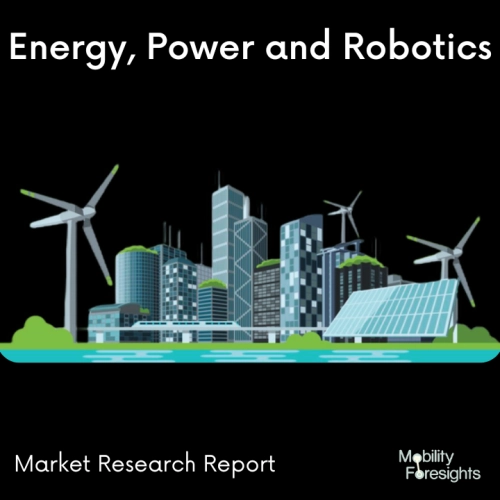
- Get in Touch with Us
Last Updated: Apr 25, 2025 | Study Period: 2024-2030
A specialised piece of machinery used in the manufacture of lithium-ion batteries is the lithium battery electrode coating machine. A thin, uniform layer of active electrode material is applied using the machine to a substrate, which is commonly comprised of copper or aluminium foil.
The substrate is coated by putting it through a succession of rollers and onto a spinning drum. Here, an even, continuous layer of active electrode material is deposited to the substrate's surface.
Before being wound onto a spool and used to create the battery cell, the coated electrode material may first be dried in the machine's drying oven.
For the automated, high-volume production of lithium-ion batteries, lithium battery electrode coating machines are crucial.
They make it possible to efficiently produce lots of coated electrodes with a high level of accuracy and uniformity, which is essential for guaranteeing the functionality and security of the final battery.
Among its essential characteristics is a machine for coating the electrodes of lithium batteries.
Lithium battery electrode coating machines are a crucial part of the automated lithium-ion battery manufacturing process because they enable the efficient and accurate production of high-quality battery electrodes.
TheGlobal Lithium Battery Electrode Coating Machine Marketaccounted for $XX Billion in 2023 and is anticipated to reach $XX Billion by 2030, registering a CAGR of XX% from 2024 to 2030.
An innovative coating method developed by scientists at Germany's esteemed Karlsruhe Institute of Technology (KIT) makes lithium-ion battery electrodes at a record-breaking rate. The new method, according to the researchers, lowers production costs while simultaneously enhancing electrode quality.
When creating battery electrodes, a thin paste of electrode material is placed in a rectangular pattern on copper or aluminium foil. In order to facilitate electron discharge, a few short pieces of foil are left uncoated.
Battery manufacturers must continually stop and start the coating process to create these bare regions. It might be challenging to create crisp edges at maximal production speeds without spreading the material.
Amperex Technology Limited (ATL) and AM Batteries (AMB) will collaborate to develop a solvent-free electrode manufacturing method for lithium-ion batteries.
Sl no | Topic |
1 | Market Segmentation |
2 | Scope of the report |
3 | Abbreviations |
4 | Research Methodology |
5 | Executive Summary |
6 | Introduction |
7 | Insights from Industry stakeholders |
8 | Cost breakdown of Product by sub-components and average profit margin |
9 | Disruptive innovation in the Industry |
10 | Technology trends in the Industry |
11 | Consumer trends in the industry |
12 | Recent Production Milestones |
13 | Component Manufacturing in US, EU and China |
14 | COVID-19 impact on overall market |
15 | COVID-19 impact on Production of components |
16 | COVID-19 impact on Point of sale |
17 | Market Segmentation, Dynamics and Forecast by Geography, 2023-2030 |
18 | Market Segmentation, Dynamics and Forecast by Product Type, 2023-2030 |
19 | Market Segmentation, Dynamics and Forecast by Application, 2023-2030 |
20 | Market Segmentation, Dynamics and Forecast by End use, 2023-2030 |
21 | Product installation rate by OEM, 2023 |
22 | Incline/Decline in Average B-2-B selling price in past 5 years |
23 | Competition from substitute products |
24 | Gross margin and average profitability of suppliers |
25 | New product development in past 12 months |
26 | M&A in past 12 months |
27 | Growth strategy of leading players |
28 | Market share of vendors, 2023 |
29 | Company Profiles |
30 | Unmet needs and opportunity for new suppliers |
31 | Conclusion |
32 | Appendix |