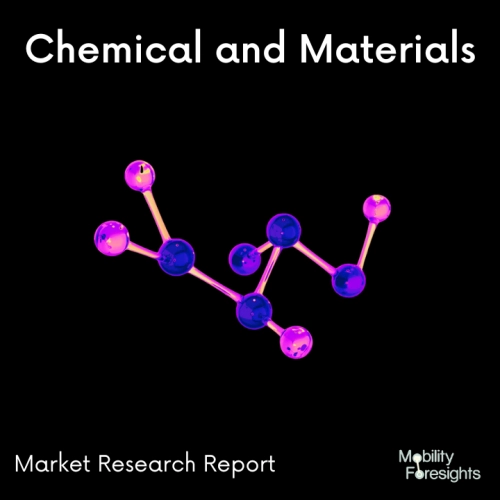
- Get in Touch with Us
Last Updated: Apr 25, 2025 | Study Period: 2024-2030
As their curing temperature is far below soldering temperature, conductive adhesives are the ideal material for establishing electrical contacts on substrates that are sensitive to temperature.
The adhesives are also a lot more flexible than solder, making them better equipped to endure vibrations. Electronics assembly is where conductive adhesives are most frequently employed.
These adhesives offer better reliability in electronic systems and are perfect for thermal and structural bonding applications as well as electrical connectivity.
The Global LED Conductive Adhesives market accounted for $XX Billion in 2023 and is anticipated to reach $XX Billion by 2030, registering a CAGR of XX% from 2024 to 2030.
New Conductive Adhesive for LED Lighting Applications is Launched by Creative Materials. The 125-35C, Syringe-dispensable Thermally Conductive Epoxy Adhesive is part of a line of goods that Creative Materials has created specifically for LED lighting applications.
These products, designed for use in the production of LEDs, work incredibly well as a heat-transfer medium between heat-producing parts and heat-sinks.
A prominent illustration of the necessity for efficient heat management is the growing market for high power light emitting diodes (LEDs).
Since LEDs are rapidly displacing more conventional lighting technologies, heat removal in LEDs has become a critical topic of R&D. To maintain optimal performance, the heat produced by LEDs must be dissipated.
One of their best-selling items is their well respected 109-12, which has a long history of success in LED lighting applications and many of the same features as 125-35C.
Due to its exceptional performance and high thermal conductivity, this product is incredibly adaptable in situations where large-area bond lines are required.
Furthermore, it has low viscosity, which permits application of a little amount of product while maintaining low heat resistance by reducing air entrapment in the component interface.
The low-stress epoxy 109-12 has a thermal conductivity of 5.65 W/mK and a maximum operating temperature of 220 °C. It has an extraordinary resistance to thermal cycling.Due to 109-12's compliance, brittle solder failure is avoided in applications where solder replacement is necessary.
Sl no | Topic |
1 | Market Segmentation |
2 | Scope of the report |
3 | Abbreviations |
4 | Research Methodology |
5 | Executive Summary |
6 | Introduction |
7 | Insights from Industry stakeholders |
8 | Cost breakdown of Product by sub-components and average profit margin |
9 | Disruptive innovation in the Industry |
10 | Technology trends in the Industry |
11 | Consumer trends in the industry |
12 | Recent Production Milestones |
13 | Component Manufacturing in US, EU and China |
14 | COVID-19 impact on overall market |
15 | COVID-19 impact on Production of components |
16 | COVID-19 impact on Point of sale |
17 | Market Segmentation, Dynamics and Forecast by Geography, 2024-2030 |
18 | Market Segmentation, Dynamics and Forecast by Product Type, 2024-2030 |
19 | Market Segmentation, Dynamics and Forecast by Application, 2024-2030 |
20 | Market Segmentation, Dynamics and Forecast by End use, 2024-2030 |
21 | Product installation rate by OEM, 2023 |
22 | Incline/Decline in Average B-2-B selling price in past 5 years |
23 | Competition from substitute products |
24 | Gross margin and average profitability of suppliers |
25 | New product development in past 12 months |
26 | M&A in past 12 months |
27 | Growth strategy of leading players |
28 | Market share of vendors, 2023 |
29 | Company Profiles |
30 | Unmet needs and opportunity for new suppliers |
31 | Conclusion |
32 | Appendix |