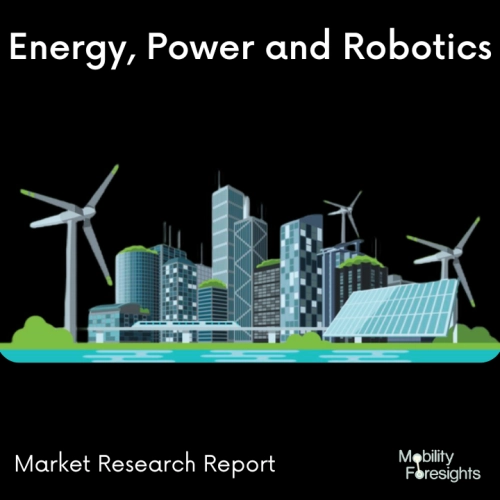
- Get in Touch with Us
Last Updated: Apr 25, 2025 | Study Period: 2024-2030
A robot with rotational joints is said to be articulated. Simple two-jointed robots all the way up to complex systems with ten or more interacting joints and materials are considered articulating robots.
Electric motors are just one of the many sources used to power them.industrial: For operations like assembling, welding, painting, packaging, and material handling, articulated robots are frequently used in the industrial sector.
The accuracy and speed with which these robots can complete these duties increases production and efficiency.Robots that have rotating joints are known as articulated robots. In the robotics community, these joints are frequently referred to as axes.
Rotating joints and up to 10 or more axes are features of articulated robots. As a result, they have more mobility, which increases their adaptability. Their dexterity and manner of movement nearly resemble a human arm. The manufacturing sector now cannot function without articulating robots. All three of the revolute joints on an articulated robot are used to enter the workspace.
Typically, the joints are set up in a "chain" so that one joint supports the next joint along the chain.a control strategy where the inputs or orders define each point along the desired motion path. The manipulator joints' synchronised motion regulates the path.
Material handling, assembling, welding, painting, and packing are just a few of the activities that these robots can automate. Companies can cut labour costs and increase productivity while maintaining quality standards by integrating articulated manipulators into their manufacturing lines.
Disadvantages Comparatively more expensive and requiring more complex control methods than other robot arms are articulated robots.Advantages precise, affordable, and skilled in many assembly techniques.
The Japan articulated robot market accounted for $XX Billion in 2022 and is anticipated to reach $XX Billion by 2030, registering a CAGR of XX% from 2023 to 2030.
2 Different Horizontal Articulated Scara Robot Types Are Introduced by Yaskawa "i3-Mechatronics" is a new addition to the MOTOMAN-SG Series' lineup that improves digital data solutions.
It is with great pleasure that Yaskawa Electric Corporation (Head Office: Kitakyushu City, Fukuoka Prefecture) announces the launch of sales of two models of horizontal articulated scara robots, the MOTOMAN-SG400 and MOTOMAN-SG650.
These robots are ideal for assembly and transportation processes of small components that demand high cycle times, in the 3C market (computers, home appliances and communications equipment).
A number of robots developed by Yaskawa have been commercialised and made available for use in a variety of tasks, including welding, handling, assembly, painting, moving liquid crystal panels and semiconductor wafers, among others.
In general industries other than the automobile industry, there has been a considerable demand for automation in recent years to increase productivity and lower manufacturing costs due to a growing labour shortage brought on by the fall in the working-age population.
The market for 3C items as well as other general industries like food, medical products, and cosmetics have a particularly strong demand for automation.
Aiming primarily at the assembly, transportation, packing, sorting, and inspection of small components in general industrial domains, two varieties of horizontal articulated scara robots with different reach have been launched.
In its long-term management plan, Yaskawa promotes a concept for a solution called "i3-Mechatronics" that aims to increase productivity and achieve zero downtime production lines through digital data solutions, including product-based automation and production site visualisation.
This concept is marketed under the slogan "Realisation of a new industrial automation revolution." Yaskawa will be able to respond to the changing needs of customers in the general industrial field and strengthen its capacity to suggest "i3-Mechatronics" by combining the small general purpose robots "GP Series," "MotoMINI," and the human collaborative robots "HC Series" with the recently launched horizontal articulated scara robot.
With the highest operational performance in its class and the ability to operate at high speeds and high precision, the standard cycle time* for the SG400 is 0.32 seconds and the SG650 is 0.29 seconds.
Reciprocating motion with a payload of 2 kg and a vertical distance of 25 mm in the horizontal plane.Principal Applications Small component assembly, transportation, packing, sorting, inspection, etc.
Servo motors, the primary component of industrial robots like MOTOMAN, are developed and optimised by Yaskawa. They are creating industrial robots by merging application technology that realises the best structures and functions for uses like welding and painting, in addition to control software technology that maximises this potential.
Through the steady operation of facilities and lines at customers' production sites, they help to improve productivity and quality by gathering, compiling, and analysing data about the state of the servo motors that make up the body and the outcomes of activities.
Yaskawa's industrial robots are now employed in a variety of industries in addition to the automotive sector, including the production of semiconductors, electric and electrical equipment, food, medical products, logistics, and biomedical items.
Arc welding produces a welding bead made of lines, which is typically utilised for automotive components like mufflers. For steady welding, this calls for high-tech motion control. In-house factories at Yaskawa have created servo motors.
Arc welding enables the production of beads of excellent quality. In order to reduce sputtering or sparks that shoot from the body frame, Yaskawa also offers a robot controller driven by AI that can change the angle at which the torch is held.