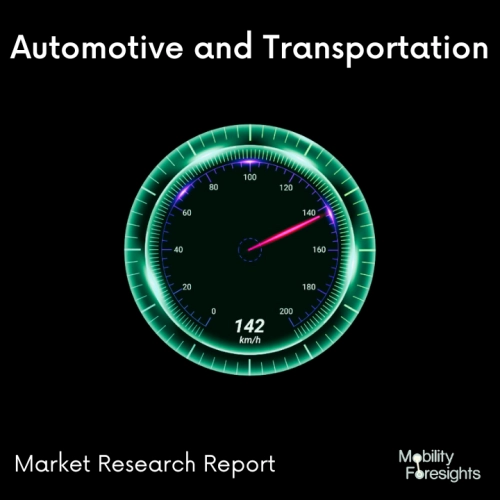
- Get in Touch with Us
Last Updated: Apr 25, 2025 | Study Period: 2024-2030
A thin layer of an electrically non-conductive ceramic composition is applied to a porous polymer sheet or membrane, and it conforms to all of the membrane's surfaces, including the pore surfaces.
A lithium ion battery can use a coated membrane like this as an intra-cell separator, for instance. The coating keeps the electrolyte in place while improving the mechanical and thermal stability of the separator during battery operation.
Atoms of one or more metals, such as aluminium, calcium, magnesium, titanium, silicon, and/or zirconium, may be deposited in a conformal layer on the surface of the workpiece during a two-step vapour-phase process to create the coating.
The surface-forming non-conductive nitrides, carbides, and/or oxides of the metal atoms may then be produced by reacting them with ammonia, carbon dioxide, and/or water.
A porous polymer separator membrane for a lithium-ion battery, with opposing sides that have surfaces and open pores that connect the sides of the membrane, the pores having surfaces; and all of the separator's surfaces having a coextensive coating of separately and sequentially applied molecular layers of an electrically resistive ceramic material that conforms to the separator's surfaces without sealing the open pores.
The porous polymeric separators used in the manufacturing of lithium-ion batteries are the subject of this invention.
The application of conformal, ceramic coatings that are electronically non-conductive to the surfaces of such separators, including their pore surfaces, is the focus of this invention in more detail.
Such surface-conforming coatings reinforce and safeguard the separators while maintaining the separator's porosity for electrolyte retention and operation.
Because of its high energy-to-weight ratios, lack of memory effect, and gradual self-discharge while not in use, lithium-ion secondary batteries are frequently used in portable consumer electronics.
In order to power electric motors that move wheels on vehicles, rechargeable lithium-ion batteries are also being developed and manufactured for use in automotive applications.
The anode, cathode, and electrolyte that make up the battery's cells are three functional components that are present in lithium-ion batteries in a variety of sizes and configurations.
The cathode on charge changes into the anode on discharge, and the reverse is true as well. Lithium ions are often passed reversibly between a negative electrode and a positive electrode to power a lithium-ion battery. On opposing sides are where the negative and positive electrodes are located.
The Global Lithium-Ion Battery Ceramic Coated Separator market accountedfor $XX Billion in 2023 and is anticipated to reach $XX Billion by 2030, registering a CAGR of XX% from 2024 to 2030.
In order to create ceramic-coated separators for lithium-ion cells, sulfonated SiO2 particles with poly lithium 4-styrenesulfonate in their shell are manufactured and employed as coating materials.
The combination of a heat-resistant silica with hydrophilic poly lithium styrenesulfonate gives the ceramic-coated separators excellent thermal stability and wettability for liquid electrolyte.
The cycling capabilities of lithium-ion batteries made up of a carbon negative electrode and a positive electrode are assessed utilising these ceramic-coated separators.
When compared to cells produced with polyethylene separators, those assembled with ceramic-coated separators exhibit better cycling performance.
Lithium-based batteries are attractive and prospective energy storage technologies in a variety of industries, including new-energy vehicles and portable electronic equipment.
Separator plays a crucial function in ensuring the longevity of batteries by acting as a solid bridge for ion movement as well as a physical barrier between electrodes.
Unfortunately, in order to combine battery safety and performance, the majority of studies in the field of lithium-based batteries have primarily concentrated on separators between 20 and 25 m.
However, such thick separators reduce the amount of available space inside the battery for accommodating active components, which hinders the future development of next-generation lithium-based batteries with high energy densities.
Sl no | Topic |
1 | Market Segmentation |
2 | Scope of the report |
3 | Abbreviations |
4 | Research Methodology |
5 | Executive Summary |
6 | Introduction |
7 | Insights from Industry stakeholders |
8 | Cost breakdown of Product by sub-components and average profit margin |
9 | Disruptive innovation in the Industry |
10 | Technology trends in the Industry |
11 | Consumer trends in the industry |
12 | Recent Production Milestones |
13 | Component Manufacturing in US, EU and China |
14 | COVID-19 impact on overall market |
15 | COVID-19 impact on Production of components |
16 | COVID-19 impact on Point of sale |
17 | Market Segmentation, Dynamics and Forecast by Geography, 2024-2030 |
18 | Market Segmentation, Dynamics and Forecast by Product Type, 2024-2030 |
19 | Market Segmentation, Dynamics and Forecast by Application, 2024-2030 |
20 | Market Segmentation, Dynamics and Forecast by End use, 2024-2030 |
21 | Product installation rate by OEM, 2023 |
22 | Incline/Decline in Average B-2-B selling price in past 5 years |
23 | Competition from substitute products |
24 | Gross margin and average profitability of suppliers |
25 | New product development in past 12 months |
26 | M&A in past 12 months |
27 | Growth strategy of leading players |
28 | Market share of vendors, 2023 |
29 | Company Profiles |
30 | Unmet needs and opportunity for new suppliers |
31 | Conclusion |
32 | Appendix |