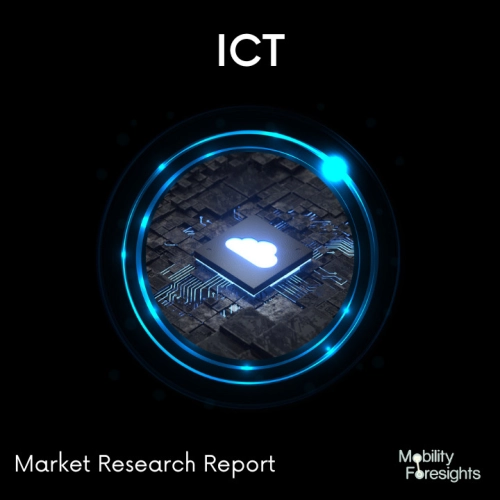
- Get in Touch with Us
Last Updated: Apr 25, 2025 | Study Period: 2023-2030
A camera sensor and Internet of Things (IoT) on near-real-time image analysis were used to design and test the landslide surveillance system.
Vision-based algorithms are applied to a monitored landslide using a low-cost Raspberry Pi computing unit and a camera serial port.
Additionally, there are a number of direct ways to stop landslides; modifying the geometry of the slope, utilizing chemical agents to reinforce the material on the slope, erecting structures like piles and retaining walls, grouting rock joints and fissures, redirecting pathways for debris, and rerouting surface and underwater drainage are some examples of these.
"The lead researcher of a "Smart Road Safety and Landslide Detection System" stated that ultrasonic sensors, water level sensors, vibration sensors, accelerometers, inclinometers, and rainfall sensors are examples of geotechnical instruments used in landslide monitoring.
Resources from agriculture and forests are lost; Heritage sites and infrastructure are damaged or destroyed.
Material from landslides can obstruct rivers and increase sedimentation in the downstream area, increasing the risk of flooding.
TheGlobal landslide prevention camera systemsaccounted for $XX Billion in 2022 and is anticipated to reach $XX Billion by 2030, registering a CAGR of XX% from 2023 to 2030.
UNTERSCHLEIÃHEIM, Germany Roads, buildings, and even passing vehicles can be severely damaged by large boulders carried by debris flow.
A tried-and-true method for dissipating the impact energy of boulders and a less expensive alternative to larger reinforced concrete structures is to construct a steel baffle on steep slopes.
However, the effectiveness of the steel baffle as a safety measure may be hindered by its current designs, footings, and structural connections.
New baffle designs have been subjected to full-scale pendulum impact tests by researchers at the Hong Kong University of Science and Technology1.
On cubic footings with side lengths of either 650 mm (2.13 feet) or 1300 mm (4.25 feet), a baffle was installed with or without steel dowels inserted at various depths in the ground.
Concrete boulders weighing nearly 4500 pounds were hoisted by cranes and dropped on the baffles, generating impact energy of up to 100 kilojoules, for the testing.
A Mikrotron MotionBLITZ mini GigE Vision monochrome camera was positioned on one side of a large test platform to record the impact of boulders on the various baffle designs.
Camera goal was set for 1280 Ã 1008 pixels at 300 casings each second, bringing about examination quality pictures much obliged, to some extent, to its rapid worldwide screen.
Deflection was measured by laser sensors positioned on the top and bottom of the baffles. A data logger was connected to the camera, laser sensors, and other instruments like an accelerometer and strain gauges.
Based on the data that was gathered, 3D finite element models were created using multi-physics software. After that, the 3D models were uploaded to a parametric study to see how different configurations changed when the boulders were hit with different energy levels, depending on how far uphill they were released.
Sl no | Topic |
1 | Market Segmentation |
2 | Scope of the report |
3 | Abbreviations |
4 | Research Methodology |
5 | Executive Summary |
6 | Introduction |
7 | Insights from Industry stakeholders |
8 | Cost breakdown of Product by sub-components and average profit margin |
9 | Disruptive innovation in the Industry |
10 | Technology trends in the Industry |
11 | Consumer trends in the industry |
12 | Recent Production Milestones |
13 | Component Manufacturing in US, EU and China |
14 | COVID-19 impact on overall market |
15 | COVID-19 impact on Production of components |
16 | COVID-19 impact on Point of sale |
17 | Market Segmentation, Dynamics and Forecast by Geography, 2022-2030 |
18 | Market Segmentation, Dynamics and Forecast by Product Type, 2022-2030 |
19 | Market Segmentation, Dynamics and Forecast by Application, 2022-2030 |
20 | Market Segmentation, Dynamics and Forecast by End use, 2022-2030 |
21 | Product installation rate by OEM, 2022 |
22 | Incline/Decline in Average B-2-B selling price in past 5 years |
23 | Competition from substitute products |
24 | Gross margin and average profitability of suppliers |
25 | New product development in past 12 months |
26 | M&A in past 12 months |
27 | Growth strategy of leading players |
28 | Market share of vendors, 2022 |
29 | Company Profiles |
30 | Unmet needs and opportunity for new suppliers |
31 | Conclusion |
32 | Appendix |