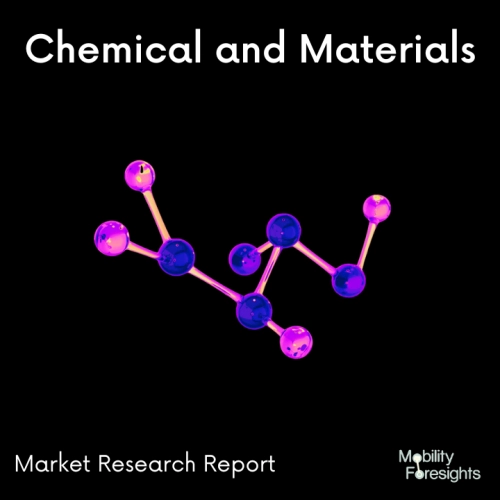
- Get in Touch with Us
Last Updated: Apr 25, 2025 | Study Period: 2023-2030
The level of air pollution can be even greater in industrial buildings, particularly for manufacturing plants or chemical processing facilities.
Additionally, carry over from the manufacturing process, such as dust particles, oil mist aerosols, and condensed vapors, can accumulate both inside and outside the equipment leading to issues with process quality, equipment maintenance, and worksite safety.
Industrial filtration involves the removal of contaminating particles from air and other gases. Many industrial processes require air filtration and separation systems not only to protect equipment, but to also protect the work environment.
Contaminants that are present during the manufacturing process can be extremely damaging to equipment. One of the most important roles of industrial filtration is to capture and remove these contaminants and contain them for proper removal and disposal.
For instance, vacuum pumps are commonly used in pharmaceutical manufacturing to remove moisture from a product to create a powdered substance.
During this process, some of the moisture and/or powder particles may be released into the air stream flowing to the vacuum pump.
This residue could eventually clog the equipment and damage rotating components. In this example, a liquid separator and a particulate filter would be used to protect the vacuum pump from both liquids and particulates.
The Italy Industrial Filters Market accounted for $XX Billion in 2022 and is anticipated to reach $XX Billion by 2030, registering a CAGR of XX% from 2023 to 2030.
Figeva Metal cartridge filters for fluids - metal cartridge filters for fluids feature filtering media composed of a woven surface of stainless steel micro-wire.
The metal cartridge filters for fluids are used mainly in applications with challenging operating conditions in terms of temperature and chemical compatibility, due in particular to the presence of organic and inorganic solvents.
The modest drop in pressure generated by these cartridges makes them suitable for use on high-viscosity liquids such as mineral or vegetable oils, gelatine and sugary syrups.
In many applications, it is possible to clean the cartridge, eliminating any contaminant that has become trapped.Having removed the filter from its housing, and can be washed it in an ultrasound bath, with a pressure washer or by brushing the filtering media.
Sl no | Topic |
1 | Market Segmentation |
2 | Scope of the report |
3 | Abbreviations |
4 | Research Methodology |
5 | Executive Summary |
6 | Introduction |
7 | Insights from Industry stakeholders |
8 | Cost breakdown of Product by sub-components and average profit margin |
9 | Disruptive innovation in the Industry |
10 | Technology trends in the Industry |
11 | Consumer trends in the industry |
12 | Recent Production Milestones |
13 | Component Manufacturing in US, EU and China |
14 | COVID-19 impact on overall market |
15 | COVID-19 impact on Production of components |
16 | COVID-19 impact on Point of sale |
17 | Market Segmentation, Dynamics and Forecast by Geography, 2023-2030 |
18 | Market Segmentation, Dynamics and Forecast by Product Type, 2023-2030 |
19 | Market Segmentation, Dynamics and Forecast by Application, 2023-2030 |
20 | Market Segmentation, Dynamics and Forecast by End use, 2023-2030 |
21 | Product installation rate by OEM, 2023 |
22 | Incline/Decline in Average B-2-B selling price in past 5 years |
23 | Competition from substitute products |
24 | Gross margin and average profitability of suppliers |
25 | New product development in past 12 months |
26 | M&A in past 12 months |
27 | Growth strategy of leading players |
28 | Market share of vendors, 2023 |
29 | Company Profiles |
30 | Unmet needs and opportunity for new suppliers |
31 | Conclusion |
32 | Appendix |