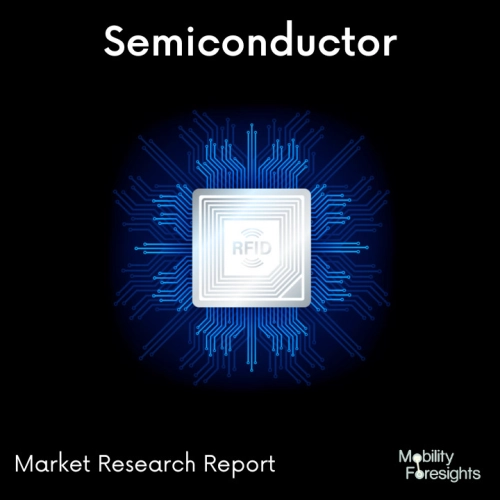
- Get in Touch with Us
Last Updated: Apr 25, 2025 | Study Period: 2024-2030
A linear encoder is a sensor, transducer, or redhead that is connected to a scale to encode position. The sensor scans the scale to transform the encoded position into an analogue or digital signal, which a digital readout (DRO) or motion controller may subsequently decode into position.
The encoder might be incremental or absolute in nature. In an incremental system, motion over time determines position; in an absolute system, position over time determines motion. Technologies for linear encoders include optical, magnetic, inductive, capacitive, and eddy current.
Shadow, self imaging, and interferometric technologies are examples of optical technologies. Metrology equipment, motion systems, inkjet printers, and high precision machining tools such as digital calipers and coordinate measuring machines all employ linear encoders.
The high resolution industry is dominated by optical linear encoders, which can use shuttering/moiré, diffraction, or holographic principles. Optical encoders are the most precise and widely utilized of the main types of encoders in industrial automation applications.
When specifying an optical encoder, it is critical that extra protection be built in to avoid contamination from dust, vibration, and other industrial environment conditions. Typical incremental scale durations range from hundreds to sub-micrometers. Interpolation can achieve nanometer-level resolution.
Magnetic linear encoders can be active (magnetized) or passive (variable reluctance), and position can be measured via sense-coils, Hall effect, or magnetoresistive redheads. Sine and cosine quadrature signals are the industry standard analogue output for linear encoders.
Typically, they are broadcast differently to increase noise protection. Peak-to-peak current signals were an early industry standard, but they have since been supplanted with peak-to-peak voltage signals. The reduced bandwidth of analogue transmissions helps to reduce EMC emissions as compared to digital transmission.
A linear incremental encoder generates quadrature squarewaves via two digital output signals, A and B. An encoder may generate A and B directly from sensors that are inherently digital in nature, or it may interpolate its own, analogue sine/cosine signals, depending on its internal mechanism.
The interpolation method effectively subdivides the scale period in the latter scenario, resulting in improved measurement resolution.
The Global Linear Encoders Market accounted for $XX Billion in 2023 and is anticipated to reach $XX Billion by 2030, registering a CAGR of XX% from 2024 to 2030.
SICK has introduced a new linear encoder product family for high-precision detection of piston locations in hydraulic cylinders and machine monitoring. The DAX linear encoder product family offers versatility for a wide range of industrial applications.
To fit various applications, the product family includes three designs, each with industry-appropriate measurement ranges. An Online Configurator guides customers through the process of picking an appropriate DAX. The product family's smart and flexible system design enables for personalized and efficient adaptation for applications with particular needs.
Based on magnetostriction, the sensing of a linear location is contactless and hence wear and maintenance free. This exact measuring approach guarantees maximum machine availability with no need for reference runs.
Furthermore, DAX linear encoders provide full diagnostic functionality. This enables the sensors to be used for condition monitoring and integration into digital transformation settings.
The DAX linear encoder may be used to measure locations in a variety of applications, such as injection molding machines, presses, automotive machinery, printing and packaging machines, wind, hydro, and solar facilities, wood processing, and medical technology.
SICK has expanded its offering of magnetostrictive linear encoders for industrial applications with the DAX product family. There is no need for a reference run because the gadget operates on an absolute measurement premise.
For the DAX's market introduction, three housing options are available: a design for integration into industrial hydraulic cylinders, a flat type with block magnets for mounting in tight installation situations.
The DAX platform idea provides significant system flexibility, allowing highly quick generation of application-specific versions and easy integration of the device into a wide range of machine concepts. This applies not only to the housing designs, but also to the position magnets, which may be customized to meet the needs of the application.
This backward compatibility gives the consumer greater options and freedom when selecting an encoder and manufacturer.The DAX product family's magnetostrictive capability employs a very precise and dependable time-of-flight (ToF) measuring mechanism.
This non-contact and wear-free working philosophy removes nearly all maintenance during operation while also providing a long service life.
Sl no | Topic |
1 | Market Segmentation |
2 | Scope of the report |
3 | Abbreviations |
4 | Research Methodology |
5 | Executive Summary |
6 | Introduction |
7 | Insights from Industry stakeholders |
8 | Cost breakdown of Product by sub-components and average profit margin |
9 | Disruptive innovation in the Industry |
10 | Technology trends in the Industry |
11 | Consumer trends in the industry |
12 | Recent Production Milestones |
13 | Component Manufacturing in US, EU and China |
14 | COVID-19 impact on overall market |
15 | COVID-19 impact on Production of components |
16 | COVID-19 impact on Point of sale |
17 | Market Segmentation, Dynamics and Forecast by Geography, 2024-2030 |
18 | Market Segmentation, Dynamics and Forecast by Product Type, 2024-2030 |
19 | Market Segmentation, Dynamics and Forecast by Application, 2024-2030 |
20 | Market Segmentation, Dynamics and Forecast by End use, 2024-2030 |
21 | Product installation rate by OEM, 2023 |
22 | Incline/Decline in Average B-2-B selling price in past 5 years |
23 | Competition from substitute products |
24 | Gross margin and average profitability of suppliers |
25 | New product development in past 12 months |
26 | M&A in past 12 months |
27 | Growth strategy of leading players |
28 | Market share of vendors, 2023 |
29 | Company Profiles |
30 | Unmet needs and opportunity for new suppliers |
31 | Conclusion |
32 | Appendix |