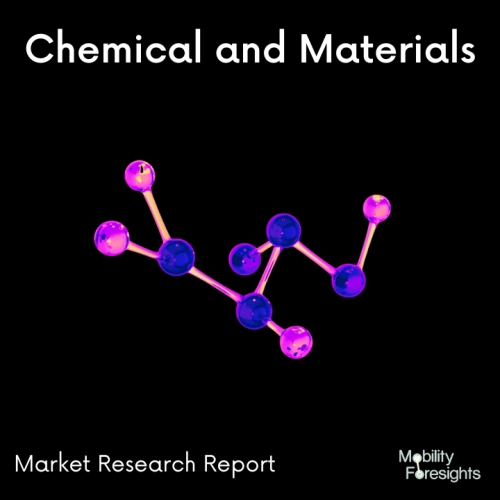
- Get in Touch with Us
Last Updated: Apr 25, 2025 | Study Period: 2024-2030
An electroactive polymer (EAP) is a type of polymer that responds to an electric field by changing size or shape. This kind of material is most frequently used in actuators and sensors.
The ability of an EAP to withstand significant forces while undergoing significant deformation is a common characteristic.
Ceramic piezoelectric materials make up the majority of previous actuators. Even though these materials can withstand significant forces, the majority of the time, they will only deform to a fraction of a percent.
It has been demonstrated that some EAPs can exhibit strains of up to 300 percent, which is significantly higher than that of any ceramic actuator.
In the field of robotics, the creation of artificial muscles is one of the most common uses for EAPs; As a result, the term "artificial muscle" is frequently used to describe an electroactive polymer.
In electroactive polymers (EAPs), electromechanical coupling has been widely used for actuation and is also being studied more and more for sensing chemical and mechanical stimuli.
EAPs are a one-of-a-kind group of materials that can conform to a variety of shaped surfaces and have low moduli and high strain capabilities. They are appealing for applications like soft tissue interface and wearable sensors because of these features.
The Global Intelligent sensor Electroactive polymer market accounted for $XX Billion in 2023 and is anticipated to reach $XX Billion by 2030, registering a CAGR of XX% from 2024 to 2030.
EAPs comprise a family of promising materials for sensing, but are still new to most researchers working on sensor-related topics.
Since there is no material that can cover all sensory requirements, the selection of a material should be made carefully to suit individual requirements .
EAPs should certainly be considered complementary to conventional sensing materials, especially in areas where high strains and conformity to soft materials is desired.In this article, we review such materials and aspects of their associated sensing mechanisms.
EAPs are attractive to people working on electrically driven soft actuators , as some EAPs such as dielectric elastomers can handle much larger strains than their equivalent conventional actuator materials, such as piezoelectric ceramics.
EAP artificial muscles are strongly comparable to biological muscle due to their response to electrical stimulation, though their operation mechanism is significantly different.
Besides actuators, EAPs have revealed their potential in other applications such as sensors, electronic components and energy generators.
EAPs are suitable for sensory applications ranging from haptic sensing to blood pressure and pulse rate monitoring and even chemical sensing.
This is due to numerous favourable properties: facile fabrication, high mechanical flexibility, customizable electromechanical coupling properties and tailorable geometries. Furthermore, coupling EAPs into micro-electro-mechanical systems (MEMS) has been discussed by both the EAP and MEMS communities.
Sl no | Topic |
1 | Market Segmentation |
2 | Scope of the report |
3 | Abbreviations |
4 | Research Methodology |
5 | Executive Summary |
6 | Introduction |
7 | Insights from Industry stakeholders |
8 | Cost breakdown of Product by sub-components and average profit margin |
9 | Disruptive innovation in the Industry |
10 | Technology trends in the Industry |
11 | Consumer trends in the industry |
12 | Recent Production Milestones |
13 | Component Manufacturing in US, EU and China |
14 | COVID-19 impact on overall market |
15 | COVID-19 impact on Production of components |
16 | COVID-19 impact on Point of sale |
17 | Market Segmentation, Dynamics and Forecast by Geography, 2024-2030 |
18 | Market Segmentation, Dynamics and Forecast by Product Type, 2024-2030 |
19 | Market Segmentation, Dynamics and Forecast by Application, 2024-2030 |
20 | Market Segmentation, Dynamics and Forecast by End use, 2024-2030 |
21 | Product installation rate by OEM, 2023 |
22 | Incline/Decline in Average B-2-B selling price in past 5 years |
23 | Competition from substitute products |
24 | Gross margin and average profitability of suppliers |
25 | New product development in past 12 months |
26 | M&A in past 12 months |
27 | Growth strategy of leading players |
28 | Market share of vendors, 2023 |
29 | Company Profiles |
30 | Unmet needs and opportunity for new suppliers |
31 | Conclusion |
32 | Appendix |