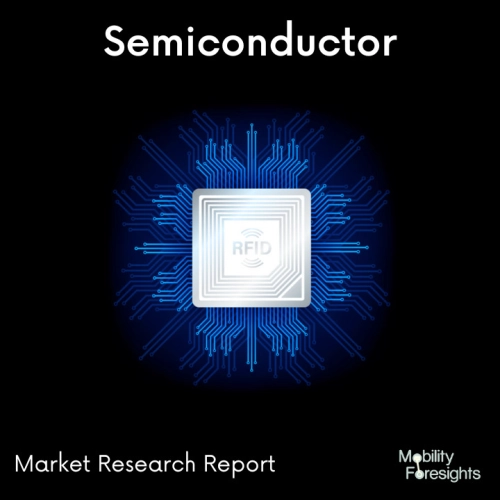
- Get in Touch with Us
Last Updated: Apr 25, 2025 | Study Period: 2024-2030
Interfaces for sensors. Sensor interface ICs give systems the ability to extract data from the input signal produced by sophisticated sensors and convert it into an appropriate output signal that is simple for the host system to display or process. Even in severe conditions, ams sensor interfaces provide great accuracy, precision, and sensitivity.
Analog-to-digital conversion is used with other signal conditioning techniques, such as amplification and filtering, for sensor interfacing. Even if the analog-to-digital converter (ADC) is built inside your microcontroller, the sensor must still be compatible with the ADC input.
Most likely, the sensor manufacturer will have some recommendations for connections and conditioning. Upon selecting a sensor, the tool directs you to a suggested design that has a schematic, a complete bill of materials (BOM), test results, specifications, and other helpful information.
The designs are the outcome of numerous engineers working together to create an ideal consensus design. Included is the ADC.
The Global Interface sensors market accounted for $XX Billion in 2023 and is anticipated to reach $XX Billion by 2030, registering a CAGR of XX% from 2024 to 2030.
The A17700, an automotive-grade interface IC for resistive bridge pressure sensors with cutting-edge signal conditioning algorithms, was unveiled today by Allegro Micro Systems, Inc. ("Allegro"), a global leader in sensing and power solutions for motion control and energy-efficient systems.
The A17700 combines premium performance and better system economy with multiple interface options all in a tiny form factor and is built on decades of experience in automotive sensors.
Flexible compensation algorithms for accuracy over temperature and sensing bridge variation are among the qualities that lead the market. Supply of precise pressure data in low delay analogue, PWM, or SENT outputs; automotive EMC robustness with a minimum of external components and AEC-Q100 Grade 0 accreditation;
The A17700 can be configured for resistive bridge pressure sensors in a variety of crucial applications found in today's efficiently designed cars, from high-pressure systems like dynamic brake systems (DBS) in turbo and hybrid electric vehicles (HEV) or gasoline direct injection (GDI) to medium and low-pressure systems like brake boosters, HVAC applications for electrified vehicles, and automatic transmission oil management.
Renesas introduced an integrated LIN interface sensor signal conditioner for HVAC systems in electric and hybrid vehicles.
The single-package sensor signal conditioner (SSC), used in HVAC applications for plug-in hybrid electric vehicle (PHEV), battery electric vehicle (BEV), and fuel-cell electric vehicle (FCEV) climate control systems, offers best-in-class performance, increased design flexibility, and cost efficiency in a small package.
It is possible to configure the ZSSC4132 for almost all resistive bridge sensors. This adaptability, together with the SSC's industry-leading performance levels, integrated LIN PHY, compact package footprint, and AEC-Q100 Grade 0 certifications, make it the perfect choice for small automotive sensor modules that must meet end-of-line (EOL) calibration criteria and have limited space and financial constraints.
OEMs are looking for solutions to increase system efficiency while retaining high performance and adhering to strict budgetary limits because HVAC plays a big impact in EV battery range.
Customers may easily and affordably scale the development of their HVAC systems for mid-range to high-end EVs and HEVs by using the ZSSC4132, which offers access to a comprehensive SSC solution that is already LIN certified.
The ZSSC4132 combines best-in-class analogue front end (AFE) technology for improved sensor signal conditioning with digital calibration to greatly lower the noise sensitivity and give high accuracy for pressure and temperature readings.
Through a reduction in the demand for external components, the SSC's integration lowers overall bill of materials (BOM) requirements. Additionally, users can minimize calibration efforts using the ZSSC4132's special digital calibration capability, which further lowers system costs.
The KEVA/KECA/KEVCY medium voltage sensors from ABB are compatible with the new model of PM174/5 Advanced Power Quality Analyzers that SATEC is introducing.
These distinctive sensors have a built-in potential transformer and current transducer combination, integrated into an RJ45 3VAC output, originally intended for connecting to digital protection relays. This interface is used in SATEC's concept to use these current sensors' outputs for extremely accurate power metering.
Protection equipment's readings are typically not as accurate as the PM174/5's and do not give a network's power quality profile. By using this idea, it is also not necessary to build expensive metering cubicles with all the necessary equipment (MV CT and PT).
Sl no | Topic |
1 | Market Segmentation |
2 | Scope of the report |
3 | Abbreviations |
4 | Research Methodology |
5 | Executive Summary |
6 | Introduction |
7 | Insights from Industry stakeholders |
8 | Cost breakdown of Product by sub-components and average profit margin |
9 | Disruptive innovation in the Industry |
10 | Technology trends in the Industry |
11 | Consumer trends in the industry |
12 | Recent Production Milestones |
13 | Component Manufacturing in US, EU and China |
14 | COVID-19 impact on overall market |
15 | COVID-19 impact on Production of components |
16 | COVID-19 impact on Point of sale |
17 | Market Segmentation, Dynamics and Forecast by Geography, 2024-2030 |
18 | Market Segmentation, Dynamics and Forecast by Product Type, 2024-2030 |
19 | Market Segmentation, Dynamics and Forecast by Application, 2024-2030 |
20 | Market Segmentation, Dynamics and Forecast by End use, 2024-2030 |
21 | Product installation rate by OEM, 2023 |
22 | Incline/Decline in Average B-2-B selling price in past 5 years |
23 | Competition from substitute products |
24 | Gross margin and average profitability of suppliers |
25 | New product development in past 12 months |
26 | M&A in past 12 months |
27 | Growth strategy of leading players |
28 | Market share of vendors, 2023 |
29 | Company Profiles |
30 | Unmet needs and opportunity for new suppliers |
31 | Conclusion |
32 | Appendix |