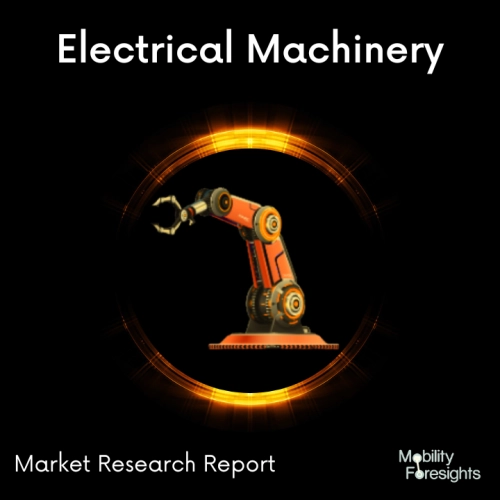
- Get in Touch with Us
Last Updated: Apr 25, 2025 | Study Period: 2023-2030
Laser peening creates a high-amplitude stress wave at the surface of a part using a high-energy pulsed laser. Compressive residual stresses are created by the stress wave in the component, preventing various metal fatigue signs.
Peening is the technique of shaping a metal's surface to enhance its material qualities, typically through mechanical methods like hammer blows, shot peening, or concentrating light (laser peening).
A high-energy, pulsed laser beam is used in the cold working process of laser peening to contact the surfaces of gear teeth, creating a compressive residual stress layer. It is a noncontact method as compared to mechanical shock peening.
Laser peening modifies the surface of a target material by using the dynamic mechanical effects of a shock wave generated by a laser. It doesn't make use of thermal phenomena. Essentially, a transparent overlay and a high energy, pulsed laser system are all that are needed to do laser peening.
TheGlobal Laser peening machine marketaccounted for $XX Billion in 2022 and is anticipated to reach $XX Billion by 2030, registering a CAGR of XX% from 2023 to 2030.
Quarter Century Development of Laser Peening without Coating.The idea was to induce compressive residual stresses (RSs) on the surface of vulnerable components in order to reduce stress corrosion cracking (SCC) of structural components in operational nuclear power reactors (NPRs).
Due to the radioactivity and submerged cooling of NPR components, full remote operation must be achieved utilising water-penetrable wavelength lasers without any surface preparation. Reduced pulse energy and pulse duration of less than 300 mJ and increased pulse density were used to create compressive RS on the top-surface (number of pulses irradiated on unit area).
LPwC has been used in NPRs with frequency-doubled Q-switched Nd:YAG lasers as preventative maintenance against SCC. In order to broaden the scope of application, fiber-delivery of powerful laser pulses was created concurrently and has been applied in NPRs.
Even though LPwC increased the components' surface roughness, the impact of extending fatigue life was still visible. It has been established that 10 to 20 mJ of pulse energy is sufficient to improve the fatigue characteristics of structural steel weld joints. In light of these developments, work on 20 mJ-class palmtop-sized handheld lasers began.
Sl no | Topic |
1 | Market Segmentation |
2 | Scope of the report |
3 | Abbreviations |
4 | Research Methodology |
5 | Executive Summary |
6 | Introduction |
7 | Insights from Industry stakeholders |
8 | Cost breakdown of Product by sub-components and average profit margin |
9 | Disruptive innovation in the Industry |
10 | Technology trends in the Industry |
11 | Consumer trends in the industry |
12 | Recent Production Milestones |
13 | Component Manufacturing in US, EU and China |
14 | COVID-19 impact on overall market |
15 | COVID-19 impact on Production of components |
16 | COVID-19 impact on Point of sale |
17 | Market Segmentation, Dynamics and Forecast by Geography, 2023-2030 |
18 | Market Segmentation, Dynamics and Forecast by Product Type, 2023-2030 |
19 | Market Segmentation, Dynamics and Forecast by Application, 2023-2030 |
20 | Market Segmentation, Dynamics and Forecast by End use, 2023-2030 |
21 | Product installation rate by OEM, 2023 |
22 | Incline/Decline in Average B-2-B selling price in past 5 years |
23 | Competition from substitute products |
24 | Gross margin and average profitability of suppliers |
25 | New product development in past 12 months |
26 | M&A in past 12 months |
27 | Growth strategy of leading players |
28 | Market share of vendors, 2023 |
29 | Company Profiles |
30 | Unmet needs and opportunity for new suppliers |
31 | Conclusion |
32 | Appendix |