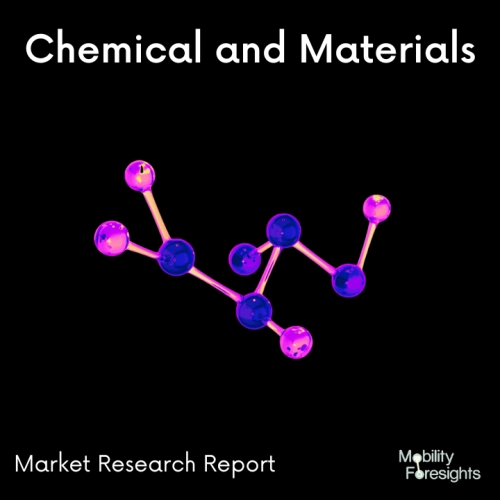
- Get in Touch with Us
Last Updated: Apr 25, 2025 | Study Period: 2024-2030
The chemical composition of the vacuum-melted iron-nickel-cobalt alloy Kovar is tightly regulated to ensure accurate, homogeneous thermal expansion qualities. Because of this, it is particularly well suited for applications that need a matched-expansion seal between metal and glass pieces. an alloy with the same heat expansion characteristics as heat-resistant glass that is mostly made of iron, nickel, and cobalt; it is typically fused to glass to create gas seals.
The Global Kovar Alloy Market accounted for $XX Billion in 2023 and is anticipated to reach $XX Billion by 2030, registering a CAGR of XX% from 2024 to 2030.
Machining Alloy 52 Kovar using different machining environments.In electronics and optoelectronics applications where hermetic seals are needed between metal and glass components, kovar is widely employed. Despite being used, little is known about Kovar's machinability. Anodic bonding is a technique that was created to firmly attach conductive materials like Kovar to glass.
By heating the samples at a low temperature, Kovar is joined to ion-containing glass using this technique. To improve the weldability of Kovar and borosilicate glass, the surface of Kovar pieces are frequently oxidised.
With this technique, metallic assemblages are used to protect electrical components like piezoelectric and microfluidic sensors.For the first time, the effect of the machining environment and the cutting tool rake angle on Kovar's mesoscale end milling operations is examined in this work.
In conditions involving flood, minimum quantity lubrication (MQL), and cryogenic machining, two cutting rake angles of 10° and 12° were assessed. The findings indicate that abrasive wear is the primary mechanism of tool wear while machining Kovar, and that utilising MQL, cutting tools with a 12° rake angle had the longest tool lives.In many industries where hermetic sealing between glass and metal components are necessary, the controlled expansion alloy kovar is used.
Although being extensively used in electronics, optoelectronics, and aerospace, this alloy cannot be machined. With the monitoring of tool wear, tool life, surface finish, and power consumption, a full factorial design of experiments based on the two variables of cutting tool rake angle and machining environment has been successfully performed.
Sl no | Topic |
1 | Market Segmentation |
2 | Scope of the report |
3 | Abbreviations |
4 | Research Methodology |
5 | Executive Summary |
6 | Introduction |
7 | Insights from Industry stakeholders |
8 | Cost breakdown of Product by sub-components and average profit margin |
9 | Disruptive innovation in the Industry |
10 | Technology trends in the Industry |
11 | Consumer trends in the industry |
12 | Recent Production Milestones |
13 | Component Manufacturing in US, EU and China |
14 | COVID-19 impact on overall market |
15 | COVID-19 impact on Production of components |
16 | COVID-19 impact on Point of sale |
17 | Market Segmentation, Dynamics and Forecast by Geography, 2024-2030 |
18 | Market Segmentation, Dynamics and Forecast by Product Type, 2024-2030 |
19 | Market Segmentation, Dynamics and Forecast by Application, 2024-2030 |
20 | Market Segmentation, Dynamics and Forecast by End use, 2024-2030 |
21 | Product installation rate by OEM, 2023 |
22 | Incline/Decline in Average B-2-B selling price in past 5 years |
23 | Competition from substitute products |
24 | Gross margin and average profitability of suppliers |
25 | New product development in past 12 months |
26 | M&A in past 12 months |
27 | Growth strategy of leading players |
28 | Market share of vendors, 2023 |
29 | Company Profiles |
30 | Unmet needs and opportunity for new suppliers |
31 | Conclusion |
32 | Appendix |