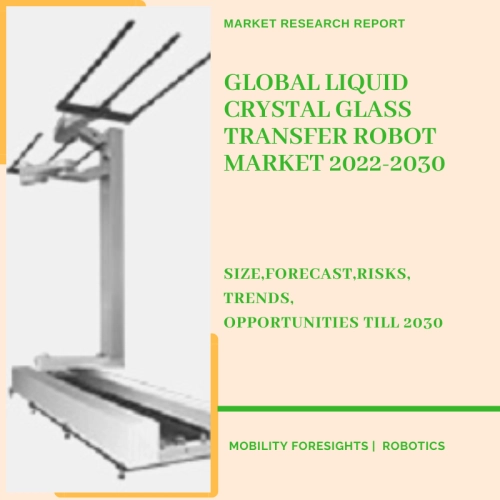
- Get in Touch with Us
Last Updated: Apr 25, 2025 | Study Period: 2022-2030
The mechanical compliance, adaptability, and high power-to-weight ratio of artificial muscles made of stimuli-responsive polymers often make them very promising replacements for conventional rigid motors in future soft robots, wearable electronics, and biomedical devices.
Variable recruitment of actuator elements spanning micro- to macroscale volumes to modify their isometric and isotonic force-velocity profiles is one of the more intriguing contrasts between natural muscles and motors that power today's equipment.
Thermomechanical liquid crystal elastomers (LCEs) are among the candidate actuation schemes that are most appealing because they naturally exhibit variable recruitment, localised actuation, mechanical compliance, and have been reported to apply contractile stresses resembling those of natural muscle.
The Global Liquid Crystal Glass Transfer Robot Market accounted for $XX Billion in 2021 and is anticipated to reach $XX Billion by 2030, registering a CAGR of XX% from 2022 to 2030.
The primary unit of NIDEC SANKYO's SR8651 liquid crystal glass transfer robot features various end effector types to accommodate various temperature needs, simple maintenance or driving units with a module construction a long Z-stroke that allows access to up to a three-layer load lock, Small and light controllers with a standard design for simple maintenance.
Sankyo's original cooling system was designed to withstand extreme temperatures. R-axis unit and manipulator are easily detachable for straightforward installation and maintenance, seramic hands ready for a great moment, For arm drive units, high-precision components and hybrid beads are used.
The world's largest shipbuilder by assets, Hyundai Heavy Industries Co., Ltd. (HHI), has been successful in localising the manufacture of fourth-generation LCD glass transfer robots. Since the size and form of the robot must change depending on the size (generation) of the LCD panel, HHI's LCD transfer robots require extremely advanced technology.
Keeping fine particle concentrations in the production process below 10 particles per 1 m3 is essential to preventing LCD panels from suffering irreparable damage.
Sl no | Topic |
1 | Market Segmentation |
2 | Scope of the report |
3 | Abbreviations |
4 | Research Methodology |
5 | Executive Summary |
6 | Introduction |
7 | Insights from Industry stakeholders |
8 | Cost breakdown of Product by sub-components and average profit margin |
9 | Disruptive innovation in the Industry |
10 | Technology trends in the Industry |
11 | Consumer trends in the industry |
12 | Recent Production Milestones |
13 | Component Manufacturing in US, EU and China |
14 | COVID-19 impact on overall market |
15 | COVID-19 impact on Production of components |
16 | COVID-19 impact on Point of sale |
17 | Market Segmentation, Dynamics and Forecast by Geography, 2022-2030 |
18 | Market Segmentation, Dynamics and Forecast by Product Type, 2022-2030 |
19 | Market Segmentation, Dynamics and Forecast by Application, 2022-2030 |
20 | Market Segmentation, Dynamics and Forecast by End use, 2022-2030 |
21 | Product installation rate by OEM, 2022 |
22 | Incline/Decline in Average B-2-B selling price in past 5 years |
23 | Competition from substitute products |
24 | Gross margin and average profitability of suppliers |
25 | New product development in past 12 months |
26 | M&A in past 12 months |
27 | Growth strategy of leading players |
28 | Market share of vendors, 2022 |
29 | Company Profiles |
30 | Unmet needs and opportunity for new suppliers |
31 | Conclusion |
32 | Appendix |