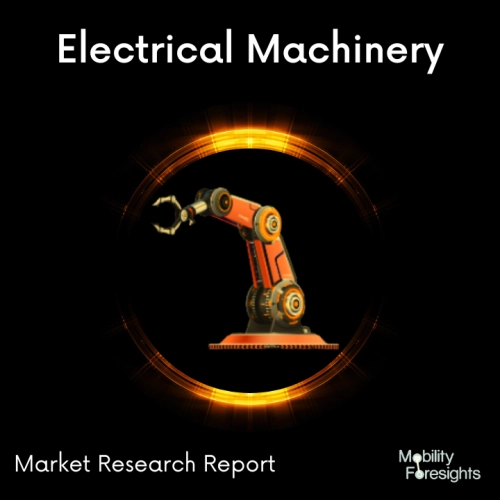
- Get in Touch with Us
Last Updated: Apr 25, 2025 | Study Period: 2024-2030
Laser welding produces a robust seam quickly by delivering a concentrated heat source. The automotive industry is where laser welding methods and applications are most prevalent since lasers increase productivity at a cheap cost when joining vehicle parts, such as roof, door, or filter assembly.
High-power fiber lasers that are continuous or even quasi-continuous that can be used for laser beam welding are used to create the welding process.
Laser welding will require light with a wavelength that is nearly infrared. The lasers are simple to manage, allowing you to alter their performance's resolution and pace.
Laser welding reduces the danger of contamination because it is significantly cleaner than traditional arc or Tig welding.
Additionally, it allows for the bonding of considerably thinner metals and offers far higher tensile and bending strength. It is also more precise and simpler to automate.
The laser beam melts the mated components along a shared joint in heat conduction welding. The weld is created when the molten components flow together and solidify.
Welding with heat conduction is used to unite pieces with thin walls. Corner welds on the surfaces of device housings that are visible are one illustration of this.
A manufacturing process known as laser welding, often referred to as laser beam welding (abbreviated "LBW"), involves using a laser beam to join two or more pieces of material, typically metal.
The Global Laser Welded Electrode Assembly market accounted for $XX Billion in 2023 and is anticipated to reach $XX Billion by 2030, registering a CAGR of XX% from 2024 to 2030.
A laser welding device for EV motors has been developed in collaboration with NITTOKU Co., Ltd. By combining the factory automation (FA) solutions of NITTOKU (which holds the top market share in the world for winding machines) and the laser welding copper material characterization technologies of Furukawa Electric, they hope to improve their customers' motor manufacturing processes (accelerate work, simplify processes, and stabilize quality).
A laser welding machine for electric vehicle motors is the new item. The integration of precision FA technologies from NITTOKU with laser processing technologies from Furukawa Electric (beam mode control and Blue-IR hybrid laser technologies) during the welding process can boost both quality and production.
In order to further enhance the performance of Furukawa Electric laser oscillators, NITTOKU will establish a production facility line that uses original control technology in addition to precision processing employing rectangular wire forming.
The process can be streamlined by using Furukawa Electric laser processing technologies, which enable motor welding to be done even when there is a height difference or space between rectangular wires.
Sl no | Topic |
1 | Market Segmentation |
2 | Scope of the report |
3 | Abbreviations |
4 | Research Methodology |
5 | Executive Summary |
6 | Introduction |
7 | Insights from Industry stakeholders |
8 | Cost breakdown of Product by sub-components and average profit margin |
9 | Disruptive innovation in the Industry |
10 | Technology trends in the Industry |
11 | Consumer trends in the industry |
12 | Recent Production Milestones |
13 | Component Manufacturing in US, EU and China |
14 | COVID-19 impact on overall market |
15 | COVID-19 impact on Production of components |
16 | COVID-19 impact on Point of sale |
17 | Market Segmentation, Dynamics and Forecast by Geography, 2024-2030 |
18 | Market Segmentation, Dynamics and Forecast by Product Type, 2024-2030 |
19 | Market Segmentation, Dynamics and Forecast by Application, 2024-2030 |
20 | Market Segmentation, Dynamics and Forecast by End use, 2024-2030 |
21 | Product installation rate by OEM, 2023 |
22 | Incline/Decline in Average B-2-B selling price in past 5 years |
23 | Competition from substitute products |
24 | Gross margin and average profitability of suppliers |
25 | New product development in past 12 months |
26 | M&A in past 12 months |
27 | Growth strategy of leading players |
28 | Market share of vendors, 2023 |
29 | Company Profiles |
30 | Unmet needs and opportunity for new suppliers |
31 | Conclusion |
32 | Appendix |