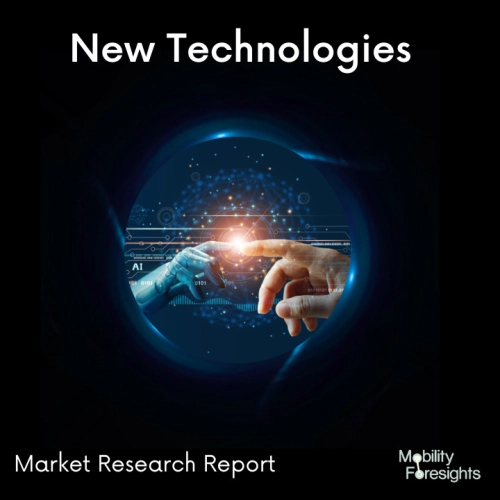
- Get in Touch with Us
Last Updated: Apr 25, 2025 | Study Period: 2023-2030
Making plastic goods involves a crucial procedure called injection moulding. It is a method that makes it possible to quickly produce similar goods in big quantities.
This can be high-precision technical components or disposable consumer items. Injection moulding can be used to process even thermoplastics.
In this technique, nylon, polycarbonate, polypropylene, and acrylonitrile butadiene styrene are the components that are most frequently employed.
The majority of plastic products made in India are created through the process of injection moulding. Injection-moulded parts and components are used in almost all industrial industries.
Wheelie bins, car bumpers, and various large and small components are examples.We can make the same parts or components thousands or even millions of times thanks to the method.
The ability of the injection moulding method to produce in huge quantities is its key benefit. Although developing and constructing the mould will initially cost a lot, the subsequent procedure of making each unit of the plastic item is quite inexpensive.
Compared to conventional techniques, injection moulding yields a very little amount of trash. The scrap rate is significantly lower when using 3D printing.
The four sections of the injection moulding process that produce waste plastics are the spruce, the gate positions, the runners, and any mould leaks.
The majority of the part design and prototype will be carried out utilising a 3D printer and a different material from the actual manufacture. Thousands of injection-moulded prototypes must be produced using an injection mould tool.
The Globalinjection moulded consumer goodsmarket accountedfor $XX Billion in 2021 and is anticipated to reach $XX Billion by 2030, registering a CAGR of XX% from 2022 to 2030.
A manufacturing technique called injection moulding is used to create parts in enormous quantities, ranging from thousands to millions.
A hollow mould is filled with melted resin until it is entirely filled. High temperature and high pressure are used in the injection moulding process to completely fill the interior with molten plastic resin or liquid polymers.
After cooling, the moulds are opened to release the finished plastic parts. You have a variety of techniques to pick from when developing a product that calls for moulded plastic components, based on the type of application and part you want to make.
Injection moulding is one of the most widely used techniques for producing plastic parts of high quality and at a reasonable price.
Plastic is employed in a wide range of consumer goods applications, from athletic equipment and electronics to product packaging and in-store displays.
The problem is still getting high-quality products on shelves quickly to fulfil consumer demand and outperform rival brands, regardless of the shape, size, or complexity of the consumer goods that are being created.
For the majority of plastic consumer goods, injection moulding has long been the preferred production technique due to its ability to manufacture big volumes swiftly and affordably.
Injection moulding, the penultimate stage of product production, is a technique that involves heating plastic material and injecting it under pressure into a closed metal mould.
The desired shape, such as a television remote or a piece of plastic drinkware, is subsequently achieved by cooling the molten plastic until it hardens.
Sl no | Topic |
1 | Market Segmentation |
2 | Scope of the report |
3 | Abbreviations |
4 | Research Methodology |
5 | Executive Summary |
6 | Introduction |
7 | Insights from Industry stakeholders |
8 | Cost breakdown of Product by sub-components and average profit margin |
9 | Disruptive innovation in the Industry |
10 | Technology trends in the Industry |
11 | Consumer trends in the industry |
12 | Recent Production Milestones |
13 | Component Manufacturing in US, EU and China |
14 | COVID-19 impact on overall market |
15 | COVID-19 impact on Production of components |
16 | COVID-19 impact on Point of sale |
17 | Market Segmentation, Dynamics and Forecast by Geography, 2023-2030 |
18 | Market Segmentation, Dynamics and Forecast by Product Type, 2023-2030 |
19 | Market Segmentation, Dynamics and Forecast by Application, 2023-2030 |
20 | Market Segmentation, Dynamics and Forecast by End use, 2023-2030 |
21 | Product installation rate by OEM, 2023 |
22 | Incline/Decline in Average B-2-B selling price in past 5 years |
23 | Competition from substitute products |
24 | Gross margin and average profitability of suppliers |
25 | New product development in past 12 months |
26 | M&A in past 12 months |
27 | Growth strategy of leading players |
28 | Market share of vendors, 2023 |
29 | Company Profiles |
30 | Unmet needs and opportunity for new suppliers |
31 | Conclusion |
32 | Appendix |