LASER DISPLACEMENT SENSORS MARKET
KEY FINDINGS
- The Global Laser Displacement Sensors Market is projected to experience robust growth from 2024 to 2030, driven by increasing demand across various industries including automotive, aerospace, and manufacturing.
- Technological advancements such as the integration of artificial intelligence and IoT capabilities into laser displacement sensors are anticipated to fuel market expansion during the forecast period.
- The market is expected to witness significant adoption of 3D laser displacement sensors, particularly in applications requiring precise measurement and inspection tasks.
- Rising automation in industries, coupled with the need for high-speed and accurate measurement solutions, is driving the demand for laser displacement sensors globally.
- Asia Pacific is poised to emerge as a lucrative market for laser displacement sensors, attributed to the region's flourishing manufacturing sector and increasing industrial automation.
- North America and Europe are expected to maintain substantial market shares, supported by the presence of prominent manufacturers and the adoption of advanced technologies.
- The automotive industry is anticipated to remain a key end-user segment for laser displacement sensors, primarily for applications such as quality control, robotic guidance, and autonomous vehicle development.
- Additionally, the growing use of laser displacement sensors in consumer electronics, healthcare, and robotics sectors is contributing to market growth.
- Challenges such as high initial investments and the availability of alternative technologies may hinder the market growth to some extent during the forecast period.
- However, ongoing research and development activities aimed at enhancing the performance and reducing the cost of laser displacement sensors are expected to create lucrative opportunities for market players in the coming years.
LASER DISPLACEMENT SENSORS MARKET OVERVIEW
- The Global Laser Displacement Sensor Market is anticipated for steady growth from 2024 to 2030, driven by several key factors.
- One major driver is the rising trend of industrial automation. These sensors play a crucial role in robots, assembly lines, and other automated systems, ensuring precise positioning and measurement.
- Another factor propelling the market is the increasing adoption of laser displacement sensors in consumer electronics. They are being used in smartphones for features like facial recognition and 3D cameras.
- The automotive industry is also embracing these sensors for applications like collision avoidance systems and automated assembly lines. This trend is expected to continue in the coming years.
- The growing demand for high-precision manufacturing across various industries is another factor driving the market. Laser displacement sensors offer exceptional accuracy, making them ideal for tasks requiring micrometre-level precision.
- However, the market does face some challenges. The high cost of these sensors compared to traditional methods might deter some potential users. Additionally, the limited measuring range of some sensors might restrict their applicability in certain situations.
- Despite these challenges, the market for laser displacement sensors is expected to witness significant growth due to the increasing demand for automation, precision manufacturing, and advanced consumer electronics.
- Advancements in laser technology are expected to further enhance the capabilities and functionalities of these sensors. This, in turn, could open doors for new applications across various industries.
- The Asia Pacific region is expected to hold a dominant position in the global laser displacement sensor market due to the presence of major manufacturing hubs and growing automation adoption in countries like China and India.
- The market is expected to witness a rise in strategic collaborations and mergers and acquisitions among key players to expand their product portfolios and gain a competitive edge.
- Overall, the future of the global laser displacement sensor market appears promising, with advancements in technology, increasing automation, and growing demand for high-precision measurement driving its growth.
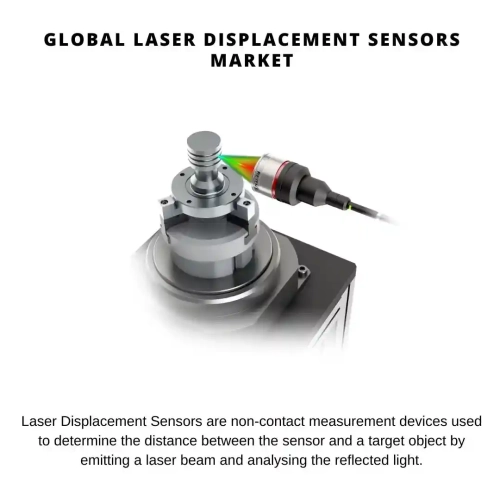
LASER DISPLACEMENT SENSORS MARKET INTRODUCTION
Laser Displacement Sensors are non-contact measurement devices used to determine the distance between the sensor and a target object by emitting a laser beam and analysing the reflected light. These sensors are highly precise and can measure distances with high accuracy, making them ideal for various industrial applications where precise measurements are crucial.
