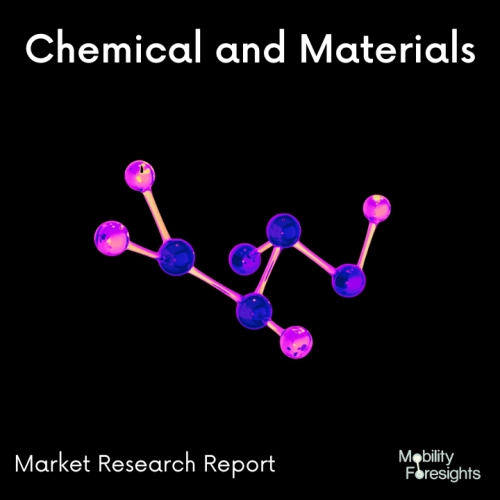
- Get in Touch with Us
Last Updated: Apr 25, 2025 | Study Period: 2024-2030
A specialised material used in the manufacture of lithium-ion batteries is lithium battery aluminium laminated film, sometimes referred to as lithium-ion battery aluminium foil. The film is usually produced from an aluminium foil layer that has a thin coating of a polymer, like polyethylene or polypropylene, coated on top.
The aluminium laminated film's function is to act as a barrier between the battery's positive and negative electrodes while also facilitating the movement of lithium ions during charging and discharging.
The film must be both thin and flexible enough to enable effective packing of the battery cells and strong and resilient enough to endure the rigours of repeated charging and discharging cycles.
Lithium battery aluminium laminated film has a number of important qualities, including:
The performance, dependability, and safety of these significant energy storage devices are enhanced by the use of lithium battery aluminium laminated film, which is an essential part of high-quality lithium-ion battery architecture.
Solid state batteries as well as current Lithium-ion batteries all require the lithium battery aluminium films in order to ensure best stability under harsh real world use cases of the battery as it is these films that make the batteries safe for consumer use.
TheGlobal âLithium Battery Aluminum Laminated Film marketaccounted for $XX Billion in 2022 and is anticipated to reach $XX Billion by 2030, registering a CAGR of XX% from 2024 to 2030.
A secondary lithium-ion rechargeable battery with a manganese laminate has started to be sold by NEC Mobile Energy Corp. in Tokyo, Japan. The business strives to satisfy consumer demand for mobile terminal devices with a compact design, such as cell phones and PDAs.
Instead of the usual aluminium and iron packing, the batteries use a laminate film, which results in a smaller size. The battery's internal content was boosted by the use of innovative packaging, which also improved the electrolytic composition.
This resulted in a greater energy density of 150Wh/kg, a 25 percent improvement above the 120Wh/kg typical of conventional batteries.
Researchers from Yokohama National University in Japan have created a stretchable packaging film with a high gas and moisture barrier capability for these batteries, bringing us that much closer to the idea of highly deformable batteries being a common technology in wearable devices.
Sl no | Topic |
1 | Market Segmentation |
2 | Scope of the report |
3 | Abbreviations |
4 | Research Methodology |
5 | Executive Summary |
6 | Introduction |
7 | Insights from Industry stakeholders |
8 | Cost breakdown of Product by sub-components and average profit margin |
9 | Disruptive innovation in the Industry |
10 | Technology trends in the Industry |
11 | Consumer trends in the industry |
12 | Recent Production Milestones |
13 | Component Manufacturing in US, EU and China |
14 | COVID-19 impact on overall market |
15 | COVID-19 impact on Production of components |
16 | COVID-19 impact on Point of sale |
17 | Market Segmentation, Dynamics and Forecast by Geography, 2024-2030 |
18 | Market Segmentation, Dynamics and Forecast by Product Type, 2024-2030 |
19 | Market Segmentation, Dynamics and Forecast by Application, 2024-2030 |
20 | Market Segmentation, Dynamics and Forecast by End use, 2024-2030 |
21 | Product installation rate by OEM, 2023 |
22 | Incline/Decline in Average B-2-B selling price in past 5 years |
23 | Competition from substitute products |
24 | Gross margin and average profitability of suppliers |
25 | New product development in past 12 months |
26 | M&A in past 12 months |
27 | Growth strategy of leading players |
28 | Market share of vendors, 2023 |
29 | Company Profiles |
30 | Unmet needs and opportunity for new suppliers |
31 | Conclusion |
32 | Appendix |