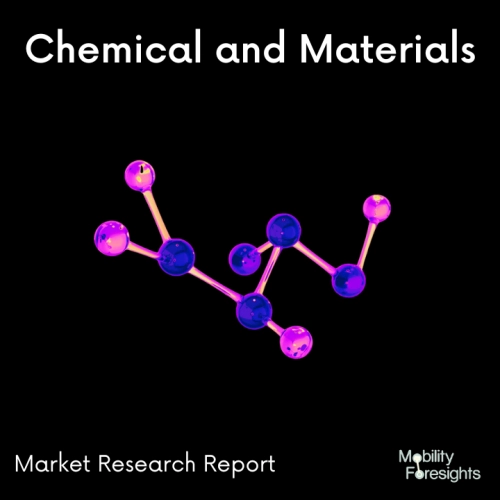
- Get in Touch with Us
Last Updated: Apr 25, 2025 | Study Period: 2024-2030
In the electronics industry, particularly in the power electronics sector, a brand-new application for laser micro welding is laser ribbon bonding. Ultrasonic welding is used in traditional ribbon bonding to secure the aluminum or copper ribbon to a conductive surface.
A new ribbon bonding technology is developed by modifying an ultrasonic ribbon bonder and equipping it with a fiber laser, a galvanometric scanner, and a beam focusing and delivery system. The "laser bonder" system design and test results for welding copper ribbons with a thickness of 300 m to DCB substrates are among the presented work.
Spatial power modulation is used for the laser welding of the ribbons, and the results on the welded ribbons are shown. The work concludes with the technology's benefits and drawbacks, particularly in relation to its applications in comparison to ultrasonic bonding.
The Global Laser Bonding Ribbons market accounted for $XX Billion in 2022 and is anticipated to reach $XX Billion by 2030, registering a CAGR of XX% from 2024 to 2030.
The F & K Delvotec Ultrasonic-Laserbonder reveals a brand-new technology. The brand-new method, which is based on laser micro-welding, is especially good for joining bonding wire to battery terminals, DCB substrates, and power electronics module copper terminals.
Ribbon bonding can be used at much higher currents thanks to ultrasonic-laser bonding. Ultrasonic-Laser bonding, which allows aluminum and copper wire to be bonded onto DCB substrates and copper terminals, not only expands the application area of bonding technology but is also more robust than conventional wire bonding. This makes electronic manufacturing simple and cost-effective.
Surface quality and cleaning procedures are less important now, and the need for completely immovable work pieces is no longer a barrier to zero-fault production.
When making batteries, this makes it possible to connect the terminals in a secure and adaptable way and eliminates the need to handle connector strips. Wire bonding's physical limit for carrying current in power electronics will eventually be reached. Laser welding, on the other hand, allows for the joining of virtually any thickness, but it is less flexible because it requires connectors that have already been manufactured.
Sl no | Topic |
1 | Market Segmentation |
2 | Scope of the report |
3 | Abbreviations |
4 | Research Methodology |
5 | Executive Summary |
6 | Introduction |
7 | Insights from Industry stakeholders |
8 | Cost breakdown of Product by sub-components and average profit margin |
9 | Disruptive innovation in the Industry |
10 | Technology trends in the Industry |
11 | Consumer trends in the industry |
12 | Recent Production Milestones |
13 | Component Manufacturing in US, EU and China |
14 | COVID-19 impact on overall market |
15 | COVID-19 impact on Production of components |
16 | COVID-19 impact on Point of sale |
17 | Market Segmentation, Dynamics and Forecast by Geography, 2024-2030 |
18 | Market Segmentation, Dynamics and Forecast by Product Type, 2024-2030 |
19 | Market Segmentation, Dynamics and Forecast by Application, 2024-2030 |
20 | Market Segmentation, Dynamics and Forecast by End use, 2024-2030 |
21 | Product installation rate by OEM, 2023 |
22 | Incline/Decline in Average B-2-B selling price in past 5 years |
23 | Competition from substitute products |
24 | Gross margin and average profitability of suppliers |
25 | New product development in past 12 months |
26 | M&A in past 12 months |
27 | Growth strategy of leading players |
28 | Market share of vendors, 2023 |
29 | Company Profiles |
30 | Unmet needs and opportunity for new suppliers |
31 | Conclusion |
32 | Appendix |