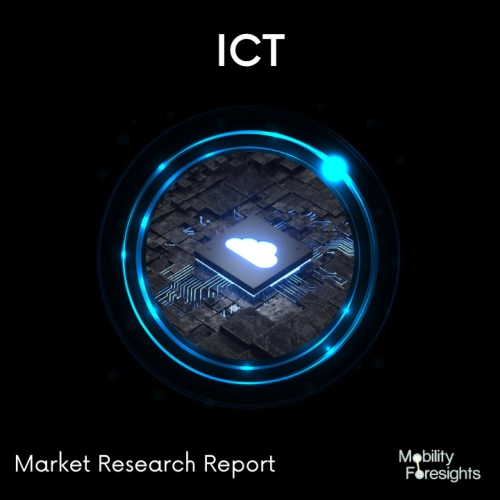
- Get in Touch with Us
Last Updated: Apr 25, 2025 | Study Period: 2023-2030
INTRODUCTION
In a laser heating process, energy is gained internally by the substrate material during the heating cycle and stored energy is released during the cooling cycle of the process.
Through carefully controlled heating and coolin
g, laser surface modification can alter the microstructure of metals. The ability to heat treat certain regions of the workpiece without harming the complete object is a benefit that lasers provide in this procedure.
Typically, a substance is heated by a laser by adding energy to it. This occurs because the energy of the light wave causes the target atoms to move more, raising the temperature of the material.
However, just as a laser can accelerate atomic motion and raise temperature in a material, it can also cause But just as a laser can raise the temperature of a material and speed up atomic motion, it can also reverse these effects.
GLOBAL LASER HEATING SYSTEM MARKET SIZE AND FORECAST
The Global Laser heating system market accounted for $XX Billion in 2022 and is anticipated to reach $XX Billion by 2030, registering a CAGR of XX% from 2023 to 2030.
NEW PRODUCT LAUNCH
New laser-heating systems are available from Hamamatsu Photonics. Five laser heating systems have been released by Hamamatsu Photonics. To enable consumers to choose the best laser-heating system for uses including laser soldering of microcomponents for smartphones, plastic welding of vehicle parts, and thermal curing of adhesives to connect incompatible materials, this new series features optimised laser output powers and spot diameters.
Laser thermal processing offers more efficiency at a lower environmental cost than traditional heating techniques, assisting in the reduction of carbon emissions for a more sustainable society.
The primary target market for these laser heating systems is domestic and international producers of electronic devices and automobile parts. The components of each of the five novel systems are a beam irradiation unit, a laser transmission optical fibre, and an LD irradiation light source.
All of them are created and put together to demonstrate the best performance for particular laser thermal processing applications and jobs.
Hamamatsu Photonics creates, develops, produces, and sells LD irradiation light sources for a variety of thermal processing tasks, such as laser soldering, plastic welding, thermal curing, drying, and hardening of adhesives.
The firm's optical design technique guarantees that the LD irradiation light sources output laser beams with consistent intensity distribution on the irradiated surface to enable high-quality processing without uneven or irregular heating.
The use of a single optical fibre for processing and measurement is another novel feature. This technique provides precise heat information at the laser irradiation site, enabling precise control of processing quality.
COMPANY PROFILE
THIS REPORT WILL ANSWER FOLLOWING QUESTIONS
Sl no | Topic |
1 | Market Segmentation |
2 | Scope of the report |
3 | Abbreviations |
4 | Research Methodology |
5 | Executive Summary |
6 | Introduction |
7 | Insights from Industry stakeholders |
8 | Cost breakdown of Product by sub-components and average profit margin |
9 | Disruptive innovation in the Industry |
10 | Technology trends in the Industry |
11 | Consumer trends in the industry |
12 | Recent Production Milestones |
13 | Component Manufacturing in US, EU and China |
14 | COVID-19 impact on overall market |
15 | COVID-19 impact on Production of components |
16 | COVID-19 impact on Point of sale |
17 | Market Segmentation, Dynamics and Forecast by Geography, 2023-2030 |
18 | Market Segmentation, Dynamics and Forecast by Product Type, 2023-2030 |
19 | Market Segmentation, Dynamics and Forecast by Application, 2023-2030 |
20 | Market Segmentation, Dynamics and Forecast by End use, 2023-2030 |
21 | Product installation rate by OEM, 2023 |
22 | Incline/Decline in Average B-2-B selling price in past 5 years |
23 | Competition from substitute products |
24 | Gross margin and average profitability of suppliers |
25 | New product development in past 12 months |
26 | M&A in past 12 months |
27 | Growth strategy of leading players |
28 | Market share of vendors, 2023 |
29 | Company Profiles |
30 | Unmet needs and opportunity for new suppliers |
31 | Conclusion |
32 | Appendix |