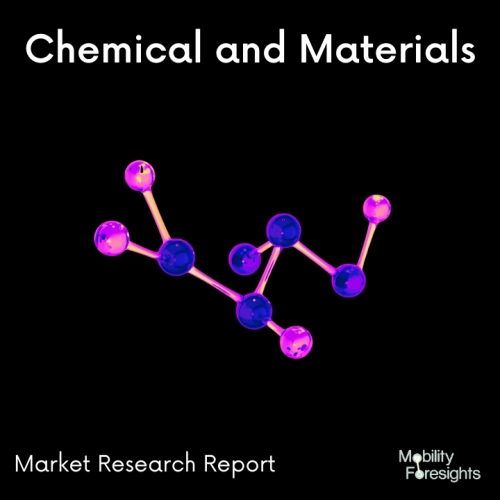
- Get in Touch with Us
Last Updated: Apr 25, 2025 | Study Period: 2024-2030
Two kinds of thermoplastics are joined together by transmission welding when welding plastics: The absorbing mating part is heated as the laser passes through the transparent mating part. The transparent joining area is melted by the absorbent plastic.
To ensure sufficient heat transfer, the mating parts must be pressed together using a suitable fixture. Here, the gap should be less than millimeters wide as much as possible. The melted plastic needs to completely solidify in order to guarantee a long-term connection.
As a result, after the actual welding process, the fixture continues to press the two mating parts together for a certain amount of time.
In many industries, laser-based plastics joining has many advantages over traditional methods like adhesive bonding and ultrasound or vibration welding.
The weld seam can be adapted to new component geometries when laser joining is used. For instance, delicate electronic components are effectively protected because the heat input is severely restricted locally.
There are typically four different types of laser welding for plastics: mask welding, contour welding, quasi-simultaneous welding, and simultaneous welding. Laser power is used for plastic welding.
Compared to adhesive bonding or vibration and ultrasound welding, no adhesive residues or plastic flakes are created when laser welding. Laser plastic welding is not just gentle for the material, but also for the environment.
The weld seams are of a consistently high quality. The strength of the seams produced corresponds to that of the base material.
The Global Laser plastic welding market accounted for $XX Billion in 2023 and is anticipated to reach $XX Billion by 2030, registering a CAGR of XX% from 2024 to 2030.
Evosys laser EvoWeld Mini plastic welding system -The EvoWeld Mini is Evosys Lasersâ newcomer among the complete systems of its EvoWeld series.
The device offers a coherent, ergonomic and economical overall concept and has been developed to realise laser plastic welding for smaller quantities â e.g. prototypes or assemblies with low quantities â or for laboratory operations.
The EvoWeld Mini is technically equipped to enable all standard industrial process variants, enhancing flexibility and making operation simpler.
The user-friendly EvoLaP software is used to program and modify welding contours, making it simple to transfer welding procedures developed on the EvoWeld Mini to more highly automated Evosys products. The welding system can be customized with a number of process and quality monitoring extensions.
At Fruit Logistica, Newtec has been showing off their brand-new LASER FLOWPACK700 laser welding equipment for ultra-thin film.
The resulting films are expected to be used, among other things, to package fruit and vegetable items. According to reports, the LASER FLOWPACK700 is economical and functions in accordance with the EU's plastic targets for the year 2025.
With a limited use of film and less consumption of plastics, Newtec claims that the machine "guarantees[s] a sustainable solution."
Additionally, it is said to integrate laser sealing and cutting into a single device to streamline and automate the manufacture of plastic films, as well as prevent the buildup of fused plastic on its welding jaws and eliminate the need to re-sharpen tools.
The system is also said to have a high production capacity of up to 80 punnets per minute, which may be altered to meet the requirements of the client.
The R3 thermoforming machine from MULTIVAC, which works with recyclable mono-material packaging films, was previously unveiled. The machine's modular architecture was intended to make it simple to operate, while simultaneously placing a high priority on preventing wrinkles in the film itself.
In addition, INSPIRA Box Motion, a vertical form fill seal bagmaker from Ishida Europe, aimed to offer snack producers a more affordable and adaptable operating process while also consuming 17% less energy while in use and 25% less while in standby.
Laser Plastic Welding (LPW) solutions are provided by IPTE, a provider of automated manufacturing machinery for the electronics and mechanical industries. Their methods offer a great deal of flexibility while improving the quality of the welding.
In recent years, the laser has replaced other welding techniques for plastics in a variety of industries. By creating a variety of tested LPW solutions, IPTE has responded to the growing demand from its clients.
Highest quality weld joints are ensured when LPW is used. Its fundamental working principle is the transmission of laser energy through a permeable top layer to an absorbent bottom layer.
The heat produced by the laser energy will cause the plastic components to melt. The end result, once the material has cooled, is a superior weld junction.
The following are just a few benefits of IPTE Laser Plastic Welding: Great precision and accuracy come after a superior weld connection.
The ergonomic design makes it simple for users to switch between various goods to weld. Consumables are not required, which means that maintenance is minimal and running costs are cheap. Both dust and vibrations are eliminated throughout the welding process.
The LPW solutions offered by the company can be used in a variety of manufacturing settings. The LPW systems, like all other production machinery supplied by IPTE, can be customised to meet unique customer needs.
Sl no | Topic |
1 | Market Segmentation |
2 | Scope of the report |
3 | Abbreviations |
4 | Research Methodology |
5 | Executive Summary |
6 | Introduction |
7 | Insights from Industry stakeholders |
8 | Cost breakdown of Product by sub-components and average profit margin |
9 | Disruptive innovation in the Industry |
10 | Technology trends in the Industry |
11 | Consumer trends in the industry |
12 | Recent Production Milestones |
13 | Component Manufacturing in US, EU and China |
14 | COVID-19 impact on overall market |
15 | COVID-19 impact on Production of components |
16 | COVID-19 impact on Point of sale |
17 | Market Segmentation, Dynamics and Forecast by Geography, 2024-2030 |
18 | Market Segmentation, Dynamics and Forecast by Product Type, 2024-2030 |
19 | Market Segmentation, Dynamics and Forecast by Application, 2024-2030 |
20 | Market Segmentation, Dynamics and Forecast by End use, 2024-2030 |
21 | Product installation rate by OEM, 2023 |
22 | Incline/Decline in Average B-2-B selling price in past 5 years |
23 | Competition from substitute products |
24 | Gross margin and average profitability of suppliers |
25 | New product development in past 12 months |
26 | M&A in past 12 months |
27 | Growth strategy of leading players |
28 | Market share of vendors, 2023 |
29 | Company Profiles |
30 | Unmet needs and opportunity for new suppliers |
31 | Conclusion |
32 | Appendix |