There are several types of laser displacement sensors, including triangulation-based sensors, time-of-flight sensors, and confocal sensors. Triangulation-based sensors calculate distance by measuring the angle of the reflected laser beam, while time-of-flight sensors determine distance based on the time taken for the laser pulse to travel to the target and back. Confocal sensors use a narrow wavelength band of light to measure distance with exceptional precision.
The benefits of laser displacement sensors include their high accuracy, fast measurement speed, non-contact operation, and suitability for measuring a wide range of surfaces, including shiny or transparent objects. However, there are also risks and challenges associated with their use, such as the potential for interference from external factors like ambient light or reflective surfaces, as well as the need for calibration and regular maintenance to ensure accurate measurements over time. Additionally, the initial investment cost for laser displacement sensors can be high, and integrating them into existing systems may require specialised expertise, posing challenges for some users.
LASER DISPLACEMENT SENSORS MARKET SIZE AND FORECAST
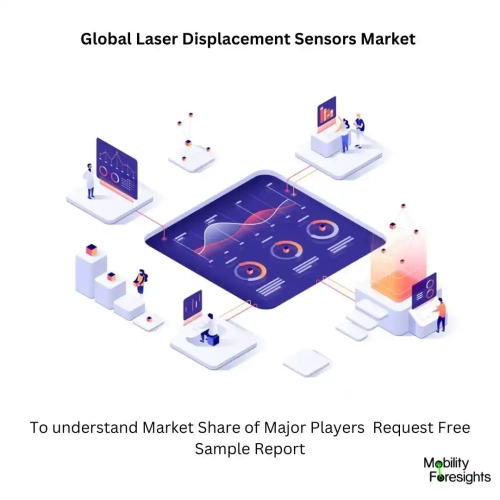
The Global Laser Displacement Sensors Market accounted for $XX Billion in 2023 and is anticipated to reach $XX Billion by 2030, registering a CAGR of XX% from 2024 to 2030.
LASER DISPLACEMENT SENSORS MARKET TRENDS
- Integration of AI and IoT: The market is witnessing a trend towards the integration of artificial intelligence (AI) and Internet of Things (IoT) capabilities into laser displacement sensors, enabling real-time data analysis and enhanced functionality. This integration allows for predictive maintenance, automated decision-making, and optimization of measurement processes, driving efficiency and reducing downtime.
- 3D Laser Displacement Sensors: There is a growing demand for 3D laser displacement sensors, fueled by the need for more comprehensive and precise measurement solutions across various industries. These sensors offer the ability to capture detailed spatial information, facilitating applications such as object recognition, volumetric measurement, and surface profiling with higher accuracy and efficiency.
- Miniaturization and Portability: Another emerging trend is the miniaturisation and portability of laser displacement sensors, catering to the requirements of mobile and compact applications. Miniaturised sensors enable integration into handheld devices, robotic arms, and drones, expanding their usability in fields such as construction, agriculture, and healthcare for tasks like structural inspection, crop monitoring, and patient positioning.
- Enhanced Sensing Technologies: Market players are investing in the development of advanced sensing technologies to improve the performance and capabilities of laser displacement sensors. Innovations such as multi-axis measurement, higher resolution, extended measurement ranges, and enhanced environmental robustness are being introduced to address diverse application needs and challenges, driving market growth.
- Application Expansion Beyond Traditional Industries: Laser displacement sensors are finding new applications beyond their traditional industries like automotive and manufacturing. Emerging sectors such as consumer electronics, healthcare, and robotics are increasingly adopting these sensors for tasks such as gesture recognition, medical imaging, and robot navigation, opening up new avenues for market expansion and innovation.
LASER DISPLACEMENT SENSORS MARKET NEW PRODUCT DEVELOPMENT
Keyence Corporationintroduced theLR-T Series of Laser Displacement Sensors. These sensors offer high-speed and accurate measurement capabilities, with a measurement range of up to 4 metres and a resolution as fine as 5 μm. The LR-T series features a compact and robust design, making it suitable for use in various industrial applications where space is limited or harsh operating conditions are present.
