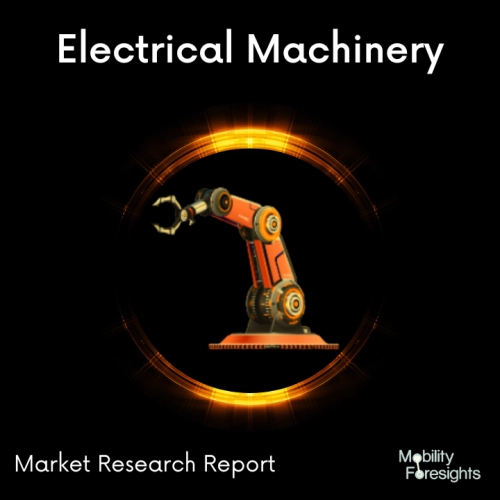
- Get in Touch with Us
Last Updated: Apr 25, 2025 | Study Period: 2023-2030
Laser-engineered net shaping (LENS) welds air-blown streams of metallic powders into unique components and production moulds over the course of hours.
The process yields geometries that are nearly identical to the finished product, negating the need for rough machining.
Small quantities of high-density components or moulds can be produced with LENS, among other things.Each of the nozzles points a jet of metal powder at a central location beneath them. A strong laser beam is simultaneously used to heat that location.
Another significant benefit of the LENS process is that production may be done on objects with uneven surfaces and without the requirement for a powder bed as the material is delivered to a construction area.
TheGlobal Laser Engineered Net Shaping (LENS) 3D Printer marketaccounted for $XX Billion in 2022 and is anticipated to reach $XX Billion by 2030, registering a CAGR of XX% from 2023 to 2030.
Optomec has introduced two new LENS (Laser Engineered Net Shaping) technology-based controlled atmosphere direct energy deposition (DED) devices.
The new reconfigurable LENS CS 600 and CS 800 Controlled Atmosphere (CA) DED Systems maximise the LENS process build envelope within a small machine footprint, and CA chambers enable processing of both non-reactive and reactive metals in an atmosphere that maintains moisture and oxygen levels at less than 10 ppm.
Based on LENS 3D printing technology, the devices employ high power lasers to produce fully dense objects in metal, ceramic, or composite materials. They can also be used to add metal to already-existing parts for repairs or coating applications.
The newly introduced systems are compatible with Optomec's most recent LENS deposition head generation, which offers even higher power laser processing, replaceable print nozzles, and adjustable spot sizes.
The linear three-axis motion system that comes with standard LENS systems can be expanded to a four- or five-axis system by adding a tilt-rotate trunnion or rotary table that users can swap out. Siemens' 840D controller, which enables fluid 3D printing from three axes up to simultaneous five axes motion, is included with the new CS 600 and 800 machines.
The Siemens motion controller uses industry-standard G&M codes and a straightforward push-button interface to operate the device. Material beginning recipes, closed loop process controls, thermal imaging, and five-axis tool path generating software will all be helpful to operators.
Sl no | Topic |
1 | Market Segmentation |
2 | Scope of the report |
3 | Abbreviations |
4 | Research Methodology |
5 | Executive Summary |
6 | Introduction |
7 | Insights from Industry stakeholders |
8 | Cost breakdown of Product by sub-components and average profit margin |
9 | Disruptive innovation in the Industry |
10 | Technology trends in the Industry |
11 | Consumer trends in the industry |
12 | Recent Production Milestones |
13 | Component Manufacturing in US, EU and China |
14 | COVID-19 impact on overall market |
15 | COVID-19 impact on Production of components |
16 | COVID-19 impact on Point of sale |
17 | Market Segmentation, Dynamics and Forecast by Geography, 2023-2030 |
18 | Market Segmentation, Dynamics and Forecast by Product Type, 2023-2030 |
19 | Market Segmentation, Dynamics and Forecast by Application, 2023-2030 |
20 | Market Segmentation, Dynamics and Forecast by End use, 2023-2030 |
21 | Product installation rate by OEM, 2023 |
22 | Incline/Decline in Average B-2-B selling price in past 5 years |
23 | Competition from substitute products |
24 | Gross margin and average profitability of suppliers |
25 | New product development in past 12 months |
26 | M&A in past 12 months |
27 | Growth strategy of leading players |
28 | Market share of vendors, 2023 |
29 | Company Profiles |
30 | Unmet needs and opportunity for new suppliers |
31 | Conclusion |
32 | Appendix |