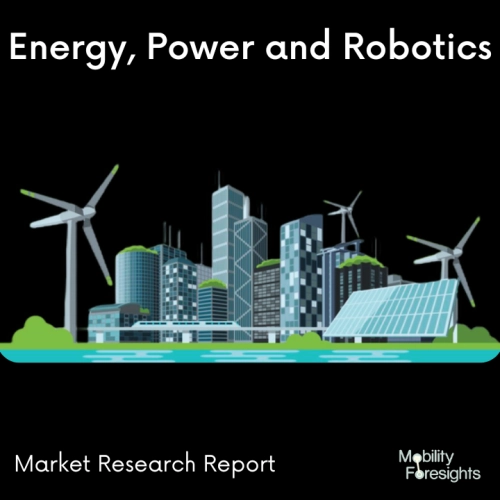
- Get in Touch with Us
Last Updated: Apr 25, 2025 | Study Period: 2024-2030
An internal combustion engine known as a jet engine produces thrust by jetting high-velocity exhaust gases in the opposite direction. Although it also finds usage in other processes like power generation and industrial processes, its main use is in airplane propulsion.
Modern aviation requires jet engines, which are well known for their high power-to-weight ratios. We shall look at the types, elements, and operating concepts of jet engines in this post.
The Newtonian concept of action and response serves as the foundation for a jet engine's operation. This idea holds that there is an equivalent and opposing reaction to every action. By accelerating a significant volume of air and expelling it at high speeds to generate forward force, jet engines take advantage of this principle.
The gas turbine is a jet engine's main structural element. The compressor, combustion chamber, and turbine make up the gas turbine. Incoming air is compressed by the compressor, which raises its pressure and temperature.
After the fuel and compressed air are combined and burnt in the combustion chamber, a high-pressure, high-temperature gas is produced. The compressor and other engine accessories are powered by the energy that this gas extracts as it expands and goes through the turbine. At high speeds, the exhaust gases are finally released, creating thrust.
A jet engine's compressor portion is in charge of compressing the incoming air. The air pressure is often gradually increased over a number of stages by rotating blades or airfoils. Some engines additionally have a fan, which is an additional part that is placed at the front and pulls in a lot of air. The efficiency of the engine is increased and additional thrust is provided by the fan.
The fuel and compressed air are combined and burned in the combustion chamber. Typically, a fine mist or spray of fuel is pumped into the combustion chamber. The gases' temperature and pressure are increased as a result of the enormous quantity of energy released during burning.
The combustion chamber is built to resist extreme temperatures, offer effective combustion, and maintain the engine's structural integrity.The compressor and other engine parts are powered by the energy that the turbine section extracts from the hot gases. It is made up of several turbine blades arranged on a shaft.
The turbine blades are rotated by the high-velocity gases that exit the combustion chamber. The compressor and any other engine-connected accessories, such as generators or hydraulic pumps, receive the turbine's rotation as well.
Depending on their design and use, jet engines can be divided into various categories. The turbojet, turbofan, turboprop, and turboshaft engine types are the most prevalent. Military aircraft that fly at high speeds employ turbojet engines, which work by accelerating all of the air passing past them.
Commercial airplanes frequently use turbofan engines, which have a sizable front fan that bypasses a sizable percentage of the air around the engine core to increase thrust and lessen noise. Smaller aircraft use turboprop engines, which have a propeller attached to the turbine to provide both jet thrust and propeller-driven propulsion.
Last but not least, helicopters employ turboshaft engines to drive a variety of systems, including rotors, hydraulic pumps, and electrical generators.In summary, a jet engine is an effective internal combustion device that produces thrust by releasing high-velocity exhaust gases.
It is made up of a turbine, a combustion chamber, and a compressor. Incoming air is compressed by the compressor, fuel, and air are burned in the combustion chamber, and energy is extracted by the turbine to power the compressor and other accessories.
Jet engines are essential to aviation, and there are several varieties designed for diverse tasks. They are essential for modern air travel because of their effectiveness, power-to-weight ratio, and capability to function at high altitudes.
The Global Jet Engine Market accounted for $XX Billion in 2023 and is anticipated to reach $XX Billion by 2030, registering a CAGR of XX% from 2024 to 2030.
Today, Rolls-Royce and easyJet announced that their first run of a modern aircraft engine on hydrogen had achieved a new aviation record. The ground test was performed using green hydrogen produced by wind and tidal power on an early concept demonstrator.
It is a crucial proof point in both Rolls-Royce and easyJet's decarbonization programs and represents a significant step toward demonstrating that hydrogen might be a zero-carbon aviation fuel in the future.
Both businesses have set out to demonstrate that hydrogen can produce power for civil aircraft engines in a safe and effective manner, and they are currently preparing for a second round of experiments with the longer-term goal of conducting flight tests.
The test was conducted with a modified Rolls-Royce AE 2100-A regional aircraft engine at the MoD Boscombe Down outdoor test facility in the UK. The green hydrogen used in the testing was provided by EMEC (European Marine Energy Centre), which produces it on Eday in the UK's Orkney Islands using renewable energy.
The alliance intends a series of additional rig tests after analysis of this preliminary concept ground test, culminating in a full-scale ground test of a Rolls-Royce Pearl 15 jet engine. The Race to Zero initiative, which both businesses have joined and which is supported by the UN and aims to achieve net zero carbon emissions by the year 2050, served as the inspiration for the alliance.
Sl no | Topic |
1 | Market Segmentation |
2 | Scope of the report |
3 | Abbreviations |
4 | Research Methodology |
5 | Executive Summary |
6 | Introduction |
7 | Insights from Industry stakeholders |
8 | Cost breakdown of Product by sub-components and average profit margin |
9 | Disruptive innovation in the Industry |
10 | Technology trends in the Industry |
11 | Consumer trends in the industry |
12 | Recent Production Milestones |
13 | Component Manufacturing in US, EU and China |
14 | COVID-19 impact on overall market |
15 | COVID-19 impact on Production of components |
16 | COVID-19 impact on Point of sale |
17 | Market Segmentation, Dynamics and Forecast by Geography, 2023-2030 |
18 | Market Segmentation, Dynamics and Forecast by Product Type, 2023-2030 |
19 | Market Segmentation, Dynamics and Forecast by Application, 2023-2030 |
20 | Market Segmentation, Dynamics and Forecast by End use, 2023-2030 |
21 | Product installation rate by OEM, 2023 |
22 | Incline/Decline in Average B-2-B selling price in past 5 years |
23 | Competition from substitute products |
24 | Gross margin and average profitability of suppliers |
25 | New product development in past 12 months |
26 | M&A in past 12 months |
27 | Growth strategy of leading players |
28 | Market share of vendors, 2023 |
29 | Company Profiles |
30 | Unmet needs and opportunity for new suppliers |
31 | Conclusion |
32 | Appendix |