SICK AGintroduced theOD1000 Displacement Sensor. This sensor utilises time-of-flight technology to deliver precise distance measurements over long ranges, up to 1,000 metres. With a high measurement frequency and accuracy down to the micrometre range, the OD1000 sensor is ideal for applications such as crane positioning, warehouse automation, and outdoor distance monitoring.
OMRON Corporationintroduced theZW-7000 Series of Laser Displacement Sensors, designed to meet the demands of high-speed and high-precision measurement applications. These sensors feature a measurement range of up to 200 mm and boast a measurement frequency of 120 kHz, allowing for rapid data acquisition in dynamic environments. The ZW-7000 series incorporates OMRON's advanced technology for stable measurements, ensuring consistent performance even in the presence of vibrations or changing ambient conditions.
LASER DISPLACEMENT SENSORS MARKET SEGMENTATION
Laser Displacement Sensors Market By Geography
- USA
- Europe
- China
- Asia Excluding China
- ROW
Laser Displacement Sensors Market By Technology
Laser Displacement Sensors Market By Application
- Industrial Automation
- Consumer Electronics
- Automotive
- Others (e.g., Medical, Security)
Laser Displacement Sensors Market By Measurement Range
- Short Range
- Medium Range
- Long Range
KEY PLAYERS IN LASER DISPLACEMENT SENSORS MARKET
- Keyence Corporation
- SICK AG
- OMRON Corporation
- Panasonic Corporation
- Micro-Epsilon
- IFM Electronic GmbH
- Z-LASER Optoelektronik GmbH
- Banner Engineering Corp.
- Accretech (Tokyo Seimitsu Co., Ltd.)
- LMI Technologies Inc.
THIS LASER DISPLACEMENT SENSORS MARKET REPORT WILL ANSWER THE FOLLOWING QUESTIONS
- What are the primary factors driving the growth of the Laser Displacement Sensors Market from 2024 to 2030?
- How is the integration of artificial intelligence influencing the development of Laser Displacement Sensors Market?
- What are the key challenges faced by manufacturers in the global Laser Displacement Sensors Market?
- How do 3DLaser Displacement Sensors Market differ from traditional 1D sensors, and what are their advantages?
- What role do laser displacement sensors play in the automotive industry, and how is this market segment expected to evolve?
- How are advancements in miniaturization impacting the design and functionality of laser displacement sensors?
- What are the emerging applications of laser displacement sensors beyond traditional industries?
- How are laser displacement sensors contributing to the advancement of robotics and automation?
- What are the regional trends shaping the global laser displacement sensors market landscape?
- How do laser displacement sensors contribute to quality control and inspection processes in manufacturing?
- What are the potential risks associated with the widespread adoption of laser displacement sensors?
- How are market leaders differentiating their products to maintain a competitive edge in the industry?
- What are the implications of the growing demand for laser displacement sensors in the consumer electronics sector?
- How are regulations and standards influencing the development and deployment of laser displacement sensors?
- What role do laser displacement sensors play in ensuring the safety and reliability of autonomous vehicles?
- How are laser displacement sensors being integrated into smart manufacturing and Industry 4.0 initiatives?
- What are the cost implications of implementing laser displacement sensor technology in various industries?
- How do laser displacement sensors contribute to the optimization of supply chain and logistics operations?
- What are the key considerations for companies looking to invest in laser displacement sensor technology?
- How do laser displacement sensors compare to other non-contact measurement technologies in terms of accuracy and reliability?
- What are the potential environmental impacts associated with the production and disposal of laser displacement sensors?
- How are advancements in materials science influencing the development of laser displacement sensor components?
- What are the key trends in sensor fusion and data integration in the context of laser displacement sensors?
- How do laser displacement sensors contribute to the advancement of precision agriculture and environmental monitoring?
- What are the emerging opportunities for innovation and growth in the global laser displacement sensors market?
- How are advancements in laser technology influencing the performance and capabilities of laser displacement sensors?
- What are the key factors influencing the adoption of laser displacement sensors in the healthcare industry?
- How are market dynamics such as mergers, acquisitions, and partnerships shaping the competitive landscape of the industry?
- What are the potential implications of geopolitical factors on the global supply chain of laser displacement sensor components?
- How are manufacturers addressing concerns related to data privacy and cybersecurity in laser displacement sensor systems?