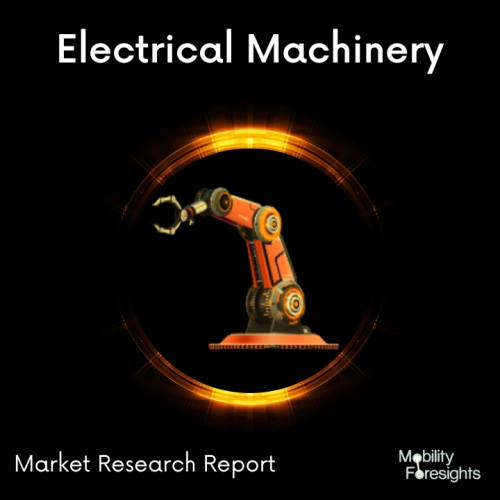
- Get in Touch with Us
Last Updated: Apr 25, 2025 | Study Period: 2024-2030
To describe measurement systems created to collect data with extremely high precision, the term "Laser-Radar" was adopted. Specifically focused light of a given wavelength or a combination of wavelengths is utilised for this.
LIDAR is a catch-all term for the majority of light-based metrology techniques. Depending on the system's design and application, typical devices may use laser beams, structured light mesh, or even pulsed white light. All are used to measure the location of the target points in a manner akin to radar.
By spinning along horizontal and vertical axes, the laser beam is guided. This gadget reads the return signal as previously said after sending a precise, focused laser pulse to an item. It does not require the use of a retroreflector, unlike laser tracking and other surveying tools.
The light reflected from the surface of the actual object serves as its signal. It is designed to deliver accurate industrial measurements with tolerances of tenths of a thousandth of an inch or even thousandths of an inch.
Global laser radar measuring system market accounted for $XX Billion in 2023 and is anticipated to reach $XX Billion by 2030, registering a CAGR of XX% from 2024 to 2030.
For producers looking to measure the geometry of medium-to-large parts, including everything from a vehicle door, casting, or fabrication to a whole car chassis or airframe structure, Nikon Industrial Metrology has unveiled a number of new metrology solutions.
As an alternative to conventionally sluggish and rigid panel machines and large-volume, horizontal-arm CMMs, APDIS Intelligent Quality (IQ) Stations provide a variety of Laser Radar options.
Major OEMs already utilise Nikon's non-contact Laser Radars on a global scale to measure thousands of items each day in metrology rooms and on shop floors.
Utilizing the MV430E Laser Radar's speed and data quality enhancements, Nikon has created completely automated measuring stations that are easy to instal, quick to programme, and quick to measure. Even when changing measurements or adding new parts, the use of a fixed set of positions removes the need for robot programming after installation.
The ability to define and replicate measurements off-line before physical setup makes it easier to analyse measurement programmes with just a few clicks.
Sl no | Topic |
1 | Market Segmentation |
2 | Scope of the report |
3 | Abbreviations |
4 | Research Methodology |
5 | Executive Summary |
6 | Introduction |
7 | Insights from Industry stakeholders |
8 | Cost breakdown of Product by sub-components and average profit margin |
9 | Disruptive innovation in the Industry |
10 | Technology trends in the Industry |
11 | Consumer trends in the industry |
12 | Recent Production Milestones |
13 | Component Manufacturing in US, EU and China |
14 | COVID-19 impact on overall market |
15 | COVID-19 impact on Production of components |
16 | COVID-19 impact on Point of sale |
17 | Market Segmentation, Dynamics and Forecast by Geography, 2024-2030 |
18 | Market Segmentation, Dynamics and Forecast by Product Type, 2024-2030 |
19 | Market Segmentation, Dynamics and Forecast by Application, 2024-2030 |
20 | Market Segmentation, Dynamics and Forecast by End use, 2024-2030 |
21 | Product installation rate by OEM, 2023 |
22 | Incline/Decline in Average B-2-B selling price in past 5 years |
23 | Competition from substitute products |
24 | Gross margin and average profitability of suppliers |
25 | New product development in past 12 months |
26 | M&A in past 12 months |
27 | Growth strategy of leading players |
28 | Market share of vendors, 2023 |
29 | Company Profiles |
30 | Unmet needs and opportunity for new suppliers |
31 | Conclusion |
32 | Appendix |