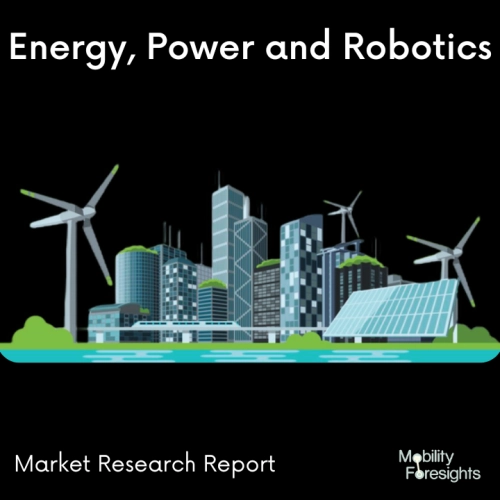
- Get in Touch with Us
Last Updated: Apr 25, 2025 | Study Period: 2023-2030
Gas metal arc welding, or GMAW, is combined with a laser beam in laser hybrid welding. The advantages of both instruments can then frequently be used to assist the welding process, such as deep penetration through the laser beam and gap bridging through the consumable added and melted by the electric arc process.
The growing number of process factors, which needs even more knowledge and expertise than the operations for a single heat source already do, is one drawback. Despite the fact that there have been several hybrid welding experiments over the past two decades, it is challenging to navigate to results in a methodical manner.
Because of the fundamental nature of data and information, this is a fundamental conundrum for laser processing and welding technologies.
The benefits of gas metal arc welding and laser keyhole welding are combined in laser arc hybrid welding, along with some of their more complicated physical workings. A map with many different functions was originally started from a variety of study outcomes, mostly experimental but also theoretical.
The goal is to assess the overall backdrop and to make it easier to navigate through the different phenomena that are demonstrated through case studies that are accompanied by theoretical justifications and optimization instructions. The map, while not entirely accurate, allows for methodical and graphical navigation to pertinent publications.
The map's core structure, which was determined early on, makes it naturally extensible in the future by adding both old and new knowledge, as well as knowledge from other research groups, enabling evolution.
The Global Laser hybrid navigation market accountedfor $XX Billion in 2021 and is anticipated to reach $XX Billion by 2030, registering a CAGR of XX% from 2022 to 2030.
Micro Air Vehicles (MAVs) are currently gaining a lot of popularity in a variety of applications. Due to their size and weight, they are reasonably priced and mobile.
MAVs can do autonomous flight by adding more sensors to them. MAVs can therefore autonomously investigate locations that are challenging for ground vehicles or pedestrians to reach. Examples of this include disaster zones, when the MAV supplies rescue personnel with information pertaining to their particular mission.
Such operations need to be carried out with a very precise navigational solution at all times. MAVs typically come with GNSS (Global Navigation Satellite System) receivers, which help the inertial navigation system by providing absolute position (INS).
As a result, additional sensors are needed, such as a camera and a laser rangefinder. Although these sensors don't give precise position data, they do make the navigation system more reliable and accurate.
Features are easily detected by the camera and tracked so that ego-motion may be seen. The absence of the para-factor is due to the following reasons..:: the unknown... metre. : the unknown to the The widely used visual odometry technique offers solutions to this issue.
One can utilise a stereo camera or an inertial measurement unit, for instance. Both approaches have limitations. For the IMU filter strategy to reduce the uncertainty of 3D points, camera viewpoint modification is required.
The stereo camera method's baseline constrains how accurate it can measure depth. Contrarily, laser rangefinders don't use triangulation to deliver precise depth information.
Sl no | Topic |
1 | Market Segmentation |
2 | Scope of the report |
3 | Abbreviations |
4 | Research Methodology |
5 | Executive Summary |
6 | Introduction |
7 | Insights from Industry stakeholders |
8 | Cost breakdown of Product by sub-components and average profit margin |
9 | Disruptive innovation in the Industry |
10 | Technology trends in the Industry |
11 | Consumer trends in the industry |
12 | Recent Production Milestones |
13 | Component Manufacturing in US, EU and China |
14 | COVID-19 impact on overall market |
15 | COVID-19 impact on Production of components |
16 | COVID-19 impact on Point of sale |
17 | Market Segmentation, Dynamics and Forecast by Geography, 2023-2030 |
18 | Market Segmentation, Dynamics and Forecast by Product Type, 2023-2030 |
19 | Market Segmentation, Dynamics and Forecast by Application, 2023-2030 |
20 | Market Segmentation, Dynamics and Forecast by End use, 2023-2030 |
21 | Product installation rate by OEM, 2023 |
22 | Incline/Decline in Average B-2-B selling price in past 5 years |
23 | Competition from substitute products |
24 | Gross margin and average profitability of suppliers |
25 | New product development in past 12 months |
26 | M&A in past 12 months |
27 | Growth strategy of leading players |
28 | Market share of vendors, 2023 |
29 | Company Profiles |
30 | Unmet needs and opportunity for new suppliers |
31 | Conclusion |
32 | Appendix |