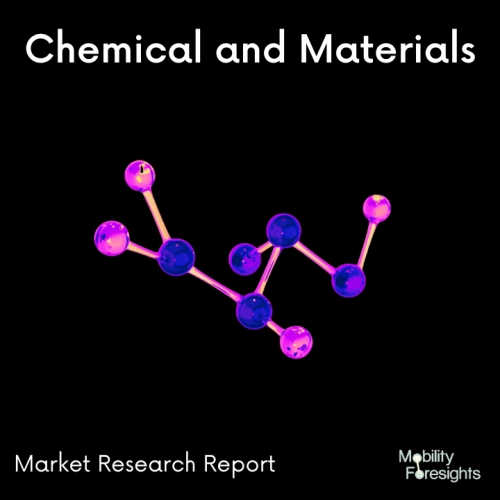
- Get in Touch with Us
Last Updated: Apr 25, 2025 | Study Period: 2023-2030
The removal of surface coating from base material is known as laser ablation. This technique works well for both coating application and removal. Although it can be utilised in compositions made of various materials, metal is a common example.
It is challenging to employ alternative techniques that wouldn't harm the base metal because the coatings are strong and thin.
Moreover, controlling the thickness of the removed layer is simpler using a laser. Moreover, it is possible to remove flexible designs without the need for masking or an additional step that adds a protective layer, as in chemical etching.
It is a direct procedure that requires no pre- or post-processing, making it affordable, practical, and time-saving.Here, two instances of laser ablations are highlighted.
Because of their low density, low coefficient of thermal expansion, high strength at high temperatures, and outstanding heat resistance, carbon composites are regarded as the most promising thermal structural materials for the automotive, nuclear energy, and aerospace industries.
The application of C/C composites in the oxygen-containing environments mentioned above is hampered by the oxidation of these materials, although this problem can be solved through coating preparation technology.
SiC is regarded as a suitable material to shield C/C composites from oxidation because of the low CTE, strong compatibility with C/C composites, and self-healing capacity brought by its oxide film.
In order to create SiC coating on C/C composites, pack cementation method is typically chosen due to the straightforward operation and established process. Nevertheless, a significant amount of molten Si seeps into the substrate through the pores of C/C composite as a result of prolonged heat treatment.
The mechanical strength of samples coated with SiC is adversely affected by the siliconization corrosion of the C/C substrate during the PC process, which severely restricts the practical applicability of this technology.
Due to a number of benefits, including precise positioning, adjustable coating thickness, a small heat-affected zone, and minimal substrate damage, laser cladding has gained a lot of interest as an antioxidant coating preparation method that is quickly growing.
Thus, in comparison to PC, LC approach is anticipated to enhance SiC coating preparation quality on C/C composites without degrading their mechanical properties. According to Wang et al., the SiC coating needed to be manufactured by LC using Si as the binder, and the Si-SiC coating was successfully produced.
The Global Laser-ablation-resistant coating market accounted for $XX Billion in 2022 and is anticipated to reach $XX Billion by 2030, registering a CAGR of XX% from 2023 to 2030.
The market leader in photonic printing solutions, DataLase, has launched a new line of functional Laser-ablation-resistant coatings for flexible packaging printers that are solvent-based. The innovation broadens the company's offering beyond flexographic printing to gravure printing applications and increases its engagement in the global high-growth flexible packaging market.
To generate high contrast, long-lasting, black-on-white codes over a variety of film and foil surfaces, the new solvent-based coatings, developed for use with CO2 lasers, offer an alternative to continuous inkjet and laser ablation. The DataLase method involves two steps.
The DataLase laser-reactive coating is first applied to a film or foil by the printer as a patch.To provide tamper-proof anti-counterfeit coding, this patch can either be surface printed or reverse printed beneath a barrier laminate layer.
This solution is especially well suited for the rigorous packaging requirements of the pharmaceutical industry. At the point in the manufacturing process where the variable data, such as expiration dates, lot codes, and/or 2D codes, is to be applied to the product, a CO2 laser is attached.
When exposed to the CO2 laser beam, the patch is activated, printing changeable data as needed to produce highly readable, machine-readable, tamper-proof codes that are perfect for applications requiring 100% product traceability.
Sl no | Topic |
1 | Market Segmentation |
2 | Scope of the report |
3 | Abbreviations |
4 | Research Methodology |
5 | Executive Summary |
6 | Introduction |
7 | Insights from Industry stakeholders |
8 | Cost breakdown of Product by sub-components and average profit margin |
9 | Disruptive innovation in the Industry |
10 | Technology trends in the Industry |
11 | Consumer trends in the industry |
12 | Recent Production Milestones |
13 | Component Manufacturing in US, EU and China |
14 | COVID-19 impact on overall market |
15 | COVID-19 impact on Production of components |
16 | COVID-19 impact on Point of sale |
17 | Market Segmentation, Dynamics and Forecast by Geography, 2023-2030 |
18 | Market Segmentation, Dynamics and Forecast by Product Type, 2023-2030 |
19 | Market Segmentation, Dynamics and Forecast by Application, 2023-2030 |
20 | Market Segmentation, Dynamics and Forecast by End use, 2023-2030 |
21 | Product installation rate by OEM, 2023 |
22 | Incline/Decline in Average B-2-B selling price in past 5 years |
23 | Competition from substitute products |
24 | Gross margin and average profitability of suppliers |
25 | New product development in past 12 months |
26 | M&A in past 12 months |
27 | Growth strategy of leading players |
28 | Market share of vendors, 2023 |
29 | Company Profiles |
30 | Unmet needs and opportunity for new suppliers |
31 | Conclusion |
32 | Appendix |