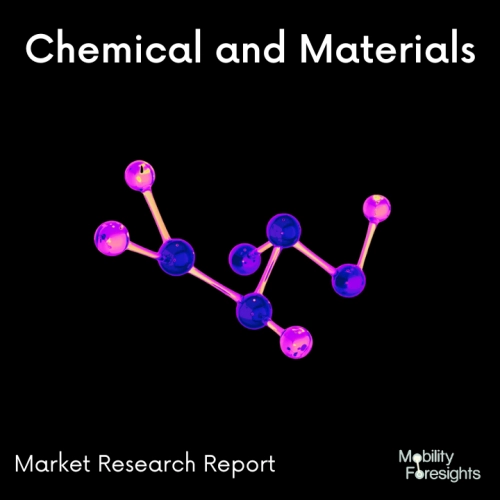
- Get in Touch with Us
Last Updated: Apr 25, 2025 | Study Period: 2023-2030
Liquid crystal displays (LCDs) are assembled using an adhesive resin called LCD sealant resin, often referred to as LCD optical adhesive or LCD bonding glue. It is used to join together different LCD panel layers and parts, ensuring structural integrity, protection, and optical improvement. The LCD sealant resin has the following salient features:Optically Clear: The formulation of LCD sealant resin provides high optical clarity and transparency.
It is made to reduce light absorption, refraction, and scattering in order to preserve the display's image quality.Bonding and Adhesion: The main purpose of LCD sealant resin is to affix the various LCD panel layers and parts together.
The glass substrate, polarizing and retardation films, color filters, electrodes, and other optical layers are all bonded during this process. The adhesive offers powerful adhesion, ensuring that the layers remain securely bonded throughout use and handling of the LCD screen.
Mechanical Stability: The LCD panel's endurance and mechanical stability are improved by the LCD sealant resin. It ensures structural integrity and prevents the layers from separating or delaminating.
The resin aids in shielding the fragile parts from moisture, dirt, and other impurities.Optical Enhancement: LCD sealant adhesive may also possess optical qualities that raise the display's general performance.
For instance, it might be designed to have a particular refractive index to lessen reflection and glare, enhancing the contrast and visibility of the display.UV Curing: Ultraviolet light is frequently used to cure LCD sealant glue. UV-curable resins have quick curing times and allow for fine production process control.
The Global LCD sealant resin market accounted for $XX Billion in 2022 and is anticipated to reach $XX Billion by 2030, registering a CAGR of XX% from 2023 to 2030.
Robnor launched PX628D LCD sealant resin has excellent strength and adhesion to a variety of substrates, including plastics, copper, brass, aluminum, and stainless steel. It can cover gaps because it is an epoxy paste glue that doesn't slump.
Stainless steel is a high-performing material with an MPa of 26.At room temperature, PX628D has a handling time of 6 to 8 hours and takes 48 hours to attain full potency.Its easy 1:1 by volume mix ratio makes it possible to meter and mix the glue in bulk.
Since the combined PX628D is grey in color, it is simple to verify that the white hardener and the black resin component have mixed together properly.PX628D is available in bulk or in 50, 200, and 400 ml cartridges and complies with WEEE, RoHS, and REACH regulations. Upon request, other sizes are offered.
1 | Market Segmentation |
2 | Scope of the report |
3 | Abbreviations |
4 | Research Methodology |
5 | Executive Summary |
6 | Introduction |
7 | Insights from Industry stakeholders |
8 | Cost breakdown of Product by sub-components and average profit margin |
9 | Disruptive innovation in the Industry |
10 | Technology trends in the Industry |
11 | Consumer trends in the industry |
12 | Recent Production Milestones |
13 | Component Manufacturing in US, EU and China |
14 | COVID-19 impact on overall market |
15 | COVID-19 impact on Production of components |
16 | COVID-19 impact on Point of sale |
17 | Market Segmentation, Dynamics and Forecast by Geography, 2023-2030 |
18 | Market Segmentation, Dynamics and Forecast by Product Type, 2023-2030 |
19 | Market Segmentation, Dynamics and Forecast by Application, 2023-2030 |
20 | Market Segmentation, Dynamics and Forecast by End use, 2023-2030 |
21 | Product installation rate by OEM, 2023 |
22 | Incline/Decline in Average B-2-B selling price in past 5 years |
23 | Competition from substitute products |
24 | Gross margin and average profitability of suppliers |
25 | New product development in past 12 months |
26 | M&A in past 12 months |
27 | Growth strategy of leading players |
28 | Market share of vendors, 2023 |
29 | Company Profiles |
30 | Unmet needs and opportunity for new suppliers |
31 | Conclusion |
32 | Appendix |