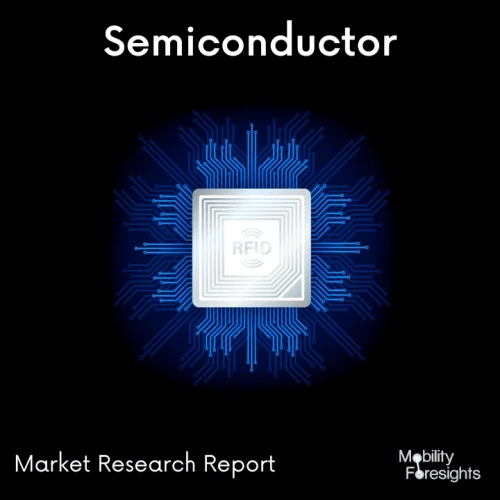
- Get in Touch with Us
Last Updated: Apr 25, 2025 | Study Period: 2024-2030
Laser distance sensors are advanced devices used to precisely measure distances to objects or surfaces by emitting a laser beam and analyzing the reflection of that beam. These sensors are highly accurate and are employed in a wide range of applications across industries such as manufacturing, construction, robotics, and more.
The laser distance sensors have a high ingress protection class, a small beam diameter, and an extremely high resolution. Direct mounting on movable machine parts like robotic arms is a good use for them.
The digital display and integrated electronic analysis circuitry make it simple to configure the sensor and quick to visualize the measured distances.The data is sent directly to a machine controller that is connected via three configurable switch outputs and two analog outputs.
The light propagation time principle underpins the operation of the laser distance sensors.They are used to position floor conveyors in high-bay warehouses, regulate speed, and prevent collisions in electric suspended railways due to their high reproducibility and precision.
With background suppression and a range of up to 10 meters, these sensors can also be used as light scanners.
S No | Company Name | Development |
---|---|---|
1 | Micro-Epsilon | With the addition of an integrated heating and cooling version that can operate in temperatures ranging from -40°C to +65°C, Micro-Epsilon has developed the popular optoNCDT ILR 2250-100 range of non-contact laser distance sensors. This enables the sensor to be used in permanent outdoor distance measurement applications. |
2 | Laser-View Technologies | Dimetix's laser distance sensors have been developed with new output features. Dimetix's master distributor, Laser-View Technologies, stocks, promotes, and offers support for the whole line of Dimetix laser distance sensors in the USA. Two digital outputs might previously have an on/off hysteresis encoded into them. |
3 | Ushio, Inc | New high-efficiency, low operating current laser diodes (LDs) from the HL65261MG series have been launched by Ushio, Inc. There are numerous industrial applications for laser distance sensors, ranging from more established ones in construction and civil engineering to newer ones in factory automation (FA) of production lines, logistics systems, and unmanned operations. |
For outdoor measurements over considerable distances, the optoNCDT ILR 2250-100-H laser distance sensor is the best option.
In addition to measuring properly on challenging surfaces like dark, complex, or weakly reflecting materials, the sensor measures distances up to 150m with an accuracy of 1mm. The sensor has a remarkable range up to 100m without any specific target adjustments. The range can be increased to 150 metres by adding a reflector to the target.
The most recent firmware version can deliver an output with a particular pulse width in either an ON or an OFF direction. Depending on factors like proximity, speed, signal strength, or temperature, each output can be set to activate.
As a result, the sensor is made more useful and programmable, and in some circumstances, it will be possible to use it without the assistance of external control processors.
Time of Flight (ToF) laser distance sensors in particular use an infrared or red laser as its light source to offer a long detection distance of many tens of metres together with high accuracy positioning capabilities.
To allow very accurate, long distance detection in ToF sensor applications, powerful pulsed light output is necessary. To make measurement devices that are more effective, there is also a need for increased LD efficiency and lower running current.
The Global Laser Distance Sensors market accounted for $XX Billion in 2022 and is anticipated to reach $XX Billion by 2030, registering a CAGR of XX% from 2024 to 2030.
Wintec has redefined the performance limits of photoelectronic sensors with the release of Wenglor Sensoric's most recent generation of long-range laser distance sensors.The integrated "Dynamic Sensitivity" (DS) technology has significantly improved the performance of the transit time sensors, which are available in plastic or stainless steel 316L housings.
In addition, the sensors combine all of the features of the well-known wintec series, which has revolutionized the automation industry since 2009.
The new Wintec features a working range of up to 10,000 mm, maximum reproducibility of 3 mm, and insensitivity to ambient light of up to 100,000 lux.
Process data can be written using the most recent IO-Link 1.1 standard and COM3, numerous status messages like temperature or light warnings can be called up, and even impact and shock loads can be recorded.Wintec offers innovative options for process monitoring in addition to optical performance.
With the highest level of accuracy and speed, LAT-52 laser distance sensors can quickly assess changes in distance as little as one millimetre. They are appropriate for precise proximity measurements in the 30 to 500 mm range and come in three different measuring ranges.
These measuring sensors are simple to set up and use across all applications thanks to their dual operating concept (operation through IO-Link or by keyboard) and eye-safe laser class 1. Quick commissioning and ideal measurement outcomes are provided by three preset sensor modes and adjustable filters. The LVHT-52 version is utilised when very accurate switching is of the utmost necessity.
These sensors have metal plugs and a sturdy metal casing (IP67). Large keys and LEDs make it simple to set them through IO-Link or on the sensor, and they are then immediately ready for use.
Measured data can be sent digitally and without loss via the IO-Link interface, diagnostic tasks can be easily carried out, identification and localization tasks can be realised, mean and median filters can be established, and relative measurements can be carried out.
Furthermore, IO-Link allows for the configuration of custom settings, as well as the saving and loading of masters. Because of this, replacing a gadget is particularly straightforward.
The user can virtually begin doing basic measuring activities by selecting one of three pre-set ready-to-run sensor modes: "Standard," "Power," or "Speed."
Sl no | Topic |
1 | Market Segmentation |
2 | Scope of the report |
3 | Abbreviations |
4 | Research Methodology |
5 | Executive Summary |
6 | Introduction |
7 | Insights from Industry stakeholders |
8 | Cost breakdown of Product by sub-components and average profit margin |
9 | Disruptive innovation in the Industry |
10 | Technology trends in the Industry |
11 | Consumer trends in the industry |
12 | Recent Production Milestones |
13 | Component Manufacturing in US, EU and China |
14 | COVID-19 impact on overall market |
15 | COVID-19 impact on Production of components |
16 | COVID-19 impact on Point of sale |
17 | Market Segmentation, Dynamics and Forecast by Geography, 2024-2030 |
18 | Market Segmentation, Dynamics and Forecast by Product Type, 2024-2030 |
19 | Market Segmentation, Dynamics and Forecast by Application, 2024-2030 |
20 | Market Segmentation, Dynamics and Forecast by End use, 2024-2030 |
21 | Product installation rate by OEM, 2023 |
22 | Incline/Decline in Average B-2-B selling price in past 5 years |
23 | Competition from substitute products |
24 | Gross margin and average profitability of suppliers |
25 | New product development in past 12 months |
26 | M&A in past 12 months |
27 | Growth strategy of leading players |
28 | Market share of vendors, 2023 |
29 | Company Profiles |
30 | Unmet needs and opportunity for new suppliers |
31 | Conclusion |
32 | Appendix |