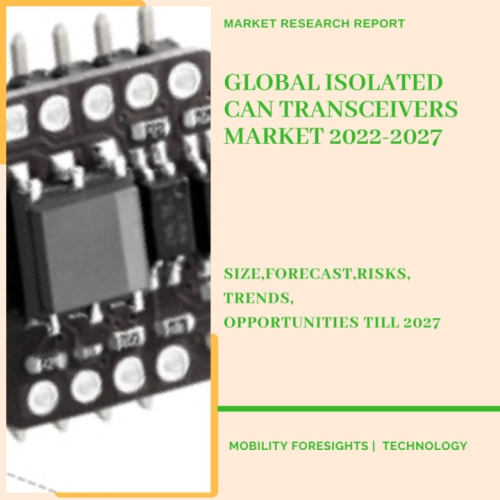
- Get in Touch with Us
Last Updated: Apr 25, 2025 | Study Period: 2022-2027
Separating the CAN occurs whenever the appropriate measures to address in a CAN networks have bigger grounding possible differences (GPDs) than that of the transceiver's permitted line frequency voltage range, for example, due to extended communications distances or noisy systems grounding (as in motor driving applications).
These single-ended data bits on the current side of the screen are segregated and linked to the CAN transceiver, which transforms them into divergent CAN protocol. Grounded prospective discrepancies between components, generalized noise generators also including common-mode energies and radiating frequency, and high-voltage noise and spikes.
S No | Overview of Development | Development Detailing | Region of Development | Possible Future Outcomes |
1 | The new generation Isolated 485 CAN Transceiver with integrating Chipset SIP Technology | The Chiplet SIP platform to launch the new generation chip level 485 CAN family referred to as R4 receivers. | Global | This would enhance better Technological Controls |
2 | Isolated CAN Transceivers Aimed at Improving the Robustness of Industrial Communications | Maxim Integrated has released a new family of isolated CAN transceivers to aid in the improvement of communication uptime in the industrial sector. | Global | This would enhance better Technological Controls |
3 | Smallest reinforced isolated CAN FD transceivers deliver the industry's highest bus fault protection | With TI's new transceivers delivering the greatest operating voltage, engineers may improve communication reliability and protection in industrial and automotive applications. | Global | This would enhance better Technological Controls |
4 | Interconnecting multiple system - Novel solution for CAN bus application | The Controller Area Network (CAN) is a communication protocol created by the BOSCH business and standardised by ISO-11898 in 1993. | Global | This would enhance better Technological Controls |
5 | Galvanically Isolated CAN Bus Transceivers Protect Networks Against Destructive Energy | To protect a network from this harmful energy, the CAN bus system must be galvanically isolated from other local node circuits. | Global | This would enhance better Technological Controls |
Processors are increasingly being used in automotive and aerospace applications via controller area network (CAN) networking buses.
The latter technology is the application must compensate for electromechanical noisy environments across a wide frequency range, from high-frequency radiant energy electromagnetic fields (EMI) to widely accepted performed interference, as well as voltage swell caused by the correlation and disassociation of load variations like electric engines, retransmits, as well as switching operation alternators/generators.
Analog Devices is a leading mobiliser of the CAN Transceivers technology in the market. The latest integrated device combines a 2-channel isolation as well as a CAN transceiver into such a single isolated outlines electronic component (SOIC) surface-mount packaging using Analog Devices, Inc.'s iCoupler technologies.
For CAN and CAN FD systems, the ADM3058E is just a completely isolated system. The ADM3058E separates the CAN microcontroller from the core network interface.
Texas Instruments is part of the component manufacture trending companies in the current industry. The ISO1050 is a polarisation separated CAN transceiver which complies with ISO11898-2 requirements. A silicon oxide (SiO2) insulating barrier separates the logical inputs and outputs buffering, providing electrical isolation of up to 5000 VRMS for ISO1050DW and 2500 VRMS for ISO1050DUB.
The mechanism inhibits disturbance current flow on a bit stream or even other circuitry from accessing the neighbourhood grounding when used in combination with isolated power supply.
Sl no | Topic |
1 | Market Segmentation |
2 | Scope of the report |
3 | Abbreviations |
4 | Research Methodology |
5 | Executive Summary |
6 | Introduction |
7 | Insights from Industry stakeholders |
8 | Cost breakdown of Product by sub-components and average profit margin |
9 | Disruptive innovation in the Industry |
10 | Technology trends in the Industry |
11 | Consumer trends in the industry |
12 | Recent Production Milestones |
13 | Component Manufacturing in US, EU and China |
14 | COVID-19 impact on overall market |
15 | COVID-19 impact on Production of components |
16 | COVID-19 impact on Point of sale |
17 | Market Segmentation, Dynamics and Forecast by Geography, 2022-2027 |
18 | Market Segmentation, Dynamics and Forecast by Product Type, 2022-2027 |
19 | Market Segmentation, Dynamics and Forecast by Application, 2022-2027 |
20 | Market Segmentation, Dynamics and Forecast by End use, 2022-2027 |
21 | Product installation rate by OEM, 2022 |
22 | Incline/Decline in Average B-2-B selling price in past 5 years |
23 | Competition from substitute products |
24 | Gross margin and average profitability of suppliers |
25 | New product development in past 12 months |
26 | M&A in past 12 months |
27 | Growth strategy of leading players |
28 | Market share of vendors, 2022 |
29 | Company Profiles |
30 | Unmet needs and opportunity for new suppliers |
31 | Conclusion |
32 | Appendix |