophisticated device supports Modbus/RTU protocols for RS-485 serial communication purposes. WISE-2460 is an IP68-rated shell housing an ARM Cortex-M7 processor, a temperature sensor, and a high-detection-range Z-axis accelerometer. It is intended for use in harsh environments to monitor equipment RPM and frequency detection ranges. The device's user-friendly Advantech WISE Studio software streamlines alarm threshold control and setting.
Sr. No | Topic |
1 | Market Segmentation |
2 | Scope of the Report |
3 | Research Methodology |
4 | Executive Summary |
5 | Introduction |
6 | Average B-2-B Selling Price in Past 5 Years |
7 | Insights from Industry Stakeholders |
8 | Cost Breakdown of Product Components and Average Profit Margin |
9 | Disruptive Innovation in the Industry |
10 | Technological Innovations in Global industrial vibration sensor Market 2024-2030 |
11 | Advancements in Automation Framework |
12 | Integration of AI and Machine Learning |
13 | Sensor Technology Innovations |
14 | Evolution of Predictive Maintenance |
15 | Real-time Sensor Enhancements |
16 | Adoption of Cloud Robotics Solutions |
17 | Progress in Wireless and IoT integration |
18 | Development of Robust Safety Features |
19 | Interoperability and Compatibility Improvements |
20 | Scalability and Modularity Enhancements |
21 | New Product Development in the Past 12 Months |
22 | Market Size, Dynamics, and Forecast by Geography (2024-2030) |
23 | Market Size, Dynamics, and Forecast by Type (2024-2030) |
24 | Market Size, Dynamics, and Forecast by Equipment (2024-2030) |
25 | Market Size, Dynamics, and Forecast by Application (2024-2030) |
26 | Competitive Landscape and Market Share Analysis |
27 | Growth Strategy of Leading Players |
28 | Market Share of Vendors (2023) |
29 | Company Profiles |
30 | Unmet Needs and Opportunities for New Suppliers |
31 | Conclusion |