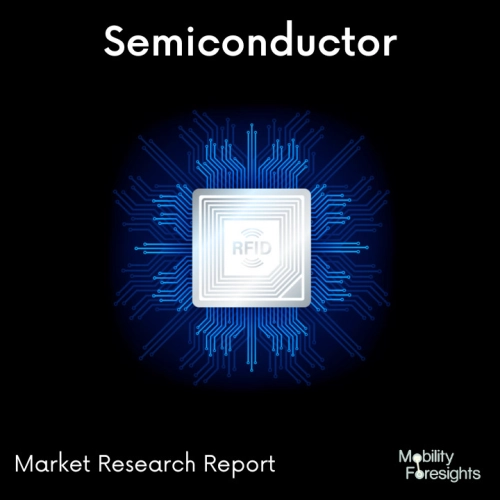
- Get in Touch with Us
Last Updated: Apr 25, 2025 | Study Period: 2023-2030
Factory automation sensors are instrumental components in the realm of industrial automation, revolutionizing manufacturing processes across various industries.
These sensors play a vital role in monitoring and controlling critical parameters within the production environment, enabling efficient and precise operation while ensuring the highest levels of productivity and safety.
This introduction provides a concise overview of factory automation sensors, highlighting their significance, types, and impact on modern industrial automation.
Sensors for factory automation are specialized apparatuses created to record and transform physical measurements into electronic impulses. Automated systems then make use of these signals to promote informed decision-making, control machinery, and enhance overall manufacturing processes.
Factory automation sensors enable enterprises to improve operational efficiency and product quality by supplying real-time data about the manufacturing environment, machine performance, and material status.
There are various types of factory automation sensors, each tailored to detect and measure specific physical parameters. Proximity sensors are utilized to detect the presence or absence of objects within a defined range, employing technologies such as inductive, capacitive, or optical principles.
Photoelectric sensors, on the other hand, utilize light beams to determine the presence, distance, or absence of objects, making them ideal for diverse industrial applications.
Pressure sensors are vital for monitoring and controlling the pressure levels of liquids, gasses, or air in pneumatic and hydraulic systems. Temperature sensors enable precise monitoring of thermal conditions in objects or environments, ensuring optimal process control and equipment protection.
Level sensors play a crucial role in monitoring the levels of liquids or solids in tanks or containers, enabling accurate inventory management and preventing overflow or depletion. Flow sensors measure the flow rate of liquids or gasses, facilitating precise control of fluid movement.
The integration of factory automation sensors within industrial automation systems brings numerous benefits. These sensors enable real-time data collection, precise control, predictive maintenance, and data-driven decision-making, ultimately leading to increased productivity, improved product quality, and enhanced worker safety.
Automation sensors reduce human intervention in repetitive tasks, minimizing errors and streamlining operations. Additionally, they contribute to energy efficiency by optimizing resource consumption and reducing costs.
Factory automation sensors are instrumental in driving the advancement of industrial automation. By providing real-time data and enabling precise control, these sensors revolutionize manufacturing processes, resulting in improved efficiency, productivity, and safety.
With their diverse range of types and functions, factory automation sensors continue to shape the future of industrial automation, facilitating innovation and optimization in a wide range of industries.
The Japan Factory Automation Sensor market accounted for $XX Billion in 2022 and is anticipated to reach $XX Billion by 2030, registering a CAGR of XX% from 2023 to 2030.
The TDK i3 Micro Module, the first module in the world with integrated edge AI and wireless mesh connectivity capability, was unveiled today by TDK Corporation (TSE:6762).
The i3 Micro Module combines the TI SimpleLinkTM platform, which uses the CC2652R7, an Arm® Cortex®-M4F multiprotocol 2.4-GHz wireless 32-bit microcontroller (MCU) for real-time monitoring, thanks to TDK's partnership with Texas Instruments (TI).
The new module also combines edge AI, mesh network functionality, TDK's IIM-42352 high-performance SmartIndustrialTM MEMS accelerometer and digital output temperature sensor, all of which facilitate data gathering, integration, and processing.
The wireless, ultracompact sensor on the i3 Micro Module allows users to sense at virtually any desired location without physical limitations like cables. This allows for the best Condition-based Monitoring (CbM) application by considerably speeding up the forecast of anomalies in machinery and equipment.
An ideal predictive maintenance system involves monitoring through real-time visualized empirical equipment data rather than relying on manpower and scheduled maintenance, understanding the health of machinery and equipment to help extend utilization life, and reducing production downtime by avoiding unexpected failures.
To support the growing global transition to smart factories, TDK created the i3 Micro Module for truly "smart" sensor node edge implementation aimed at a variety of production equipment.
Sl no | Topic |
1 | Market Segmentation |
2 | Scope of the report |
3 | Abbreviations |
4 | Research Methodology |
5 | Executive Summary |
6 | Introduction |
7 | Insights from Industry stakeholders |
8 | Cost breakdown of Product by sub-components and average profit margin |
9 | Disruptive innovation in the Industry |
10 | Technology trends in the Industry |
11 | Consumer trends in the industry |
12 | Recent Production Milestones |
13 | Component Manufacturing in US, EU and China |
14 | COVID-19 impact on overall market |
15 | COVID-19 impact on Production of components |
16 | COVID-19 impact on Point of sale |
17 | Market Segmentation, Dynamics and Forecast by Geography, 2023-2030 |
18 | Market Segmentation, Dynamics and Forecast by Product Type, 2023-2030 |
19 | Market Segmentation, Dynamics and Forecast by Application, 2023-2030 |
20 | Market Segmentation, Dynamics and Forecast by End use, 2023-2030 |
21 | Product installation rate by OEM, 2023 |
22 | Incline/Decline in Average B-2-B selling price in past 5 years |
23 | Competition from substitute products |
24 | Gross margin and average profitability of suppliers |
25 | New product development in past 12 months |
26 | M&A in past 12 months |
27 | Growth strategy of leading players |
28 | Market share of vendors, 2023 |
29 | Company Profiles |
30 | Unmet needs and opportunity for new suppliers |
31 | Conclusion |
32 | Appendix |