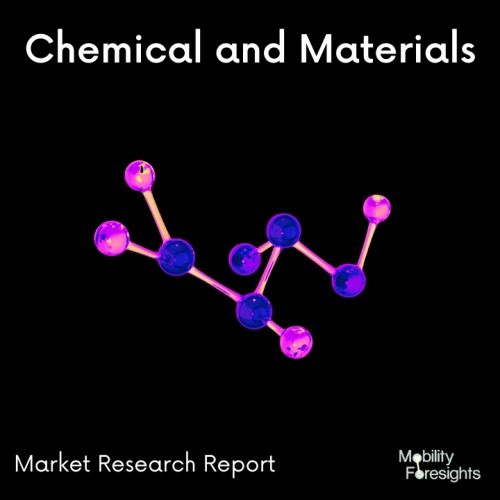
- Get in Touch with Us
Last Updated: Apr 25, 2025 | Study Period: 2024-2030
Lithium manganese oxide, also known as lithium manganate, or spinel lithium manganese oxide (LiMn2O4, LMO), is a dark to black powder that is used as a cathode material for LiMn2O4 Cathode Powder lithium-ion batteries.
It is popular due to its high thermal stability, good cycle performance, and the plentiful supply of manganese raw material. In contrast to the LiMn1.5Ni0.5O4 5V LiMn2O4 Cathode Powder, the voltage plateau of LMO is about 4.0V vs. Lithium.
The Global LiMn2O4 Cathode Powder market accounted for $XX Billion in 2023 and is anticipated to reach $XX Billion by 2030, registering a CAGR of XX% from 2024 to 2030.
Spinel LiMn2O4 Cathode Powder has been used in lithium-ion batteries for a very long time, both commercially and academically. Nowadays, electrolytic manganese dioxide (EMD) precursors are used to create the majority of commercial spinel LiMn2O4 Cathode Powder electrodes.
However, employing the cheap and readily available pyrolusite (-MnO2) described in this work has significant benefits. Micro rod-like lithium impregnated powders were produced via the solid-state process used to create spinel LiMn2O4 Cathode Powder from -MnO2 precursors, which was then followed by thermal calcination under air.
Analyzing these active materials' electrochemical behavior after Li-ion intercalation revealed a 95 mAh g-1 initial specific discharge capacity. The synthesized cathode material was able to cycle at high speeds (up to 9C), maintaining half of its initial discharge capacity and only experiencing a total loss of 7% of capacity.
Using glycine as the fuel and metal nitrates as the oxidizers, a simple solution combustion synthesis was used to create spinel-type LiMn2O4 Cathode powders as cathode materials for lithium ion batteries (LIBs). SCS was used to successfully manufacture single phases of LiMn2O4 Cathode Powder products, followed by a calcination process at 600 to 1000 oC.
Through the use of X-ray diffraction, scanning electron microscopy, and transmission electron microscopy, the powders' structure and morphology were carefully examined.
By using cyclic voltammetry and galvanostatic charge-discharge cycling, the electrochemical characteristics were identified. The calcination temperature had a significant impact on the products' size, morphology, and crystallinity. The material was calcined at 900 oC, and the particle sizes ranged from 500 to 1000 nm. It performed at its peak when the initial discharge capacity was used.
Sl no | Topic |
1 | Market Segmentation |
2 | Scope of the report |
3 | Abbreviations |
4 | Research Methodology |
5 | Executive Summary |
6 | Introduction |
7 | Insights from Industry stakeholders |
8 | Cost breakdown of Product by sub-components and average profit margin |
9 | Disruptive innovation in the Industry |
10 | Technology trends in the Industry |
11 | Consumer trends in the industry |
12 | Recent Production Milestones |
13 | Component Manufacturing in US, EU and China |
14 | COVID-19 impact on overall market |
15 | COVID-19 impact on Production of components |
16 | COVID-19 impact on Point of sale |
17 | Market Segmentation, Dynamics and Forecast by Geography, 2024-2030 |
18 | Market Segmentation, Dynamics and Forecast by Product Type, 2024-2030 |
19 | Market Segmentation, Dynamics and Forecast by Application, 2024-2030 |
20 | Market Segmentation, Dynamics and Forecast by End use, 2024-2030 |
21 | Product installation rate by OEM, 2023 |
22 | Incline/Decline in Average B-2-B selling price in past 5 years |
23 | Competition from substitute products |
24 | Gross margin and average profitability of suppliers |
25 | New product development in past 12 months |
26 | M&A in past 12 months |
27 | Growth strategy of leading players |
28 | Market share of vendors, 2023 |
29 | Company Profiles |
30 | Unmet needs and opportunity for new suppliers |
31 | Conclusion |
32 | Appendix |