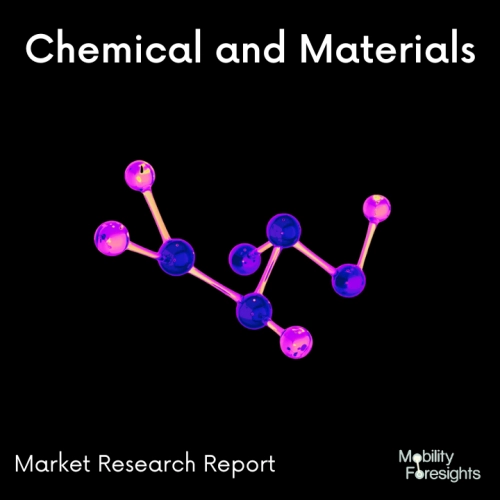
- Get in Touch with Us
Last Updated: Apr 25, 2025 | Study Period: 2024-2030
Liquid silicone rubber (LSR) is a thick liquid polymer that is produced using a clean liquid injection molding technique to create components. The most stable LSRs are two-part, platinum-cured polymers, which are employed in liquid injection molding. For manufacturing precise, fragile components, LSR liquid injection molding is the best technique.
Precision, accuracy, and high output are all features of the clean process. Products with improved durability and performance are produced when the LSR qualities are combined with the clean liquid injection molding manufacturing technique.
The Global Liquid Silicone Rubber Injection Moulding Machine market accounted for $XX Billion in 2023 and is anticipated to reach $XX Billion by 2030, registering a CAGR of XX% from 2024 to 2030.
Dow introduced SILASTICTM Liquid Silicone Rubber (LSR), which was first offered in the market for rubber manufacture. SILASTICTM F-LSR is a novel fluorinated LSR that Dow just launched. This new rubber has the performance characteristics of an FSR while still being a real LSR.
This indicates that it can endure the high temperatures and harsh solvent environments seen in contemporary automobile and aerospace engines.
Numerous current and new applications take advantage of the processing and product benefits of SILASTICTM LSRs. Both for general applications and for particular requirements, a wide product line is available. Additionally, a lot of brand-new uses for the new SILASTICTM F-LSRs are quickly emerging.
The SILASTICTM LSRs and F-LSRs are liquids with a range of viscosities, from paste to easily poured. These two-component materials, which typically use a 1:1 ratio, are made of copolymers or polysiloxane polymers that are vulcanised using polyaddition.
F-LSRs also include fluorine. SILASTICTM LSR and F-LSR are offered in 200-litre drums or 20-litre pails as lot-matched kits. The density of the product determines the precise package weight. Injection moulding, fabric coating, dipping, and extrusion coating operations all frequently employ SILASTICTM LSRs.
The automobile, aircraft, appliance, business machine, electrical, and consumer industries are only a few of the many application areas.
Sl no | Topic |
1 | Market Segmentation |
2 | Scope of the report |
3 | Abbreviations |
4 | Research Methodology |
5 | Executive Summary |
6 | Introduction |
7 | Insights from Industry stakeholders |
8 | Cost breakdown of Product by sub-components and average profit margin |
9 | Disruptive innovation in the Industry |
10 | Technology trends in the Industry |
11 | Consumer trends in the industry |
12 | Recent Production Milestones |
13 | Component Manufacturing in US, EU and China |
14 | COVID-19 impact on overall market |
15 | COVID-19 impact on Production of components |
16 | COVID-19 impact on Point of sale |
17 | Market Segmentation, Dynamics and Forecast by Geography, 2024-2030 |
18 | Market Segmentation, Dynamics and Forecast by Product Type, 2024-2030 |
19 | Market Segmentation, Dynamics and Forecast by Application, 2024-2030 |
20 | Market Segmentation, Dynamics and Forecast by End use, 2024-2030 |
21 | Product installation rate by OEM, 2023 |
22 | Incline/Decline in Average B-2-B selling price in past 5 years |
23 | Competition from substitute products |
24 | Gross margin and average profitability of suppliers |
25 | New product development in past 12 months |
26 | M&A in past 12 months |
27 | Growth strategy of leading players |
28 | Market share of vendors, 2023 |
29 | Company Profiles |
30 | Unmet needs and opportunity for new suppliers |
31 | Conclusion |
32 | Appendix |